New mobile crushers from Powerscreen
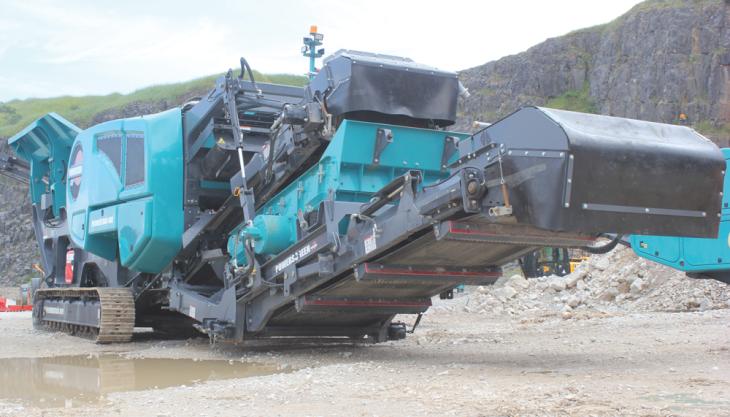
Jaw crusher
Powerscreen used this year’s Hillhead show to launch their new-generation Premiertrak 400 jaw crusher, which has been redesigned to run at low engine rev/min for improved fuel efficiency, reduced noise emissions and a lower cost per tonne, making it well suited to use on urban sites. The machine features the new styling pioneered on the Premiertrak 600, with GRP panels designed for ease of access and delivering a modern look, whilst maintaining the robustness associated with Powerscreen products.
Likewise, the new chamber in this machine was based on the success of the Premiertrak 300 hydraulic release module. Taking a lead from its smaller stablemate, the hydraulic release chamber option on the new-generation Premiertrak 400 features single-button control for closed-side setting adjustment as well as the ability to lock out the hydraulic release functionality, allowing the machine to operate in a hard rock quarry operation with the same efficiency as the standard hydraulic-adjust chamber.
Powerscreen’s proven hydraulic release system detects uncrushable material and lets it pass through the chamber safely, making the machine particularly suitable for the processing of construction and demolition waste. The new optional reverse system allows for safe and quick clearing of blockages, whilst maintaining the efficiency of the direct-drive system.
The machine on display at Hillhead was fitted with an optional post-screen system, which is designed to ensure maximum uptime and easy service and maintenance. For European customers, the new-generation Premiertrak 400 will be available with a constant-speed engine option to eliminate any requirement for expensive and complex exhaust after-treatment systems.
New impact crusher
The latest addition to the company’s mobile impact crusher range was also launched at Hillhead 2016. Powerscreen say the new Trakpactor 550 horizontal-shaft impact crusher is set to dominate in the mid-to-large size class, providing customers with the highest levels of reliability, efficiency and performance. And like the Premiertrak 400, the sleek and modern aesthetics of the Trackpactor 550 are said to belie the machine’s robust and heavily engineered chassis and sub-structures.
From the feeder through to the product conveyor, the Trakpactor 550 has been designed to promote an easy and effective flow of material, to minimize any potential material build-up and thereby ensure maximum uptime. An optional 2.1m long pre-screen unit with large open area allows the maximum amount of fines to be removed, thereby maximizing production, minimizing wear costs and contributing to extremely low cost-per-tonne performance.
The brand new chamber design, which has been rigorously developed and tested for performance and durability, incorporates features such as a hydraulic inlet lid and automatic adjustment system for ease of use by the operator, whilst an auto-rotation system for blow bar changes demonstrates Powerscreen’s focus on machine safety.
Moreover, like all Powerscreen crushers, the Trakpactor 550 comes complete with the company’s Pulse remote monitoring system as standard. This remote fleet-management system provides crushing and screening equipment owners and operators with access to key data, the analysis of which can help improve machine operation, increase uptime and allow in-depth reporting and fleet management.
Available anywhere at any time via PC, tablet or smartphone, Powerscreen Pulse provides comprehensive information on the GPS location, start and stop times, fuel consumption, tonnages, cone settings, wear ratings, operating hours, maintenance status, plus much more.