Wirtgen F-Series takes pole position in Alabama
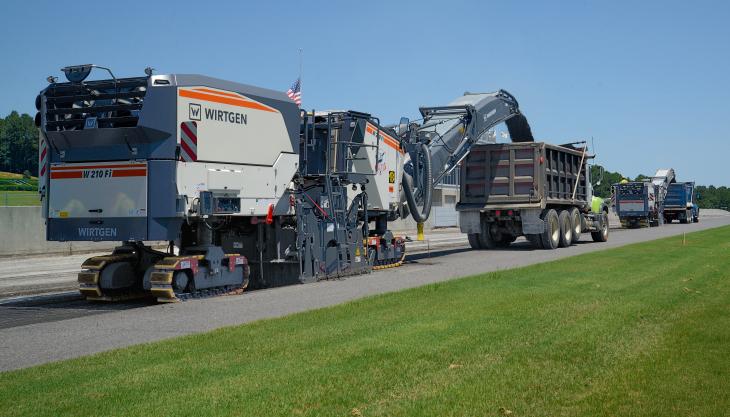
Owner impressed by new-generation large milling machines’ performance and technological innovations
TWO W 210 Fi large milling machines from Wirtgen have claimed a victory during one of their very first jobs on the North American continent, at the famous Barber Motorsports Park in Birmingham, Alabama.
At 766hp, the two large milling machines from Wirtgen can hold their own in the face of the engine power of the race cars and motorcycles that otherwise battle to come in a few hundredths of a second ahead of each other on the 3.7km circuit.
For the rehabilitation of the racetrack on the eastern outskirts of Birmingham, precision and cost-effective milling were required in addition to horsepower and speed, which is why the decision fell on two brand new W 210 Fi milling machines.
Working at different depths depending on the section of track being milled, they removed the asphalt and base layer at depths of up to 18cm over an area of 14,500 sq metres, and fine-milled the asphalt to a depth of between 1.2cm and 10cm on a further 45,000 sq metres.
The milling drums required for this purpose were changed on the milling machines almost as quickly as pit crews change the tyres on race cars – the new Multiple Cutting System making it possible to switch out milling drums of identical working widths but with different tool spacings much more quickly and easily than with other cold milling machines.
For Kim Butler, owner of the contracted milling company, Mill It Up, the changeover was so fast that she seemed to find it hard to believe: ‘It’s incredible. We can change milling drums in eight minutes – I’ve never seen anything like it.’
Equipped with new cutting tools, the W 210 Fi returned to the track. Compared with standard milling drums, fine milling drums have more picks and a smaller tool spacing – in this case 298 picks and 8mm tool spacing.
Fine milling drums are always used when, for instance, ripples and ruts need to be removed from the road surface or when the surface’s grip needs to be improved. In many cases, this eliminates the need to pave a completely new surface layer.
The fine milling method is also used to pave thin asphalt surface layers. In this case, creating a uniform, level milled surface ensures that the new layer bonds perfectly with the existing surface. As a result, fine milling plays a crucial role in determining the quality of the newly paved asphalt – which was the case at the Barber Motorsports Park.
In addition to fine milling, the levelling system also has a significant influence on the milling result. Wirtgen’s latest development, Level Pro Active, was used in Alabama. Because this system is fully integrated into the machine control system, important machine functions are directly linked to each other, ensuring precise milling results.
At the Barber Motorsports Park, the levelling system also played to its strengths when positioning the machine for the second working pass – a process that is actively and precisely supported by Level Pro Active. The result is a milled surface of much higher quality.
The two W 210 Fi machines underlined this on the racetrack in Birmingham, with its 17 different turns. After completing the milling project, Kim Butler expressed her delight with the innovations in Wirtgen’s large milling machines: ‘I’m simply amazed by the technologies,’ she said.
The race car drivers were also extremely impressed by the new road surface. Comments such as ‘smooth as a pool table’ or ‘as smooth as butter’ show that, in addition to the necessary grip, the new surface also exhibits the second most important characteristic for drivers.