Energy Efficiency in the Quarrying Industry
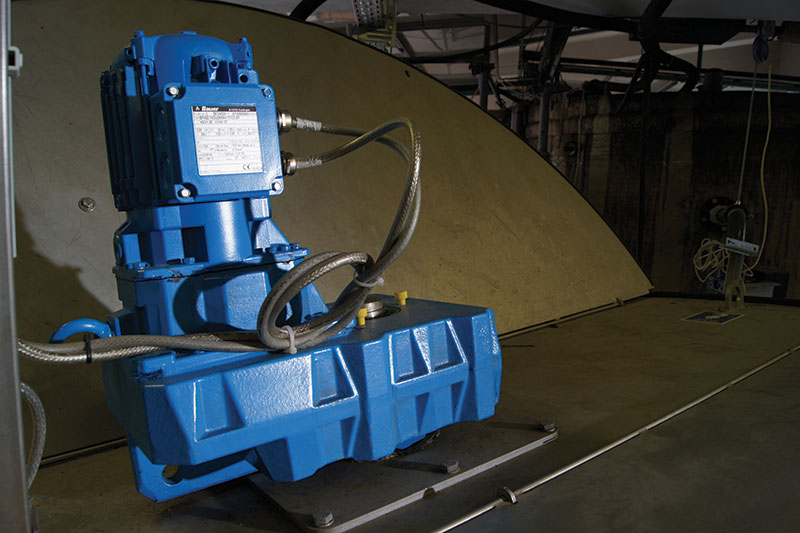
First published in the October 2014 issue of Quarry Management as Integrated Solutions
Energy efficiency may be high on the agenda in the quarrying industry, but without fully understanding all the components within a drivetrain, only a fraction of the potential savings can be realized. Philip Crowe, marketing manager with Bauer Gear Motor GmbH, explains
In today’s market, energy efficiency is one of the key determining factors when specifying geared motor solutions. Energy prices are only going to go one way, so it is important that a drive’s lifelong running costs are considered, rather than simply the cost of procurement, which is why Bauer have developed their new motor range in anticipation of the soon-to-be-implemented IE4 super-premium-efficiency classification, to offer customers the very best in terms of efficiency.
The IE2 regulations effectively cleaned-up the lower-efficiency end of the motor market. If an application requires a motor to operate rarely, then its energy consumption is not so critical; users just want the cheapest machine they can buy that will be reliable in that application. The IE2 regulations are intended to make sure that new motors being supplied into these conditions meet a minimum standard of efficiency.
IE4 is something many manufacturers are talking about but fewer are actually delivering. There is a cost premium to these motors, but the market uptake is not being driven by legislation, rather by shear economics. For a small-to-medium-sized electric motor that is running close to capacity for the majority of the time, used in a continuous manufacturing process for example, the additional investment in terms of purchase cost is quickly outweighed by the energy saving.
Motors that meet IE4 energy-efficiency standards, such as Bauer’s permanent magnetic synchronous motor (PMSM) range, can achieve an efficiency in the order of 96% and have the potential to achieve energy savings of up to 40% compared with an IE2 inverter-driven squirrel cage motor. The environmentally friendly PMSM series design offers a number of other key benefits: it reduces heat losses from the rotor by 100% and total losses by approximately 25%; and it increases total efficiency by 10% or more. For the PMSM user, this improved performance translates into lower total cost of ownership, a reduction in CO2 emissions, and ongoing savings that buffer against future increases in energy costs.
PMSM’s offer considerably improved efficiency when compared with induction motors, even under partial-load conditions, and extremely high efficiency under rated operating conditions. They also have considerably higher power density, which, for geared motors, yields higher system efficiency with minimal installation volume – and also reduced weight. Importantly, PMSM drives can produce higher torques for the same installation volume as conventional induction motors, a factor that allows cost savings through the ability to specify a smaller motor size in some applications.
Bauer have invested a considerable amount of design and development time into ensuring that their PMSM motor and drive packages deliver high-efficiency performance on partial loads, a criticism that has been levelled at other permanent magnet designs as the efficiency can drop off sharply outside the ideal operating speed and load. Bauer’s PMSM motors maintain high efficiency levels within a wide partial load range, up to a load factor of 1:5.
Since the motors can deliver both efficiency and flexibility, the combination of these features with a compact size and high torque rating means that they can be used to cut inventory significantly for large plants and third-party stock facilities. Offering a replacement for a wide variety of different asynchronous geared motors in the field can result in a further reduction in costs for inventory, logistics and maintenance.
