SBM launch new 40-tonne-class mobile crushers
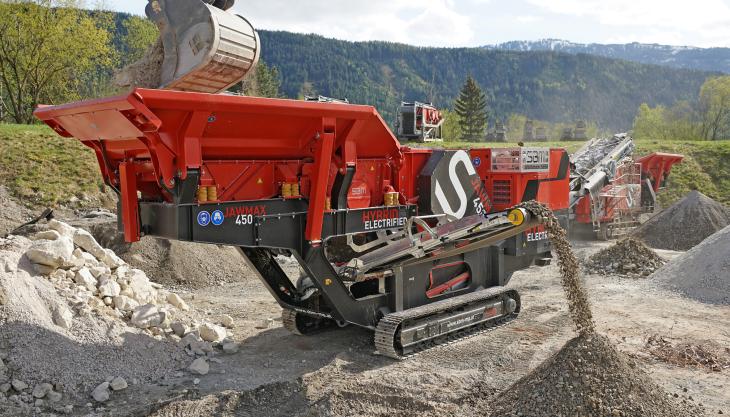
Austrian crusher manufacturer introduces the JAWMAX 400/450 and REMAX 450 models
AUSTRIAN-based SBM Mineral Processing have officially launched their new JAWMAX 400/450 crushers and the newly introduced REMAX 450 impact crusher, expanding their line-up of track-mounted mobile crushers to 10 standard models with operating weights between 30 tonnes and 60 tonnes.
A common feature of both new ‘450’ machines is a high-performance pre-screening unit that helps reduce crusher wear whilst improving the crushing result in terms of quality and output. This new circular-motion, double-deck vibratory pre-screen is directly connected to the vibrating chute in the feed hopper, whilst a triple flap on the screen run allows two fractions to be discharged in full or in part as fines or added to the end product as crusher bypass.
Compared with the double-deck grizzly feeders on the SBM’s ‘400’ models, the pre-screen increases hourly capacity by around 50 tonnes to a maximum of 450 tonnes/h, which is said to position both the 49.2-tonne REMAX 450, with its 1,300mm impact crusher and optional secondary screen, and the compact JAWMAX 450 at the top of their respective performance classes.
Like all SBM mobile crushers, both models have a hybrid diesel-electric/fully electric drive system with optional mains connection. The drive unit consists of an EU Stage V-compliant 6.7-litre Cummins diesel (170kW at 1,500 rev/min) and a 200kVa on-board generator that feeds all electrical drives (feeders, screens, conveyor belts etc) as well as the electrically operated hydraulics for the lifting cylinders and tracks.
According to SBM, the JAWMAX 450 with its independent pre-screen, in particular, sets new standards in terms of economy and practical applicability. A 110kW electric motor drives, via a V-belt, the new STE 110-70 jaw crusher, which was specially developed by SBM for mobile applications.
As one of the largest crushers in the 40-tonne size class, the machine’s 14.35-tonne jaw crusher unit features an inlet opening of 1,100mm x 700mm, accepts a nominal feed size of 0–700 mm, a maximum lump size of 1,000mm x 600mm x 600mm and has the ability to handle rock strengths up to 400MPa, thereby permitting a wide range of applications.
With its 34mm stroke, fully automatically monitored gap adjustment of 40–160mm – which can be adjusted under load, and optional overload protection, the JAWMAX 450 is designed to ensure continuously high production output of high-quality final aggregates.
The machine’s hybrid diesel-electric/fully electric system consumes diesel at 15–20 litres/h in normal operation and well below 30 litres/h at peak load. The optional connection to mains power further reduces direct energy costs by up to 60%, depending on the tariff, compared with other diesel-hydraulic mobile plants of similar performance and by round 30% compared with use of the machine’s own onboard diesel engine.
The JAWMAX 450 has also been optimized for transportability, with a transport weight of 39.2 tonnes and transport dimensions 14.71m (length) x 2.88m (width) x 3.60m (height). After unloading from a low-bed truck or uncoupling the optional three-axle dolly, the hopper walls, overband magnet and high and wide-reaching discharge conveyors are positioned hydraulically without tools, making the plant fully operational in just over five minutes.
The machine operator is fully supported by the standard multi-functional remote-control and set-up routines of the intelligent SBM Crush Control system, which also monitors and controls the fully automatic crushing operation in line with pre-set parameters. In addition, a web-based app allows remote access to all important operating and production data.