Wear issues during the manufacture of titanium dioxide
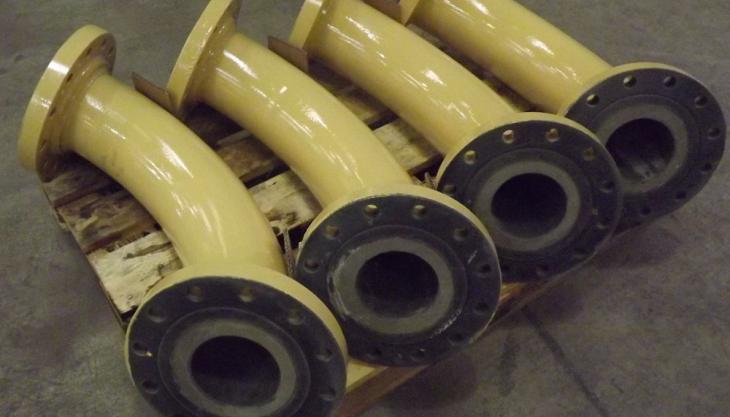
For many years the chemical industry has had an in-depth understanding of corrosion protection and the range of wear-resistant lining systems available. The costs of no or incorrect action can lead to plant degradation, unplanned shutdowns, costly repairs, and potential spillages leading to a breach of environmental legislation.
The industry introduced best engineering practice which lead to formal code of practices (ACoP) that are now adopted as mandatory for the storage and handling of chemical substances.
Ensuring the process is protected using various wear-resistant lining systems and technologies is the key to successful corrosion prevention. Wear-resistant lining specialists Kingfisher Industrial have successfully improved the performance and extended the service life of capital plant and equipment used to store, convey or process minerals in either a mechanical, pneumatic or hydraulic state.
A well known global manufacturer of titanium products were experiencing high levels of production down time and unforeseen maintenance costs. Kingfisher have been supplying the UK plant since the late 1980s when investment was made in the re-engineering of pneumatic conveying pipe work system used to inject recycled ore and coke into a fluidized bed chlorinator.
The process itself uses chloride to convert rutile or ilmenite into titanium tetrachloride which when purified, scrubbed and then oxidized creates pure titanium dioxide (TiO₂). The process depends on the correct balance of mineral and chemical additives and as such the pneumatic injection lines must be active throughout the chlorinator’s operational campaign. Protecting the pipe work from the rigours of conveying ore and coke is, therefore, of the utmost importance. Over the years various grades of wear-resistant steel tubes and refractory-grade ceramic liners were used to combat the amount of degradation that occurred within the pipelines. These systems, albeit achieving improved longevity, were not achieving the life expectancy the engineers and operators desired and the requirement to replace pipe work mid campaign was becoming common practice. This replacement activity was having a detrimental effect on the operation of the chlorinator alongside the risks associated to undertaking mechanical activities within a hazardous area. Engineers therefore turned to Kingfisher in an attempt to improve the life expectancy of the process.
From many years of experience gained through combating the cyclical effects of abrasive minerals conveyed in pneumatic pipe systems, Kingfisher sought to rectify the problem by using their range of ceramic resistant liners. These systems vary from cast basalt, high alumina oxide, silicon carbide and zirconium and all have wear-resistant properties that counter a range of abrasive minerals of certain shapes and sizes. They each perform differently dependent on the operational characteristics of the system, therefore the temperature, velocity and volume per hour needs to be factored into the review to ensure the right system solution is offered.
Kingfisher worked in conjunction with the plant reliability engineers to ensure the system matched the customer expectations with regard to quality, cost and delivery. Within two to three years of trials and inspections, Kingfisher supplied various grades of ceramic liners for testing and upon review of the data it was clearly evident which systems suited what parts of the application. It was decided and supported by real-time evidence that the optimum system consisted of the straight pipes and bends up stream of the safety shut valves, positioned to prevent blow backs from the chlorinator, being protected using 6mm thick 92P K-ALOX high alumina ceramic liners and downstream of the valves being protected with 6mm thick K-SIL RB silicon carbide liners. With the pipes being fabricated in accordance with the pressure equipment directive (PED) they are subject to stringent compliances of NDT on all welded parts and hydro static – pressure testing up to 15 bar being held at 220 psig. This endorses the integrity of the system and meets the customer’s safety and compliance features associated with chemical plants. This system gave the best performance versus investment ratio taking all the factors of product, process and safety into consideration.
The resulting situation is that this system has been adopted by the company as best engineering practice and the plant has benefited from the wear-resisting lining systems. The pipe work after the shut-off valve is changed routinely regardless of the condition and is replaced to guarantee the plant’s 18-month life expectancy between campaigns. It is imperative the company achieves this due to the operation of the chlorinator and forms part of their standard operating procedures when replacing the pneumatic pipe work system. Likewise, this technology has evolved to protect other areas of the process that suffer from material degradation such as cyclones, driers, mills and micronizers.