New dust-suppression hopper system for dry flowing materials
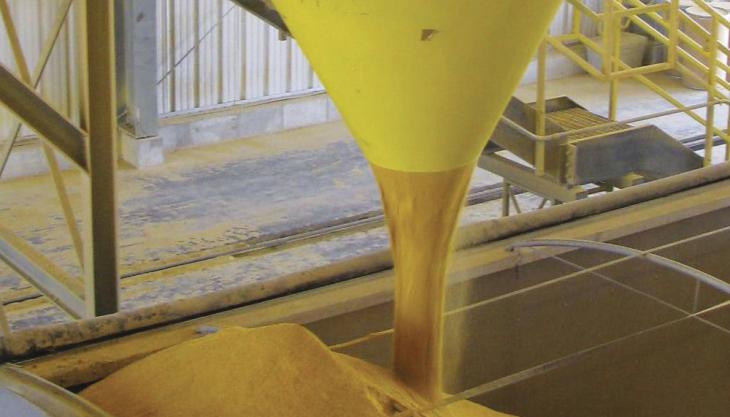
Bulk materials handling specialists Guttridge Ltd have launched a new, award-winning dust-suppression hopper system into the UK bulk handling market. Following years of fine-tuning and development work, companies around the world have acclaimed the new hopper as a total success in applications involving dry, free-flowing granular materials.
Now available for the first time in the UK, the new hopper ingeniously contains any dust within the actual product stream when discharging dry bulk materials, thus avoiding the need for the more complicated retractable loading spouts or telescopic loading bellows. The hopper is simply installed under a feed point where it can be suspended above the target, facilitating the discharge of dry goods as a concentrated solid column into road vehicles, rail wagons, stockpiles, storage containers or bags.
Originally designed for fertilizers, Guttridge say the hopper has proven successful with many other dry materials, including sand and salt. In some applications, load out rates in excess of 800 tonnes/h can be achieved, while multiple hoppers can be used for even greater throughputs.
Uncomplicated to install and easy to operate and maintain, there is no product separation during the fall of material, which means that fine material does not become concentrated in the centre of the stockpile. The standard version has no internal moving parts and requires no power supply, while the more advanced positional feed model includes built-in computerized control to manage the discharge rate for products with different specific gravities. Models are available in polyethylene, steel, stainless steel or ceramic lined.
Grant Allen, technical manager of Impact Fertilisers in New Zealand, commented: ‘Each year we load 120,000 tonnes of super phosphate for bulk shipment, which was generating localized dust, resulting in environmental complaints from the wider community and ongoing health and safety issues.
‘Installation of the new dust-suppression hopper this has resulted in a significant improvement in the working environment and reduced environmental complaints to zero. All this has been achieved with no impact on the speed of the loading operation and has, in some cases, resulted in an increased rate.’
Currently being trialed at various sites within the UK, the new dust-suppression hopper reduces hazards, health risks, dust, wastage, cleaning and maintenance costs, and increases storage capacity.