Compressor Compliance
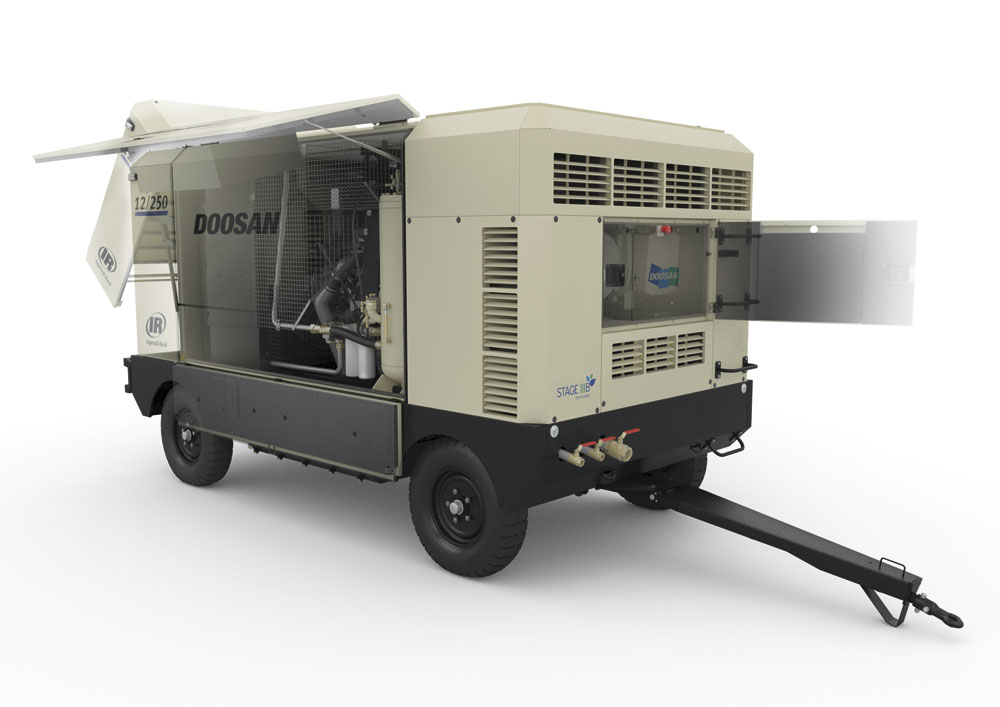
Doosan develop new Stage IIIB-compliant compressors
Since 1996 the European Commission has been working to address exhaust emissions through European Directive 97/68/EC, which focuses predominantly on reducing particulate matter (PM) or ‘soot’, and oxides of nitrogen or ‘NOx’ emissions, the primary contributors to the formation of smog.
Emissions milestones
Several milestones have already been achieved in meeting the EU regulations. Stage I reduced nitrogen oxide (NOx) emissions from diesel machines. In Stage II, the focus was on NOx hydrocarbons (HC) and PM, while Stage IIIA demanded a further reduction in NOx. In order to meet the requirements of these three Stages, all manufacturers reduced PM by 65% and NOx by 60%.
Stage IIIB regulations, which apply to equipment powered by diesel engines of 37kW and above, are being introduced in 2012 and 2013. In addition to those in Europe, various measures are being phased in throughout the US, Canada and Japan. Stage IIIB corresponds approximately to Tier 4 Interim in the US. However, EU Stage IIIB compliance will only be certified for Europe and will not be valid in the US and vice versa.
As a leading global provider of portable air compressors, Doosan Portable Power have been developing emissions-related product innovations since 1997 to meet the successive stages in the European emissions regulations. Each subsequent change has brought on new technologies to achieve the required reductions in harmful exhaust emissions.
From Stages I to IIIA, a number of core improvements have been applied to equipment, including turbo-charging, optimization of the engine combustion system and the use of high-pressure, common-rail (HPCR) fuel-injection systems.
A highly efficient fuel-injection system is essential for the clean operation of a diesel engine. HPCR is an advanced fuel-injection system that better regulates fuel pressure and injection timing. In HCPR systems, high pressure transforms the fuel into an extremely fine mist as it leaves the injectors. In this form it combusts more thoroughly, leading to lower costs as the fuel burns more completely and the engine needs less of it to run.
HPCR units provide a cleaner exhaust as less unburned fuel is left behind in the exhaust. They also deliver improved performance – multiple injections in each combustion cycle mean that combustion lasts longer, creating more energy and further output from the engine.
Increased comfort is another benefit because longer-lasting combustion lowers peak engine cylinder pressure. This reduces engine noise levels, making operation more comfortable.
HCPR is already used extensively on the high-output engines in the Doosan Portable Power range and the company says the associated electronic control unit technology will be instrumental in meeting Stage IIIB and Stage IV demands.
Portable compressor compliance
Following Stage IIIA, Stage IIB requires a further reduction of 90% in PM and 50% in NOx. Stage IV will come into effect in 2014 and will reduce NOx by an additional 80%, almost completely eliminating both PM and NOx emissions.
The Stage IIIB regulations for compressors (with engines from 130 to 560kW) came into force during 2011. Those with the engine power range from 56 to 129kW will become effective in 2012. The process continues in 2013 with Stage IIIB regulations being introduced for portable compressors in the 37–55kW range. In 2014 compliance with Stage IV regulations begins, starting with the 136–560 kW compressors and then running through to the new 37–55kW models in 2016.
