Upgraded Cat 966 and 972 loaders
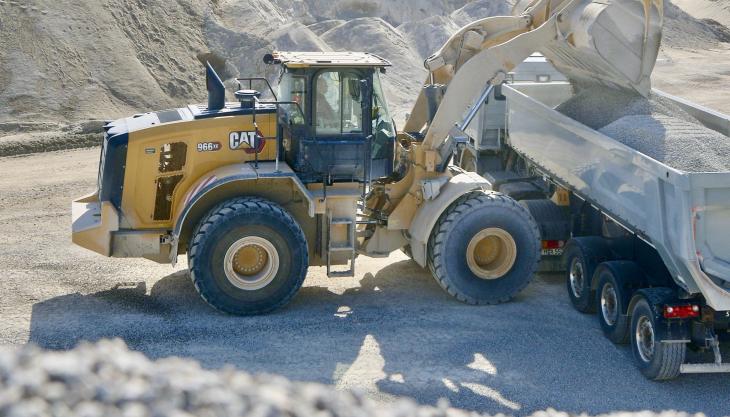
Simple-to-use technologies boost efficiencies and productivity of next-generation wheel loaders
BRINGING a host of standard technologies to the 23–25-tonne wheel loader line, Caterpillar say their updated 966 and 972 models deliver consistently high bucket fill factors to increase productivity by up to 10%, whilst the machines’ next-generation design extends fluid and filter change intervals to reduce maintenance costs by up to 20% compared with the previous models.
The Caterpillar designed and manufactured continuous variable transmission (CVT) of the next-generation Cat 966 XE and 972 XE loaders improves fuel efficiencies by up to 35%, compared with the previous powershift models, whilst prolonged service intervals plus efficiencies gained through the CVT powertrain result in even lower maintenance costs (up to 25%), further reducing total operating costs.
All four models in the updated 966 and 972 loader series feature Cat Payload with Assist as standard for accurate weighing of bucket payloads, so operators can load to target the first time, every time. Real-time data are fed to the operator display and allow a manual tip-off function to improve final bucket adjustments and truck load accuracy.
The new Cat Autodig with Auto Set Tires delivers consistently high bucket-fill factors for the updated medium wheel loaders. Fully automating bucket loading, Autodig improves fill factors and decreases loading time. Working in conjunction with Autodig, Auto Set Tires promotes proper loading techniques to significantly reduce tyre slip and wear.
Offering the ability to set customized profiles for customer-specific applications, new Application Profiles allows multiple machine parameters to be set at the press of a button, to optimize settings for the job. Selectable on-screen Job Aids, along with a streamlined new controls layout, facilitates loader operation, allowing operators of all experience levels to be more productive.
Optional Cat technologies help to further increase productivity and operational profitability of the updated series. Cat Advanced Payload with Assist offers Tip Off Assist to automatically adjust the final bucket load to match hauling unit target, enhanced lists management, site integration, and extended scale features. The available Cat Productivity subscription provides detailed and comprehensive actionable information for the site on a smartphone, tablet, or computer.
Deep system integration of the CVT powertrain, engine, hydraulic, and cooling systems, as part of the next-generation Cat 966 XE and 972 XE design, results in significantly increased performance and fuel efficiency. Without the torque converter of mechanical drive systems, these loaders independently control engine rev/min and machine speed to provide efficient digging, fine control, and operation. Caterpillar say operators will also experience smooth, fast accelerations and high speeds on grade with the CVT design.
Machine manoeuvring on grade is enhanced through speed-hold and anti-rollback features. Delivering optimal loading efficiency in the pile, advanced rimpull control helps to reduce tyre wear, whilst as well as saving fuel, the lower rated engine speed of the XE models will reduce component wear and make for quieter operation.
The next-generation 966 and 972 series design extends maintenance intervals to 1,000 hours and eliminates the 500-hour service intervals, so the loaders spend more time at work. An integrated optional Autolube reduces daily maintenance and increases component service life, whist convenient access to hydraulic and electric service centres makes servicing the loaders fast and easy. Combined, these design updates reduce maintenance costs by up to 20% for the Cat 966 and 972 models, and up to 25% for the 966 XE and 972 XE loaders.
Technology also plays a role in improving loader servicing. Helping to manage fleet location, hours, and maintenance schedules, the Cat App provides alerts for required maintenance and assists with requesting service from the local Cat dealer. Remote Troubleshoot connects the machine to the dealer’s service department via the Internet to quickly diagnose fault codes without on-machine cable connection. Additionally, Remote Flash ensures the wheel loaders are operating with the most up-to-date software, without impacting the production schedule.
The new loaders feature Caterpillar’s next generation of ride control that works as a shock absorber to improve ride quality over rough terrain. In addition, making for a quieter work environment, the cab includes sound suppression, seals, and viscous mounts to decrease noise levels, whilst a wide door that unlocks remotely from the ground, plus inclined steps, improves cab ingress/egress.
Shipped with a seat-mounted electrohydraulic joystick steering system as standard, the next-generation 966 and 972 machines are said to offer precise machine control with minimal arm movements, increased comfort, improved loading accuracy, and more legroom for the operator. An HMU steering wheel is available as an option for the 966 and 972 powershift models.
The loaders’ new dashboard and high-resolution touchscreen display provide intuitive and user-friendly loader control for enhanced performance, whilst multiple air-suspension seat options include heating or heating and ventilation to provide year-round comfort.
Standard monitored seatbelts can be enhanced with an exterior beacon for supervisors to elevate job site safety. Extending from floor to ceiling, the cab windshield improves forward visibility, whilst a standard rear-vision camera and large mirrors with integrated spot mirrors provide superior all-around visibility. Optional Cat Detect radar, to alert operators to hazards, and a multi-view (360°) vision system provide an extra level of safety monitoring around the loaders.
Available in capacities ranging from 2.8 to 14.0 cubic metres, the Cat Performance Series buckets on the new 966 and 972 loader series are said to balance shape against the linkage for higher fill factors and better material retention than other designs with the same rated capacity, whilst Fusion quick couplers permit rapid work tool changes without the operation having to leave the cab, so the loaders move quickly from task to task.
Special, purpose-built options for the loaders include: an aggregate handler configuration that offers higher payload capability for loose aggregate handling applications; and an industrial and waste model that features the guarding and reinforcement required for working at recycling facilities and demolition sites.