Pike Industries benefit from PCD milling tools
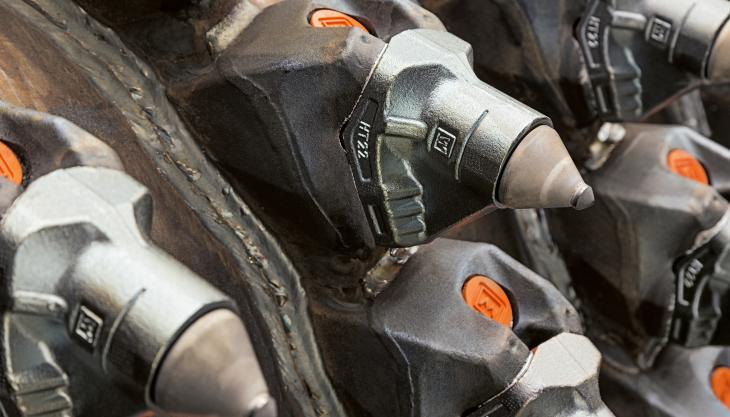
US road builder boosts productivity with polycrystalline diamond-tipped milling tools from Wirtgen
HIGH-performance Wirtgen milling tools with a polycrystalline diamond (PCD) tip have significantly increased the productivity of a major US road builder from New England.
Pike Industries, who currently produce more than 3 million tons of asphalt and process in excess of 6 million tons of aggregates per annum, switched from picks with carbide tips to PCD milling tools in 2017, which resulted in extremely evenly milled surfaces and considerable time saved during milling operations.
Due to their tool geometry and materials, PCD milling tools are primarily suitable for surface layer rehabilitation and are predominantly used in fine-milling applications. When fine milling road surfaces, milling drums with a tool spacing of 6mm or 8mm (LA6 or LA8) are used. In comparison, a standard milling drum for conventional milling has a tool spacing of 15mm (LA15).
Fine-milling drums with LA6 produce an even finer milling pattern than with LA8, and Maine’s Department of Transportation accepts both tool spacings.
‘We can therefore alternate between the milling drums,’ explained Tom Quinn, head of cold milling and pavement removal at Pike Industries. ‘The smaller tool spacing also affects the advance rate of the machine, which means that we work with a lower speed at larger milling depths.’
Fine milling removes ruts or unevenness in the road surface, improves the grip of roads that have been cleared for traffic before the surface layer is paved, and ensures a better bond between the layers when paving thin layers hot.
At Pike Industries, the fine-milling process plays a major role. This is because it allows them to produce a particularly even sub-base for the ultra-thin bonded surface layers that they pave on behalf of the state of Maine.
The requirements of the Maine Department of Transportation stipulate fine milling and, in some cases, standard milling as preparation for paving thin layers hot. ‘We are currently working on a project in which we are milling a cross slope with fine-milling drums and even removing the pavement at a depth of 15cm,’ said Mr Quinn.
‘One reason for requiring the small tool spacings is the durability of the milling pattern when the road is driven on without a surface layer for a longer period of time. The pavement is expected to better withstand the effects of traffic as a result.’
As part of another rehabilitation project, Pike Industries recently completed fine milling on State Route 202 in Gorham, approximately 20km west of Portland, Maine. Here, the company used a Wirtgen W 220 cold-milling machine equipped with a 2.5m wide fine-milling drum and PCD milling tools with LA8.
According to Mark Williams, the site manager responsible for the project, the surface layer was removed 2cm deep over a length of 3km on two lanes and the adjacent shoulders.
In this context, switching from standard picks to PCD milling tools significantly increased Pike Industries’ productivity. Previously, the team had to completely replace the set of picks at the end of each working day – now the new milling tools can be used for an entire season or even longer.
‘Picks with carbide tips wear out over the course of the day, which means that the milling pattern is not absolutely uniform and individual picks have to be replaced more frequently. In contrast, PCD milling tools have a diamond tip and an optimized cutting geometry, thus guaranteeing consistent results,’ explained Mr Quinn.
‘Even if a PCD tool has to be changed every now and then, it doesn’t have a negative effect on the pattern because the PCD tools used exhibit hardly any length wear. A uniform milling pattern is extremely important to us, and a single set of PCD milling tools is enough to guarantee this each and every day for a long period of time.’
The type of application is the main factor that determines which pick (carbide or PCD) is the most cost-effective for the job. Independent of this, cold-milling machine specialists Wirtgen have created a useful addition to their existing range of picks with PCD milling tools, thereby tailoring their range of solutions in cutting technology to meet specific requirements.
Pike Industries say they are certain that the work they save during day-to-day milling operations more than offsets the higher cost of PCD milling tools, as one set of tools can be used for an entire milling season, eliminating the need to replace picks.
Last year the company milled a total area of approximately 1.7 million square meters with two milling drums. The PCD tools on the drum with LA6 tool spacing had already removed over 400,000 square meters during the previous season, while the drum with LA8 tool spacing used on State Route 202 in Maine was fitted with new PCD tools at the beginning of the 2019 season.
‘They’re simply the best,’ said Mr Quinn. ‘This is because despite the higher acquisition costs, the PCD milling tools have already paid for themselves after half the season.
‘The PCD milling tool is a complete unit,’ he explained, ‘so not only do you eliminate the cost of the carbide picks, but also the cost of the pick holders on the milling drum. We were able to significantly cut costs through the use of PCD milling tools and the associated reduction in the amount of work involved.’