The synchronous design of the PMSM motors means that not only are they better at converting electrical energy into mechanical power, but they also offer the benefit of maintaining constant speed, independent of the load. This means that motor speed does not vary, despite overload variations or in cases of voltage drop, as long as the mains frequency is kept constant. The series is available in ventilated and non-ventilated configurations across the power range from 0.55kW to 15kW and they operate on 380V to 500V power supplies. They are rated for inverter duty, offering an extended speed range with constant torque, and their low operating and maintenance costs mean they provide an optimum energy-saving drive for use on fans, pumps and compressors, and for constant-torque applications such as elevators and conveyors.
Efficient drivetrain integration
Depending on the industry, environment and requirements of any given application, there are many different methods of transferring power from mains supply to machine. But no matter what the layout of the drivetrain, there will always be some solutions that offer smoother integration and better efficiency than others. Bauer supply electro-mechanical application solutions that guarantee every component is hand-picked for the application and integrated as efficiently as possible.
Currently, energy efficiency is a hot topic across every industry, but without fully understanding all the components within the drivetrain, only a fraction of the potential savings can be realized. Throughout the drivetrain the potential energy savings are distributed via the ZVEI model:
- 10% via improved efficiency of the motor
- 30% via electronic speed regulation
- 60% via optimization of the mechanical system.
This highlights the fact that while the current focus on energy-efficient motors is important, it is even more important that engineers do not lose sight of the other areas where improvements can be made.
Bauer are committed to delivering the best solution possible for any given application, by maximizing the savings potential across each of the three fields listed above. This means long-term reliability, low maintenance costs and the best energy efficiency possible.
Where do potential savings lie? Bauer’s approach to optimization is to adapt and simplify every aspect of the drivetrain – ensuring that it integrates seamlessly with the machine
Motors – 10% of potential saving
Recent technological advances in motor design have allowed manufacturers to deliver radical improvements in energy efficiency. Coupled with the recent IE2 and IE3 regulation – and the future IE4 regulations – this means that most applications are already benefitting from improved electrical efficiency. A recent comparison test of a standard IE2 asynchronous motor and a Bauer IE4 super-premium-efficiency motor showed that energy savings of more than 40% are possible.
All of the company’s motor competencies – from design to manufacture – are maintained in house, which gives it autonomy over the quality of the product that goes into its drivetrain packages. The company offers a full complement of products for all the energy classes, providing a wealth of choice for any application.
Speed control – 30% of potential saving
Using a speed-control device to monitor the required output of the motor and regulate its energy use accordingly is well known to be a quick and simple way of increasing the efficiency of a system. Depending on the requirements of the application, there are many different control and monitoring concepts which may offer the best combination of cost and efficiency.
Mechanical optimization – 60% of potential saving
While motor efficiency and speed control currently enjoy the majority of media coverage, the fact is that mechanical optimization accounts for the majority of potential savings in most existing drivetrain solutions. The opportunities are actually so vast that Bauer have split this aspect into two further sub-categories: gear technologies; and drivetrain optimization.
Bauer have been manufacturing gear technologies since 1927 and throughout these nearly 90 years they have always strived to offer the most efficient and reliable solutions possible. To best service this aim they have developed a standard, modular gear programme as well as a bespoke design and manufacturing service.
Modular models include the helical BG series, parallel shaft BF series, bevel BK series and worm-drive BS series; each series includes low-torque products (<100NM) to avoid unnecessary oversizing. The range also includes application-specific models with unique features and capabilities designed for the specialist requirements of differing environments.
Each product is specified by application experts to optimize for the specific application in terms of energy efficiency, smoothness, noise, impact resistance and other attributes. Where bespoke solutions are required, Bauer lay claim to providing the shortest time to market possible thanks to continued investment in their rapid prototyping capabilities.
Drivetrain optimization is the last piece of the puzzle, but no less important than the considerations that have come before it. Once each aspect of the drivetrain has been specified, it must then be integrated into the machine with as much efficiency as possible. This requires an in-depth understanding of the drivetrain as well as the specific demands of a given industry.
Simple installation solutions, such as gearing that takes over the bearing functions, thus reducing the number of components, can offer improvements in efficiency that are equivalent to the step up between an IE1 and an IE4 motor in the same drivetrain. As part of Altra Industrial Motion, Bauer are able to work closely with the Altra Coupling division, which includes brands such as Bibby, Huco and Ameridrives, to specify coupling solutions which integrate the drivetrain with minimal energy loss.
Thanks to its completely modular design, Bauer’s standard product range offers thousands of potential drivetrain packages while, for more specialist applications, the company’s Specialist Serial Demand service can build a completely bespoke design which is integrated into the machine from the ground up, the aim being to maximize the potential energy savings at every stage of specification and installation to deliver the best-possible solution to each individual application.
For further information visit: www.bauergears.com
- Subscribe to Quarry Management, the monthly journal for the mineral products industry, to read articles before they appear on Agg-Net