Sandvik unveil new QI353 mobile impactor
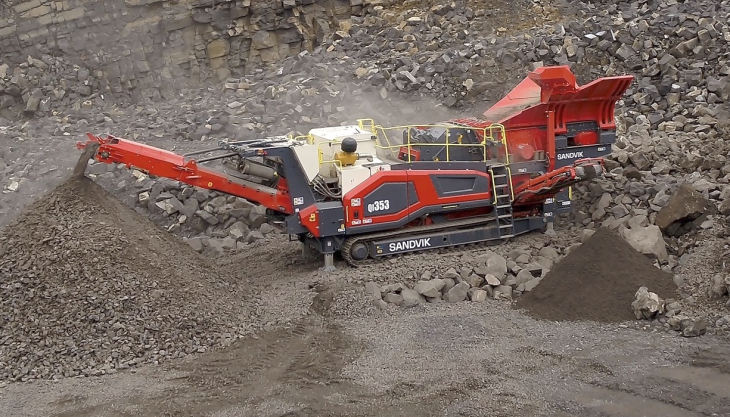
First machine launched in new third-generation 3-Series range of products from Sandvik
SANDVIK Mobile Crushers and Screens have launched the QI353 mid-size impactor, the first of their new third-generation 3-Series products. Designed in response to customer research, Sandvik say the QI353 has been built to offer more productivity, uptime, efficiency, flexibility, connectivity, and safety.
Features a new mid-size track platform and custom Prisec impact crusher, the QI353 is targeted at the quarrying, recycling, and contracting segments, and is said to be the most versatile, mid-sized mobile impactor available today, designed to provide more uptime than any other.
With the operator in mind, the QI353 offers a user-friendly mobile solution, with controls and maintenance points located conveniently at ground level. A key highlight is the new automated control system featuring the Optik intuitive user experience with colour visual display, easy navigation, and total integration for troubleshooting, diagnostics, and support.
The QI353 has been designed with productivity in mind and can process up to 400 tonnes/h. Its feed arrangement includes a new feed hopper with curved heavy-duty sides for greater capacity and tapered feed arrangement to reduce blockages and ensure continuous crushing. It also features a new pan feeder with geared drive and a larger pre-screen with improved access for media replacement.
At the core of the QI353 is a new mid-size Prisec impact crusher, which boasts the largest feed opening (1,170mm x 730mm) and largest rotor diameter (1,150mm) in its class, for higher capacity and greater energy efficiency in primary or secondary applications. Adjustable apron curtains and tip speed ensure a wide range of product gradations can be achieved, whilst all plant conveyors have larger discharge heights for increased stockpiling capacity.
The QI353 features a free-flowing feed arrangement where all components in the flow path through the machine get wider, for improved material flow and fewer blockages. A load-sensing system for the feeder drive ensures continuous crushing, whilst a large double-deck vibrating pre-screen for the effective removal of fines helps maximize throughput and reduce wear. In addition, the QI353 benefits from extended service intervals and larger onboard fuel storage to extend intervals between refuelling.
The machine requires 40% less hydraulic oil per service and benefits from extended hydraulic oil replacement intervals. The QI353 is also fitted with the latest emissions-compliant powerpack for maximum performance and cost efficiency.
The QI353’s natural fines conveyor can be positioned for right- or left-hand discharge with a three-position by-pass chute under the pre-screen allowing a choice of where to send the fines. The machine also comes prepared to accept Sandvik’s new and enhanced HS323 hanging screen module, offering the crusher the flexibility to operate in open or closed circuit.
The HS323 enhancements include ready to accept belt scales for tonnes/h monitoring on fines and stockpile conveyor belts, subframe enhancement for improved screen media access and tensioning, and an updated mid-size stockpile conveyor. The screen’s unique design allows is to be set up in less than 30 minutes and fitted without the use of additional lifting equipment.
The patent pending hanging screen option delivers multi-functionality, turning the machine into a one-, two- or three-way split screener, as well as a highly productive and efficient impact crusher.
The new automation system with Optik intuitive user experience, includes simplified operation controls and total integration with Sandvik’s My Fleet telematics solution. Diagnostic support, pre-installed guides for troubleshooting, and real-time information allows customers to know exactly how their equipment is being utilized.
One of the new additions to the QI353 is the availability of optional belt scales. These are fitted to the product conveyor and will enable productivity data to be displayed on the user interface and via My Fleet for tonnes/h monitoring, ensuring full control of the machine’s output.
For operator safety, Sandvik have incorporated a new access platform under the feeder and pre-screen and a spacious three-sided 270° platform for service and maintenance. A lifting beam, jib, and tackle are also provided, as well as the patented rotor-turning device, to ensure operator safety when removing, rotating, or installing hammers.
A height-adjustable overband magnet and all conveyors can be conveniently lowered for inspection and servicing purposes. Other enhanced safety features are embedded within Optik intuitive user experience, including visual warnings and emergency stop locations.