New drives for Nostell brickworks
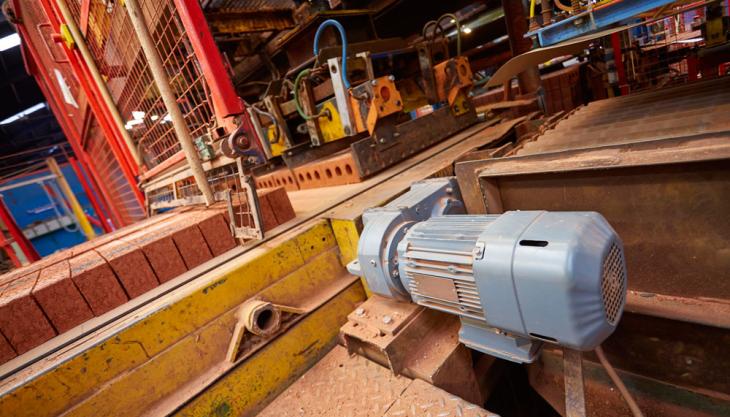
Ibstock Brick gear up production in drive technology partnership with SEW Eurodrive
AS part of a planned upgrade of their brick-making facility at Nostell, near Wakefield, Yorkshire, Ibstock Brick are replacing all the drive technology at the plant with solutions provided by SEW Eurodrive. The investment and upgrade is in response to increased demand for the company’s products within the UK market and is designed to increase production, improve efficiency and cut downtime.
David Rotherforth, Ibstock Brick’s engineering manager at the Nostell site, explained: ‘This upgrade isn’t just about updating drives with the latest technology. This is about future-proofing the whole plant and forming a strategic partnership with a drive technology supplier who can work closely with us to enable us to achieve all our objectives in terms of cutting downtime, reducing stock, increasing production and optimizing efficiency.’
As part of the upgrade, SEW Eurodrive’s engineers conducted a survey of all the drives at the plant and entered details of each unit on the company’s unique drive technology maintenance system, CDM. This records comprehensive information – including drive condition, service history and scheduled maintenance – on a secure online database that can be accessed quickly and easily by Ibstock’s engineers via multiple platforms, such as laptops, tablets and smartphones.
CDM will increase the efficiency of Ibstock’s drive technology maintenance regime by cutting downtime, eliminating unnecessary stock, identifying potential problems in advance and allowing engineers to quickly check the condition of each drive. According to SEW, CDM will provide the best possible protection against costly failures and unscheduled downtime, as well as simplifying and streamlining maintenance as a whole.
The ability to respond quickly and provide a high level of support was a key issue for Ibstock’s engineers in choosing SEW as a drive technology partner for the upgrade at Nostell. With the capacity to manufacture around 13,000 bricks an hour, increasing efficiency and cutting downtime by replacing older, unreliable drive technology was essential to achieve the objectives of the upgrade and meet the growing demand for the plant’s products.
Previously, in a worst-case scenario, unscheduled downtime as the result of a failed gearbox could have resulted in six to eight weeks of lost production. A key objective of the upgrade, therefore, was to eliminate such occurrences, as far as possible. To do so, whilst avoiding holding huge stocks of spare gearboxes, motors and other components, Ibstock’s engineers needed a drive partnership that could provide virtual integration with their own maintenance operations.
SEW’s ability to provide this level of support and respond rapidly was put to the test during the initial phase of the plant’s upgrade when an old motor on a slug-pusher drive failed unexpectedly, bringing the whole brick production line to a halt. However, within 45 minutes of Ibstock’s engineers reporting the failure to SEW, a new motor was ready to be installed and downtime was kept to an absolute minimum.
As David Rotherforth explained: ‘It was almost as if the replacement motor had come straight from our own stores. Reporting the failure to SEW was like reporting to our own people. We were all on the same team and we literally couldn’t have had the drive up and running again any faster.’
So far, SEW have upgraded approximately 24 drive units on Ibstock’s setting plant at Nostell, and, during the process, have completely redesigned and simplified the drive system on the plant’s hoist. This involved the replacement of an inefficient and unnecessarily complex arrangement of two worm gearboxes connected by a layshaft and driven by a single motor and pulley system.
The new, more efficient design involved standard gearing, inverters and a bespoke bedplate that avoided any alteration to existing steelwork. Installation and commissioning was undertaken by SEW’s engineers, and the new high-efficiency system has immediately cut the hoist’s energy consumption by 25%.
According to Mr Rotherforth, engineers at the Nostell plant have been so impressed with what has been achieved so far that the company is now pushing ahead with plans to standardize all drive technology throughout the site with further solutions from SEW Eurodrive.