Metso MP2500 cone crusher for First Quantum Minerals
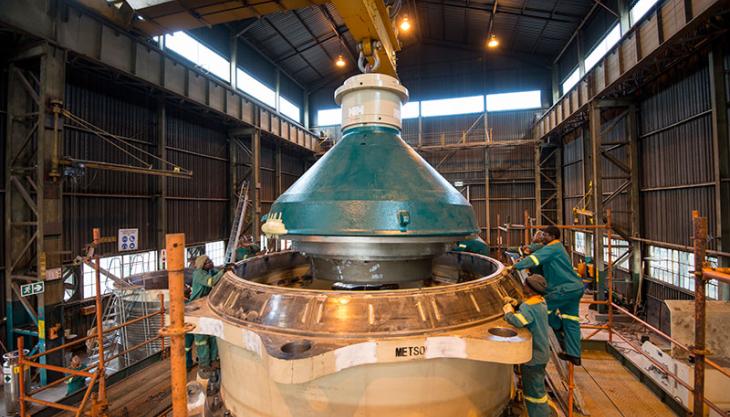
Metso introduce world’s largest cone crusher in response to mining industry’s efficiency challenge
WITH ore grades declining and increasing amounts having to be processed to obtain the requisite amount of mineral needed to meet production targets, the global mining industry is currently striving to develop more energy- and cost-efficient technologies for minerals processing.
Playing their part, Metso are responding to these challenges by developing larger and more energy-efficient machines for minerals processing, such as the world’s largest cone crusher – the MP2500.
The first MP2500 crushers have been purchased by First Quantum Minerals Ltd (FQML) for use at their Sentinel Mine, in Zambia. Their order, worth more than €10 million, was received by Metso in the first quarter of 2013 and the crushers will be fully operational at the site in early 2015.
The MP2500 was selected for Sentinel because of its capacity to process large volumes of rock, thereby achieving cost savings by reducing the number of additional crushers, related infrastructure and maintenance work required. For example, to replicate the performance of two MP2500 units would require four smaller MP1250 crushers plus all the associated infrastructure.
Moreover, with the largest feed opening ever made, the MP2500 can handle bigger lumps of rock, while its ability to crush and reduce rock further than traditional crushers helps reduce energy consumption in the later parts of the process.
Designed for use in secondary and tertiary crushing applications, the MP2500 is designed to link easily with other Metso products to create a simplified, cost-effective process flow for high-production sites.
According to Metso, development of the MP2500 cone crusher has resulted in a number of innovations in the area of health and safety, many based on discussions with FQML, while serviceability and ease of maintenance were among other key areas of focus during the design process.
Metso will help ensure efficient operation of the new MP2500 units by stationing full-time field service engineers at the Sentinel mine for a period of 12 months following commissioning, and by stocking critical spare parts at their South African distribution centre as well on site.