Recycling plants expand with Blue Machinery
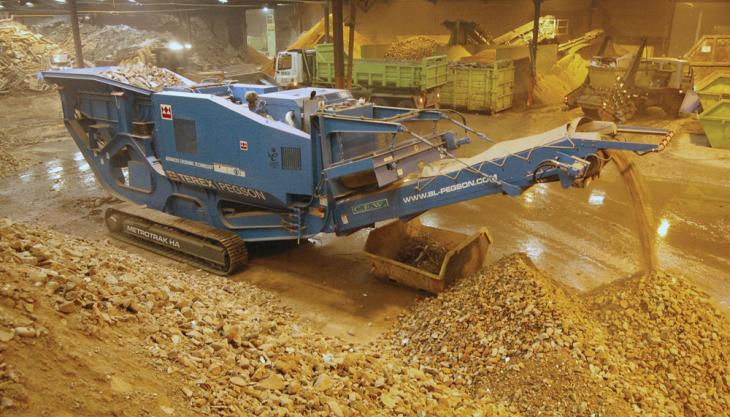
CEW Recycling Group operate what is believed to be the largest under-cover recycling centre in the North-West of England and have a throughput of over 75,000 tonnes a year. Based in St. Helens, Merseyside, the three-acre state-of-the-art facility – all under one roof – collects and receives construction and demolition waste, packaging, domestic and industrial/commercial waste from the region, with numerous contracts from major construction and civil engineering groups, local authorities and commercial concerns.
Having made considerable investments in modern, efficient recycling and reclamation equipment during the past year or so, as part of a planned and continued expansion of their facilities and equipment to recycle increasing volumes, CEW have recently purchased a new TEREX Pegson Metrotrak HA crushing plant from distributors Blue Machinery Central.
CEW reclaim in excess of 90% of the incoming raw waste materials, producing a significant output of quality recycled products and, of equal importance, significantly reducing costly waste-to-landfill volumes. The reclaimed end products include shredded wood waste, baled packaging board for pulping, recycled aggregates, ferrous and non-ferrous metals, plastics and fines – the latter being used predominantly for landfill cover. CEW are also producing 6F2, pipe bedding and, increasingly, high-quality grit sand for flagging and paviours. The company are also working with developers looking to recycle and reuse ‘same site’ demolition debris, in order to make the best possible use of recycled aggregates on brownfield developments.
CEW Recycling Group Ltd have been in existence for over seven years and moved to their current premises in November 2004. In addition to customizing the building to suit their specific requirements, the company also paid particular attention to environmental issues by installing stringent emission controls and dust suppression.
To meet their screening and shredding equipment needs for the recycling centre, the company chiefly turned to Blue Machinery as their main provider. Over the past couple of years CEW have purchased two Powerscreen Chieftain 1400 ‘flat-bed’ screening plants, a Powerscreen Trommel 615 drum screener and a Doppstadt AK-230 high-speed shredder from Blue Machinery. A new static giant trommel has also been added to the facilities, with density separators and a four-bay picking station forming the final part of the separation process.
The latest investment in the new Metrotrak HA crushing plant follows on from Blue Machinery’s recent appointment as a TEREX Pegson distributor, continuing the close working relationship between the two organizations that goes back to CEW’s inception. The machine is the site’s primary crusher, producing crushed aggregates from oversized material for further processing by the trommels and flat-bed screeners.
The Cat-powered Metrotrak HA mobile crushing plant features a hydraulically adjustable ‘M’ Series 900mm x 600mm single-toggle jaw crusher capable of outputs of up to 175 tonnes/h, depending on setting and material feed. CEW’s machine also features an overband magnet for the extraction of ferrous metals, which are reclaimed and recycled. Dust suppression sprays are fitted as standard.
Blue Machinery Central have also recently delivered one of the new-generation XR400 mobile crushers to another of their long-standing customers, P. Casey (Plant Hire) Ltd of Rochdale, Lancashire, who are part of a multi-disciplined organization with interests as diverse as building and refurbishment, land reclamation, civil engineering, waste management and plant hire.
The new crusher joins a large array of equipment available for short- or long-term hire, including excavators, bulldozers, loading shovels, ADTs, compaction equipment, crushers and screeners – all of which can be hired as operated or non-operated machines, in addition to general plant hire activities for the construction, quarrying, demolition and recycling industries.
The X400 primary crusher series was launched by TEREX Pegson in early spring 2006 and has already become established as a highly productive, economical and versatile range of mobile crushing plants, equally at home in quarrying or recycling applications. The model purchased by Casey is the XR400, which features hydraulic release and hydraulic overload protection.
The XR400 has an aggressive crushing action with hydraulic crusher setting adjustment. The high-swing jaw eases material entry into the crushing chamber, while the hydraulic adjustment allows crusher setting changes to be made quickly and easily over a wide range. The adjustment is activated without the need to release the draw-back mechanism, which is particularly useful for applications where regular jaw setting adjustments are required.
Casey’s XR400, with hydraulic release, has been specifically designed to alleviate the problems associated with crusher overload should any tramp metal enter the crushing process. The hydraulic release feature is fully adjustable, quick and easy to reset and makes blockage clearance a simple process. This saves time and money by allowing the crusher to continue processing with minimal disruption while, at the same time, protecting the jaw mechanism from potential damage.
There are numerous features on the X400 series designed to improve productivity and enhance maintenance procedures. For example, the feed hopper is constructed from 15mm heavy-duty Hardox, for prolonged active life, and folds out hydraulically with boltless fixing; there is a new and improved crusher drive access system; an easy-access power pack canopy; hydraulic and oil filter changes are only required at 2,000h intervals; and there is also generous under-crusher accessibility, for the safe and easy removal of wire, together with a hydraulic tilting conveyor system.
Driven by a 172kW Cat C9 engine, the XR400 is PLC controlled for optimum performance with fingertip actuation and a simple automatic start sequence. The plant’s HFO direct-drive system is said to deliver extremely low fuel consumption figures – as little as 22 litres/h, depending on the application. According to TEREX Pegson, this can result in annual running-cost savings of over £21,000 compared with similar-sized competitors’ products.
In operation, a new style of vibrating grizzly feeder, with an extended twin-cartridge grizzly section, actively discourages pegging and blinding. In addition, an improved impact area under the product conveyor, at the crusher discharge point, has been introduced and the hydraulically elevating and lowering product conveyor itself has an increased discharged height of 3.9m for greater stockpiling capability.
Blue Machinery (Central) Ltd, Appleton Thorn Trading Estate, Appleton Thorn, Warrington, Cheshire WA4 4SN; tel: (0845) 230 4460; fax: (0845) 658 2314; email: sales@bluemachinery.com