Ruttle Group invest in CDE technology
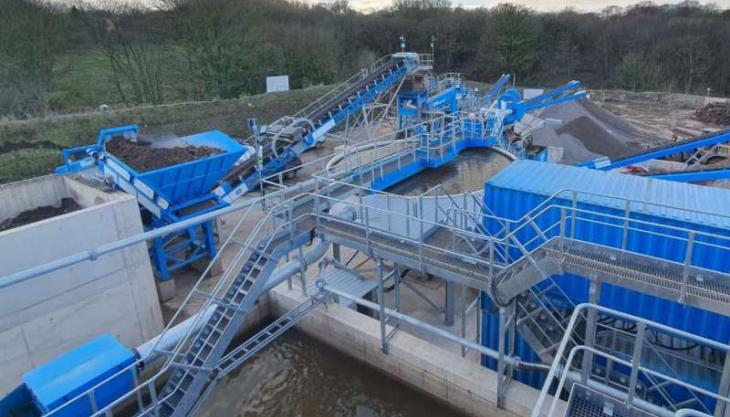
New turnkey recycling wash plant improves output and enhances sustainability in the North West
THE Ruttle Group of companies, one of the North West’s leading suppliers of recycled aggregates, have invested in a new CDE recycling plant for their waste transfer station site in Chorley. The new wash plant will produce 170,000 tonnes of recycled aggregates each year for the construction industry in the north-west of England and across the UK.
Founded in 1958, The Ruttle Group began by renting agricultural equipment to the farming community before extending their operations to earthmoving, excavating, civil engineering and landscape work. Theis latest investment signifies a further expansion by the company and the growth of its recycling and aggregates division.
Traditionally, Ruttle had segregated and stockpiled incoming inert material from construction sites in and around the Chorley area, or crushed and screened it for low-grade use. Ensuring consistency in output materials was a challenge, and with incoming volumes of remediated soils increasing, the company saw the opportunity to supply the market with a higher quality of washed and recycled sands, gravels and soils.
The original methods, while adequate, were limiting the reuse potential of both the outputs and the company as a whole. In their drive to enhance the company’s product offering, Ruttle partnered with wet-processing experts CDE to develop a waste-recycling solution.
In collaboration with Ruttle, CDE co-created and delivered a bespoke wet-processing solution to meet the company’s on-site requirements and commercial needs. The turnkey solution will effectively process the incoming inert material to produce high-quality recycled aggregates.
The 80 tonnes/h wash plant includes an R4500 primary scalping screen, an AggMax modular log-washer, an EvoWash unit, an AquaCycle thickener and a filter press.
CDE’s patented R4500 was created to handle the most troublesome materials, including heavily clay-bound rock and gravel, offering high-energy screening of material before it enters the AggMax log-washer for scrubbing and classification.
Fines are passed to the EvoWash unit, a high-frequency dewatering screen with hydrocyclone technology that provides precise control of silt cut points and eliminates the loss of quality fines to produce a range of high-quality sands.
The new Ruttle plant also incorporates efficient water recycling with the A400 AquaCycle thickener, which ensures that up to 90% of the process water can be recirculated back into the system, offering Ruttle a fully integrated primary water-treatment solution.
The AquaCycle uses a flocculant to separate clean water from the solid particles. The remaining solid particles form a sludge which is dried further in the filter press, the final stage of the process.
The filter press recovers any remaining water for recirculation and creates a dry filter cake suitable for use as pipe bedding and landfill capping, thereby ensuring minimal waste volume from the CDE turnkey solution.
Ruttle are now able to produce two sand products from 0–4mm, three aggregates from 4–20mm and an oversized product, and are meeting both their commercial and environmental aims – creating high-value recycled products which has in turn opened new revenue possibilities.
Ruttle Group managing director Gareth Ruttle said: ‘With the new CDE plant, we are able to increase supply to our current market and customers while exploring new opportunities for the recycled material. We are pleased to be able to divert high volumes of material from landfill while seeing huge benefits to our on-site operations.’
David Kinloch, CDE’s director of business development for the UK & Ireland, commented: ‘We’re delighted to work with Ruttle on this new project. The turnkey solution will increase the volumes of material the company can process and maximize recovery of quality recycled sand and aggregates as a sustainable alternative to diminishing virgin materials.’