Unusual application on the Düte bridge
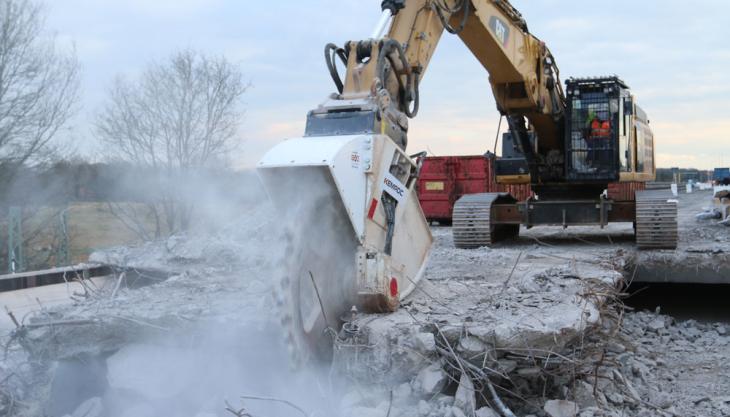
UPEK utilize a Kemroc Erwetor DMW 220 cutter wheel for sensitive bridge demolition project
WHEN the 50-year-old Düte bridge on the A1 Autobahn near Osnabrück, in Northern Germany, had to be replaced with a new structure, the original construction method used meant that demolition of the old bridge was not straightforward.
Built in 1968, the four-lane motorway bridge had eight pairs of supports holding up a single slab of concrete, which was 280m long and 35m wide; made originally from one long, continuous pour.
For this reason, the principal contractors for demolition, groundworks and construction, PORR Deutschland GmbH, had to build a steel structure to support the old bridge before they could start cutting into the concrete deck, the intention being to cut the deck longitudinally into two halves, so that one half could be removed and replaced with a new section before the second half was removed and replaced.
To further complicate matters, the river Düte and a high-speed railway line pass under the old 300m long x 18m high bridge, so certain demolition works could only be completed during operational breaks in the railway schedule. Moreover, the countryside near the bridge is part of a nature reserve, so the use of a long-reach excavator to demolish the bridge from ground level was not possible either.
Subcontractors UPEK GmbH were responsible for the demolition of the 15m wide eastern half of the bridge over the high-speed railway line and they chose to use a Kemroc Erwetor DMW 220 cutter wheel mounted on a 50-tonne excavator for the delicate demolition work.
The procedure involved cutting out segments of the deck approximately one sq m in size. After each square segment was cut, an excavator bucket was used to pull the segment backwards, on to the uncut bridge deck where it was reduced in size using a breaker or concrete shears.
By the end of May 2018, demolition of the bridge section that passed over the high-speed railway line had been completed and demolition of the superstructure using conventional methods had started. However, it was also planned to use the excavator with the Erwetor cutter wheel to demolish the remaining 115cm thick bridge heads and abutments.
In his interim report, general manager Johannes Prues commented: ‘While cutting the 65cm thick concrete road we achieved a cutting speed of 30 metres per hour, which translated into 1m of road demolished per hour.
‘Naturally, tool wear while cutting the heavily re-enforced concrete with contained 32mm diameter tension bars, was enormous. However, we achieved the desired production rate for the difficult task in the very short time frame available due to the high-speed railway operating times.’
For the demolition of the bridge heads and 80–120cm abutments, use of the Kemroc cutter wheels had some very important benefits. ‘The ability of the wheel to cut down to 100cm depths made the demolition of some structures much easier than would have been possible with traditional cutting and sawing techniques,’ explained Mr Prues.
‘In addition, using the cutter wheel on the bridge heads and abutments solved another problem. These structures were also formed from a single pour of concrete and it was only the cutter wheel that made it possible to demolish the eastern half of the bridge without damaging the western half, which remained operational. This would have been very difficult using hammers and shears.’
Meanwhile, UPEK have utilized the Kemroc cutter wheel in other, more conventional applications. ‘On some occasions, the cutter wheel has saved us significant amounts of time in the demolition of buildings and removal of basement walls compared to the use of other excavator attachments,’ said Mr Prues.
‘The Kemroc cutter wheel has become an indispensable problem-solver and time-saver for our company. I purchased the machine after renting it for one month.’