Martin Engineering introduce ‘digital’ data-tracking programme
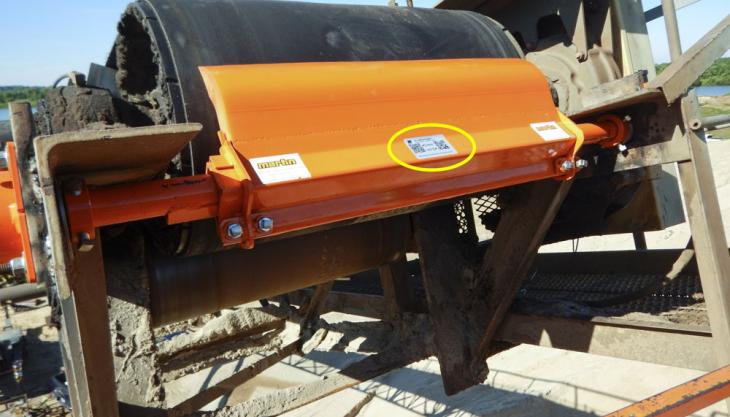
Tracking system uses QR codes to help improve safety and reduce unscheduled downtime
WITH bulk handling equipment specialists continuing to make use of new and evolving technologies to develop ‘smarter’ conveyor systems, Martin Engineering have introduced a new data-tracking system with QR codes on their belt cleaners and other components.
Currently being implemented in select markets around the world, the new tracking programme captures a wide array of information to create a detailed record of all components. Date codes are imprinted on the blades during manufacture, which is important for urethane because it has a limited shelf life, while technicians also affix tags on existing equipment to begin monitoring condition and recording observations.
Customers will benefit from regularly scheduled inspections by factory-trained and MSHA-certified technicians, providing operators with easy access to a wealth of data on the application, operating environment, service life and condition of conveyor components, updated on every belt cleaner maintenance visit.
Martin Engineering have also launched a new smartphone App that gives technicians and customers access to key data which, in turn, helps maximize both conveyor belt performance and service life, while minimizing carryback and spillage.
Data tracking and analysis have been in use by manufacturers of sophisticated equipment for several years, but the new data-tracking programme developed by Martin Engineering is believed to be the first of its kind for conveyor components. The company already has plans to expand an asset-tagging programme to its air cannons and other equipment over time.
According to Chris Schmelzer, director of the wear components business group for Martin Engineering, the constant monitoring of components contributes to enhanced safety, efficiency and reliability of the conveyor systems – minimizing hazards and unplanned outages.
‘Periodic reviews often reveal developing problems before they become a failure, such as worn idlers, leaking seals or excessive spillage,’ he said. ‘The data-tracking programme will help us work with our customers to make better-informed decisions about what equipment to use in specific applications, accurately predicting the expected wear life.
‘The goal is to help ensure that all components are properly serviced and replaced during scheduled outages, before a major breakdown occurs and stops production.’
With the new tagging and capture capabilities, component data can be recorded (eg product date of manufacture, installation and service history) and analyzed in much greater detail than ever before. Every inspection a technician makes will be logged in, along with operational factors such as the material being handled, conveyor speed and remaining wear life.