A Powerful Impact
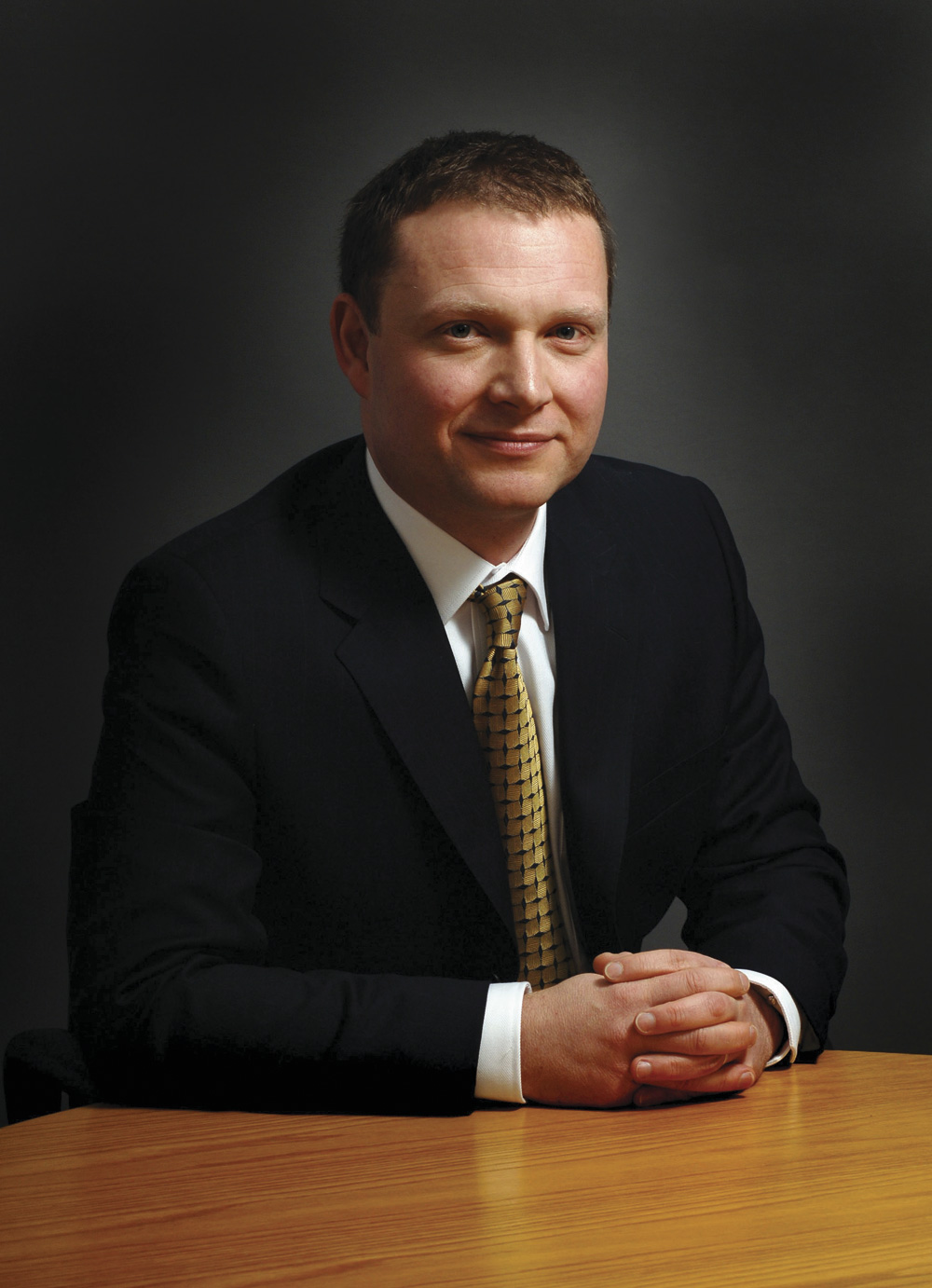
A strategic and sustained approach to the management of power quality can contribute significantly to improvements in energy efficiency
By Jeremy Salisbury, head of marketing at Brammer UK
Many manufacturers may not realize that, much like water, not all power is the same, and that electricity can be ‘clean’ or ‘dirty’. In any industrial environment, the management of power quality is integral, as poor or ‘dirty’ power quality can impact not only on energy efficiency but also on operational and financial performance.
As well as increased electricity consumption, the hidden costs of poor power quality include production downtime caused by the effects of excessive harmonic distortion, excess heat generation and reduced component life, all of which can have high-cost implications for the manufacturer. However, the quality of power supplied only generally becomes an issue when that supply is cut.
