UK lime kiln in world-first net-zero hydrogen trial
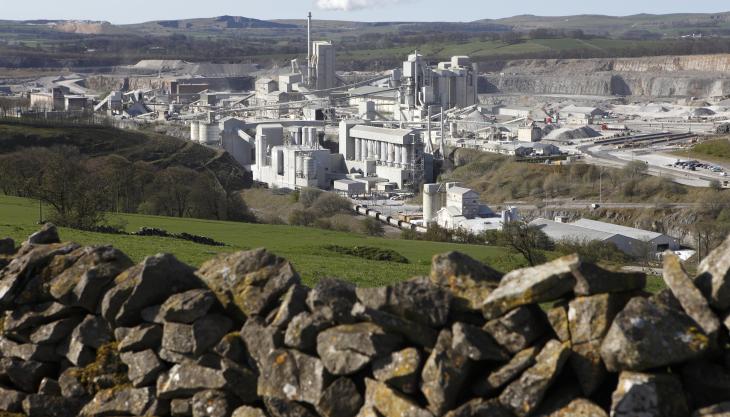
High-quality lime produced successfully at Tarmac’s Tunstead site using hydrogen technology
HIGH-quality lime has been manufactured for the first time in the UK using hydrogen technology as part of a world-first net-zero trial.
The trial, led by Tarmac at their Tunstead site, near Buxton, was the culmination of a project funded by the Department for Business, Energy and Industrial Strategy (BEIS) and demonstrated the significant potential to use hydrogen as a viable fuel alternative to natural gas for commercial-scale production of lime.
Several trials were conducted with differing energy replacements, which culminated in a 100% replacement of natural gas.
Lime is currently manufactured in high-temperature kilns by heating calcium carbonate from limestone to around 1,000°C. Using hydrogen as a fuel ensures that no CO2 emissions are produced from fuel combustion, just water vapour.
Commenting on the innovative trial, Graham Cooper, lime director at Tarmac, said: ‘High-purity limes are essential for our way of life and are used in a diverse range of sectors, from wastewater treatment through to the manufacturing of pharmaceuticals and cosmetics.
‘Lime has been manufactured in the Peak District for centuries and this forward-thinking project aims to ensure the future of this nationally significant industry as the UK transitions to net zero.’
The project builds on the company’s wider long-term sustainability programme and corporate commitment to deliver net zero by 2050 and cut CO2 by 45% per tonne of product by 2030. Over the last five years Tarmac have successfully cut CO2 by 24% per tonne of product, compared with 1990 levels.
Dr Diana Casey, director of energy and climate change at the Mineral Products Association (MPA), which managed the overall project, said: ‘Our sector is committed to ground-breaking collaborative research and innovation to meet the industry’s net-zero objectives.
‘This trial has shown that lime manufacture can and will be part of a future net-zero society. What is needed now is investment and infrastructure development to enable the roll-out of this technology at a commercial scale at sites across the country.’
Greg Hands, Minister for Energy, Clean Growth and Climate Change, said: ‘Backed by £2.8 million in government funding, this project is helping industry move away from fossil fuels and cut energy bills. Developing hydrogen technology is vital to accelerating the UK’s energy independence by boosting clean, home-grown, affordable energy.’
The project has been funded by BEIS as part of its Industrial Fuel Switching Competition and is part of fuel-switching trials managed by the MPA at three sites across the lime and cement sectors.
A second demonstration using hydrogen, meat and bonemeal, and by-products from biodiesel industries was used to fuel a cement kiln’s main burner at a plant in Ribblesdale, Lancashire, as part of the same programme.
A third demonstration, also at Tunstead but on the cement plant, has investigated the use of plasma (electrical) energy to heat the calciner.
The results from these projects will be shared with lime and cement producers and other energy-intensive industries both in the UK and globally as best practice examples, with the aim of spreading and maximizing the environmental benefits of the technology.