QMS replace primary crusher at Hope cement works
Vintage Fuller Traylor primary gyratory crusher replaced with new unit from FLSmidth
BREEDON Group’s Hope cement works, located near the village of Hope in Derbyshire, is recognized as the UK’s largest cement plant and is integral to Breedon’s cement manufacturing capabilities. To sustain the processing of quarried limestone required for cement manufacturing, Breedon recently executed a major project to replace Hope’s 1940s Fuller Traylor primary gyratory crusher with a new 1,250 tonnes/h primary gyratory crusher, supplied by FLSmidth. Quarry Manufacturing and Supplies Ltd (QMS) were the lead partner in the installation, with the overall project being managed by the projects team at Hope, alongside a team of trusted contract partners.
Breedon installed the new gyratory primary crusher in September 2024. The site had operated and maintained the previous Fuller Traylor crusher since its installation in 1952, with the body of the machine being completely original since its installation. However, owing to advancements in primary crusher technology, and a desire by the business to improve the maintainability of the crusher, plans for the replacement of the original crusher were put in place in 2022.
The project involved the installation of a single, new primary crusher and associated equipment on the existing limestone crushing line, which further consists of twin-line secondary and tertiary crushing stages, comprising of state-of-the-art QMS B6 cone crushers. The task of pre-assembling the new FLSmidth crusher, demolishing and removing the old Traylor crusher, and finally installing the new FLSmidth crusher, was given to QMS, who worked in close partnership with the Breedon team at Hope, their contract partners, and equipment suppliers FLSmidth.
George Close, UK sales director at QMS, explained: ‘Working closely with FLSmidth, we had to first build up the new gyratory crusher. This was a time-consuming and exacting process, as we were working to tight deadlines and the crusher had to be assembled on site. This site assembly was the first time all the crusher parts had been together, as the components were delivered by FLSmidth from all over the world. This took approximately five weeks. The second stage was to remove the old primary Traylor gyratory crusher; this utilized QMS’ expertise and experience gained on working with gyratory crushers throughout the world. This took two weeks, working 24h a day, seven days a week, and was finally completed in mid-August (2024).
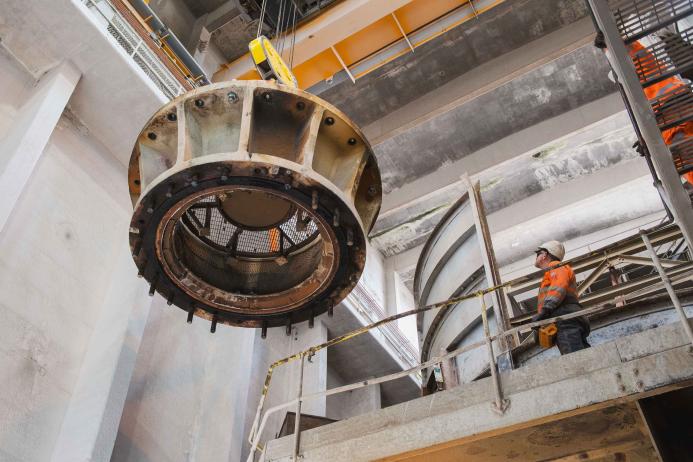
‘The third and final stage of the project was the installation of the new crusher; this again further necessitated working round the clock, night and day, taking over five weeks to complete. In addition, the new crusher has a QMS-manufactured, bespoke stainless steel lubrication system which is now integral to the crusher’s operation. We further assisted through commissioning of the crusher, alongside the Breedon and FLSmidth teams, thereby ensuring that it was fully operational.’
With a project of this scope and importance, QMS were not the only contractor involved, as Mr Close explained: ‘Our task not only involved work at our end, but also working with the project team at Hope, including FortunumPM, who acted as client representative, as well as the other contractors whose work was essential to the success of the project. Other contractors on the installation included PCS UK Ltd, who handled all the electrical work, Tideswell Welding Services, who handled all the ancillary fabrication and welding (not involving the crusher itself), and Access Drilling Services Ltd, who handled all the significant concrete removal work.’
Commenting on the work undertaken by QMS and the other contractors, David Boole, project engineer at Hope and Breedon’s representative for the installation, said: ‘We have been working with Jonathan and the team from QMS for many years now. They maintain the site’s Sandvik cone crushers (as well as the new QMS B6 cone crushers) and help to ensure Hope Works operates at optimized efficiency. The work undertaken on the installation of the FLSmidth gyratory crusher is a credit to QMS and the other contractors.’