Many of the problems of power quality are associated with harmonics. The main reason for a lot of harmonic problems is the way in which current is drawn. Until the last 20 to 30 years, most electrical equipment drew current in a linear fashion, with both the current and voltage waveforms being ‘sinusoidal’ – smooth and repetitive.
However, many modern electrical loads draw current in a ‘non-linear’ fashion, with the current waveform being regular but containing sudden peaks and troughs which can affect power quality.
Harmonic problems can manifest themselves in a variety of forms. One which could affect any manufacturer comes in the area of lighting. Many companies will have already switched to low-energy products in a bid to achieve savings, which can reach 45% depending on the size and type of fitting. However, these savings can be drastically reduced by the effects of harmonic distortion, as high-efficiency lighting products have a total harmonic distortion (THD) of up to 80%. This means any savings achieved could be more than cancelled out by the clean-up costs.
Other effects of harmonic distortion include increased transformer losses, meaning over-sized products have to be specified, adding to both purchase and running costs. Nuisance tripping of circuit breakers is another common and highly irritating problem. Meanwhile, excess heat can cause the breakdown of cable insulation, random thermal tripping of circuit breakers, transformer failures and, in the case of third or triple-n harmonics, neutral overload.
Capacitors can be significantly affected by harmonics. They naturally offer low impedance to high frequencies, absorbing harmonic current, causing them to heat up and so reducing their life expectancy. In addition, combining capacitors with motor or transformer inductance can cause undesirable resonance.
Random logic faults can also occur in microprocessors in any CNC equipment, PLCs, drives, uninterruptible power supplies (UPS) and computers, all of which have the potential to cause major disruption, as does the shorting of silicon-controlled rectifiers (SCRs) found in DC drives, battery chargers and DC power supplies.
Other common harmonic issues include incorrect power readings and the reinjection of harmonic currents into the utility network. The latter is a highly significant issue given the requirements of ENA Engineering Recommendation G5/4-1, which imposes strict limits on the amount of distortion industrial users can place on the UK electricity network.
Industrial customers must comply with G5/4-1 as it forms part of the grid code. The sanctions for non-compliance are severe, and usually result in disconnection of the supply – something that no manufacturer can countenance.
Harmonic reduction devices can be either product-based or site-based. Product-based devices include six- or 12-pulse drives, with choke or blocking filters, and active front-end clean power technology. Site-based solutions include: passive and active filters; surge protection and voltage-reduction technology; isolation transformers; fault level increase bolstering; and correction of the power factor – the ratio of the real power flowing to the load to the apparent power in the circuit.
In an electric power system, a load with a low power factor draws more current than a load with a high power factor for the same amount of useful power transferred. The higher currents increase the energy lost in the distribution system, and require larger wires and other equipment. Because of the costs of larger equipment and wasted energy, electrical utilities will usually charge a higher cost to industrial or commercial customers where there is a low power factor.
Taking action to correct a low power factor is therefore key. This can be achieved through the use of standard capacitors or inductors on linear loads, although standard capacitors should not be used on motors fed by variable- speed drives or soft starters, or on networks with active filters.
For non-linear loads, the choice is usually between either passive power factor correction using a filter, or active power factor correction through a single-stage or multi-stage active power factor corrector, which controls the input current of the load so that the current waveform is proportional to the mains voltage waveform.
De-tuned automatic capacitors should be used at the main switchboard, as these will not resonate, overheat or prematurely fail in the presence of harmonics, will contribute towards power factor correction and, depending on their design, will absorb some 5th harmonic current.
Taking action to reduce voltage can also help contribute to lower electricity costs while reducing the stress on connected equipment, reducing the risk of blackouts and notching – which can cause equipment faults – and extending service life. All electrical equipment manufactured for the UK market after 1995 can be run at voltages as low as 209V. The use of constant-voltage transformers (CVTs) can help to keep voltage within set tolerances, especially on linear loads, with savings of around 15% achievable on power use by reducing voltage from 240V to 220V on the same application.
To ensure optimum power quality, a range of companies offer independent, low-cost surveys, which will identify any areas of concern, suggest how these should be addressed and give an assurance that the site is compliant. They can also advise on the best ways to negate the problems associated with other ‘transient’ impactors on power quality (eg lighting strikes) and provide individual site requirements in the area of electro-magnetic compatibility (EMC).
Implementing any recommendations from such a survey, combined with a strategic and sustained approach to the management of power quality, can contribute significantly to improving efficiency, maintaining productivity and reducing downtime, which, in turn, will lead to significant savings.
For more information visit: www.brammer.co.uk