Higgs Plant purchase three new Bomag rollers
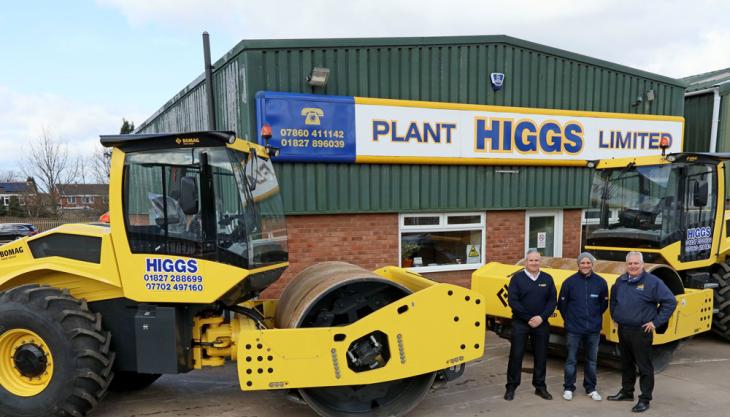
Plant hire firm invests more than £235,000 in latest ‘dash-5’ Stage 4-compliant rollers
TAMWORTH-based Higgs Plant have invested more than £235,000 in three of the latest generation ‘dash-5’, low-emission, Stage 4-compliant Bomag self-propelled single-drum rollers.
The BW 213 DH-5, BW 216 DH-5 and BW 219 DH-5 models bought by Higgs Plant weigh in at 12.7, 16.0 and 19.4 tonnes respectively. The company specified the high-climb DH, twin-pump models and, for added versatility, also ordered pad-foot shell kits for all three machines.
Richard Higgs and plant manager Graham Buckle plan on targeting civil engineering, major infrastructure and brownfield refurbishment jobs for their new fuel-efficient Bomag rollers.
‘The step from Stage 3B to Stage 4 doesn’t sound much,’ commented Mr Buckle, ‘but these new Bomag’s emit between 12% and 20% of the mono-nitrogen oxides (NOx) of an identical sized competitive Stage 3B machine. We believe that on environmentally sensitive jobs, that’s more than enough to make a difference.’
The three machines are powered by 95kW, 115kW and 150kW Deutz TCD 3.6-, 4.1- and 6.1-litre Stage 4-compliant turbocharged diesel engines respectively. Each is equipped with a diesel oxidation catalyst (DOC), a selective catalytic converter (SCR) and a diesel particulate filter (DPF).
To deliver performance with economy, the engine’s electronic control system is managed by Bomag’s ECOMODE system that automatically matches engine power to machine demand, reducing fuel consumption by up to 30%.
The engines are matched to the latest twin-pump hydraulic circuit in the DH models that gives four-speed drive and up to 60% gradeability (57% with vibration).
Moreover, the latest Bomag ‘dash-5’ single drum rollers feature a spacious cab that gives excellent all-round visibility for safety, whilst intuitive controls maximize productivity and minimize fatigue. In addition, all routine service tasks can be completed from ground level, and the new maintenance-free articulated joint further reduces service time and cost.
Richard Higgs said: ‘We’ve run Bomag rollers before but never bought new ones. I think the time is right to invest in the next generation of technology and these new machines are a step up from anything else available. They can tackle the toughest jobs and yet they are fuel efficient and have the lowest possible emissions. And we know that Bomag residual values are the best.’
The three new machines were delivered directly from Bomag GB at the beginning of April before going to work on large civil engineering projects in the West Midlands.
Bomag will be exhibiting a Stage 4 BW 216 DH-5 and other machines from their extensive range of milling, paving and compaction products on stand S1 at Hillhead 2016 from 28–30 June.