The demands for compliance with Stage IIIB in portable compressors also vary according to engine horsepower. Doosan compressors alone range from 17 to 403kW (23 to 540hp) and, as a result, the extent and types of the changes to the machines will be different across the whole range.
With the changes required to meet the new regulations, Doosan Portable Power took the opportunity to start work on the new designs from a ‘clean sheet of paper’. Throughout the product development process, Doosan’s primary task has been to combine Stage IIIB engine technology with advanced features and developments in the new-generation compressors that will significantly increase all previous levels of performance, fuel efficiency, reliability, durability and serviceability.
The company has worked closely with engine manufacturers to maintain a clear overview of the technology path they have selected for Stage IIIB and the challenges these pose in using this technology. To meet this challenge, Doosan utilized the company’s core competency in packaging diesel engines for use in severe-duty applications, such as those found in the construction, rental and oil and gas industries, to apply the requirements of Stage IIIB in order to produce compressors that offer the best service for end-users, equipment dealers and fleet buyers alike.
A key aspect for Doosan has been to make the new technology as transparent to the owner and operator as possible by:
- Maintaining or increasing performance attributes (output, fuel economy, noise levels, power density etc) versus the prior Stage.
- Rigorously testing the new technologies to ensure the reliability demanded by customers.
- Providing the technology interface to simplify operation and diagnostics.
- Providing training support (service, sales and operator) to ensure a smooth and successful transition.
Reducing both NOx and PM pollutants simultaneously, as required by the Stage I-IV directives, presents an interesting challenge as decreasing one of them implies an increase in the other. This is because nitrogen oxides are produced at high temperatures whereas particulate matter occurs at low temperatures.
After thorough research and development work, Doosan Portable Power decided that the best option, based on engineering characteristics and application requirements, was the use of EGR (exhaust gas recirculation) to deliver the best performance and the lowest operating costs for every engine in the range.
Also known as CEGR (cooled exhaust gas recirculation), EGR, which requires enhanced cooling capacity, reduces NOx by recirculating exhaust back into the engine. This dilutes the amount of oxygen in the combustion chamber and lowers the combustion peak temperature. As a result, NOx formation is reduced but PM is increased.
Counteracting this rise means that EGR systems will not be enough on their own to reduce emissions to Stage IIIB levels. Doosan have chosen to combine them with DOC (diesel oxidation catalyst) and DPF (diesel particulate filter) after-treatment systems, which are highly effective in reducing PM. The EGR, DOC and DPF systems are proven and reliable technologies which have become standard for this application and together help to reduce maintenance costs, save on fuel and maximize resale values.
The DOC is a special catalyst that reacts with engine exhaust upon contact, transforming PM emissions in the exhaust into harmless substances such as water and carbon dioxide. The DPF filters engine exhaust to remove PM and consists of a ceramic wall flow filtration system that separates PM from the exhaust. To keep the DPF clean and working efficiently, the high temperature of the exhaust itself is used to burn accumulated PM off the DPF. This semi-automatic cleaning process is called ‘Regeneration’.
New Doosan Stage IIIB compressors
The new Doosan Stage IIIB portable compressors are based on a new common platform, covering five different models with free air deliveries from 21.5 to 30.0m3/min. To meet the new regulations, the compressors are powered by a Cummins QSL9 Stage IIIB engine combining the use of EGR, DOC and DPF after-treatment technologies.
This size of portable compressor is used to provide compressed air for a wide range of drilling and boring machines for quarrying, mining, site investigation, geothermal, mineral exploration and water well construction work. They also cover specialist applications such as abrasive blasting, spray painting and standby/temporary compressed air for industry use.
The Stage IIIB models have been given new designations – 9/275, 9/305, 12/250, 17/240 and 21/220 – to distinguish them from the current Stage IIIA models in the same capacity range (9/270, 9/300, 12/235, 17/235 and 21/215). The new designations will be important for aftermarket and service considerations and customer familiarity, as the two sets of products will be available for some time in 2012 (under agreements approved by the EU).
According to Doosan, the new platform has been designed to exceed ‘voice of customer’ demands by establishing a new benchmark in the marketplace, meeting customers’ daily requirements for high performance, safety, easy servicing and cost efficiency, while operating with minimal negative impact on the environment.
Full specifications are yet to be confirmed, but the pre-series 12/250 model illustrates the innovative new features offered in the new platform of compressors that are designed to offer increased value for money for customers.
One of the most important customer requests is the importance of both compact size and easy serviceability – product features which, by their very nature, normally conflict. However, the new 12/250 model offers the best of both worlds: reduced size (two units can comfortably fit on a typical delivery truck) and unmatched service access (to reduce downtime). Although smaller in size, the new 12/250 model still offers a much higher flow of 25m3/min compared with 23.5m3/min previously.
The 12/250 compressor also has a completely new control system with a full- colour digital display. Manuals in electronic form are available on the digital display and the WiFi interface allows for live streaming of data to operators or the laptop, tablet computer or smartphone of service technicians. Several additional features, such as multiple air outlets, a 110% bunded base, central drains and forklift slots, have also been incorporated as standard in the 12/250 model.
Doosan Portable Power will be showing their new Stage IIIB compressors for the first time, including the new 12/250, at the Intermat Exhibition in Paris from 16 to 21 April 2012.
For more information visit: www.doosanportable.com