UK EFW Plant enhances operational efficiency
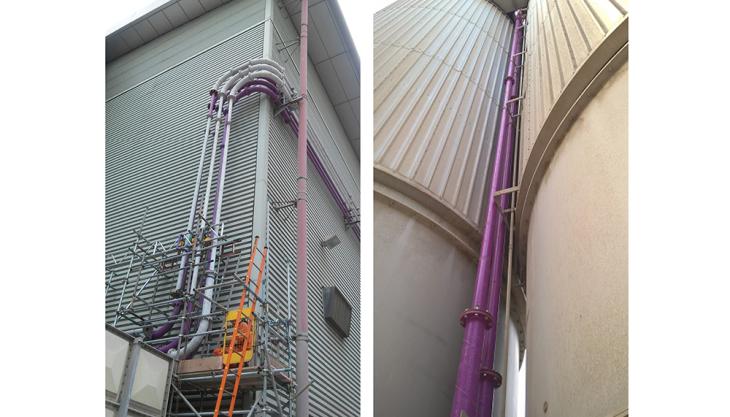
Due to the metaphoric changes happening within the UK’s energy and waste sectors, operators are under extreme pressure to deliver on their obligations in handling, sorting and processing waste in order to generate electricity and avoid diverting waste to landfill.
The need for operational uptime is of utmost importance, therefore plant availability and efficiency is key to achieving contractual commitments as well as stakeholder revenue expectations.
One such renewable energy plant was commissioned in 2009 with a 25 year licence to process both the counties regional domestic and general waste. Throughout the prevailing period, operational efficiency has risen from 77% to 94% and the objective is to achieve 98% efficiency and availability rates. An area that is now been tackled is the ash and dust plant which suffers from both plant degradation and system blockages resulting in the need for the plant to be brought off line to cater for pipe repairs and replacements or the un-blocking of pipes and associated equipment.
Following a visit by the plants engineers to the Resource and Waste Management exhibition (RWM) in 2014, they identified what they perceived to be technology that may assist them in solving the problems they were experiencing. After discussion with industry specialists Kingfisher Industrial, engineers from Kingfisher demonstrated ways were these issues could be alleviated by enhanced routing and sizing design alongside incorporating ceramic technology within the pipe system that would operate trouble free for up to 10 years at present tonnage rates.
After two years of meetings and reviews, the plant secured sufficient budget and buy in from the owners to enhance the existing ash and dust plant conveying systems. A tender document was issued in early spring 2016, where a number of parties were requested to submit their proposal for a full re-design, manufacture and commissioning of an upgraded ash disposal system.
After a thorough contractual, technical and commercial process was undertaken with all tenderers, the decision was made to place an order for circa £1million with Kingfisher who were able to demonstrate a total understanding of the key problem, solution and benefits the customer was looking to achieve.
Utilising their own internal resources, Kingfisher’s operations team visited site and liaised with the technical and operational departments of the client. They identified issues related to the re-design of the system and placed great emphasis on both the system longevity to counter the pipe degradation taking place, along with improving accessibility and directional routing of the piping system to eliminate pressure drops, which was causing the blockages. This created operational up time whilst allowing for ease of access for the plants maintenance and engineering team to carry out routine maintenance and inspection.
Kingfisher launched their K-GUARD boiler protection system last year at RWM 2016, and promoted their very own K-CLAD 800 wear-resistant chromium carbide plate.