Mick George boost output with new washing plant
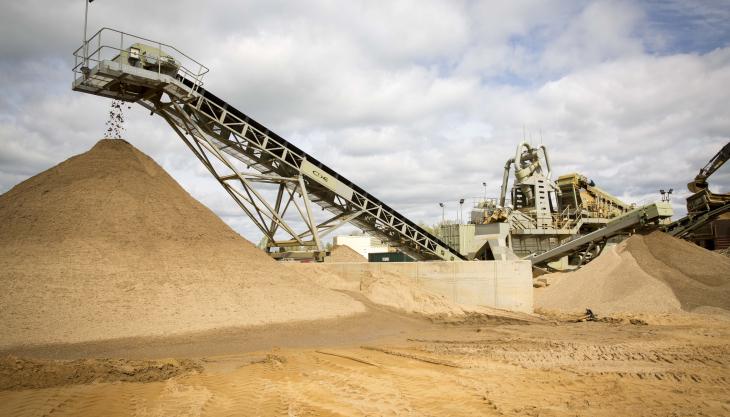
Company powers up sand and gravel volumes with new washing plant supplied by APS
MICK George Ltd have boosted sand and gravel production to a rate of 300 tonnes/h at their Bridge Farm site, in Cambridgeshire, following the introduction of a new high-performance washing plant.
Specified and supplied by Mick George’s long-standing partners Aggregate Processing Solutions (APS), the bespoke system is being used to supply materials for the major A14 Cambridge to Huntingdon road upgrade.
APS – part of the Finlay Group of companies – have worked closely with Mick George for more than 30 years and the relationship, which has seen approximately £20 million of equipment specified, has supported the continued growth of the business.
The company, which operates across East Anglia and the East Midlands, started out in business with a single tipper truck in 1978 and now boasts a commercial fleet in excess of 350 HGV vehicles.
Mick George specialize in bulk excavation, earthmoving, demolition and asbestos removal, as well as waste-management services and aggregate and concrete supply. They have also recently expanded into facilities management.
Darren Griffiths, area quarry manager at Mick George, who has nearly 30 years’ experience in the industry, says the APS machine is a fundamental part of the site.
‘It’s producing all the material we need in one self-contained unit,’ he commented. ‘The material we’re processing is taken off site, straight from the plant, so it’s been really important for us to have equipment that can keep up with such demand.
‘The best thing is that when you turn it on it does exactly what it’s supposed to, with less wear and easy maintenance.’
APS have incorporated a number of standard modular relocatable units to create the washing plant, providing Mick George with a site-specific solution to meet their precise needs.
It consists of a CDE S20 feed hopper, a CDE M4500 modular mobile washing plant, an AggMax 153 modular scrubbing and classification plant, and a 20m radial conveyor, which helps increase stockpile capacity and saves time for the business.
The washing plant, which requires only one operator, is producing six different products – a +40mm reject, 40mm, 20mm, 10mm and 6mm aggregate, as well as concrete sand.
Mr Griffiths added: ‘As it runs so well, all of the maintenance is scheduled, which is a major benefit for us. The backup we have received has also been fantastic.’
John Dunne, managing director of APS – who worked alongside Mr Griffiths to specify the plant – said: ‘It’s our association with CDE as a UK licensed partner that allows us to create bespoke solutions for businesses.
‘Working closely with Mick George, we have provided a washing plant with powerhouse production levels and a backup that can be trusted.’
To see the new washing plant in action, visit: https://www.youtube.com/watch?v=-CHMOlR0IY8&t=8s