Groeneveld and UPS form new strategic alliance
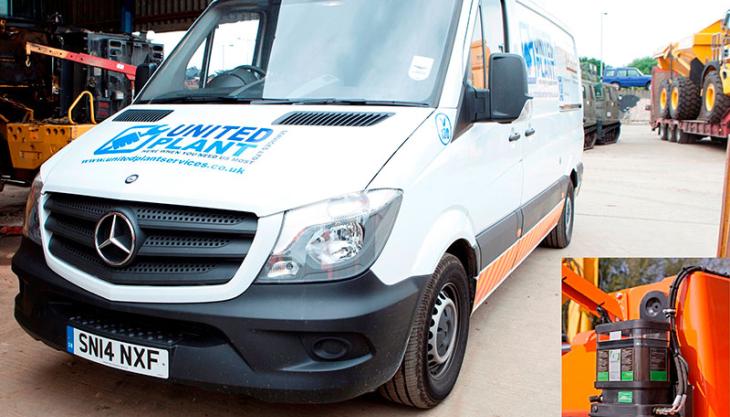
United Plant Services chosen to handle repair and servicing of Groeneveld automatic greasing systems across the UK
UNITED Plant Services (UPS), specialists in plant machinery maintenance, have formed a new strategic alliance with Groeneveld, which will see UPS handle repair and servicing for one of the UK’s leading lubrication solutions manufacturers.
Groeneveld’s automatic greasing systems are commonly used across many leading brands of construction equipment, including Bell Equipment, Caterpillar, JCB and Volvo. If a system error goes unchecked, there is the risk of long-term damage to machine components (eg bearings), thereby making it important that an engineer is called out to quickly resolve the issue.
Given that plant equipment is located throughout the UK, often away from major urban centres, Groeneveld recognized the value of recruiting a specialist maintenance provider to support the company’s own engineers and avoid any gaps in coverage where response could not be achieved within an acceptable time frame.
With their expertise in the construction sector, UPS offer exactly the support services required by Groeneveld. While Groeneveld had prior knowledge of UPS, the seeds of the current strategic partnership were sown at a meeting between the two companies at the 2014 Commercial Vehicle Show.
‘United Plant Services combines specialist knowledge of the plant sector with a UK-wide geographical reach,’ said Gary Hewitt, managing director of Groeneveld UK. ‘As such, we believe they will significantly enhance our ability to react to customer requirements. By outsourcing much of our repair and maintenance demands to UPS, we can allocate our in-house resource to the complex task of installing automatic greasing systems, both for new machines and retrofit to existing models, in order to improve their performance and productivity.’
UPS will provide strategic support for warranty repairs and call-outs on Groeneveld systems. Typically, an engineer will be called out when an error message is displayed on the automatic greasing system. Groeneveld will remain the first point of contact for all call-outs, allowing the company to determine whether UPS or its own team is best located to attend to the machine.
‘Groeneveld customers will get the best of both worlds – a consistent, one-call request for support, allied to the fastest and most efficient response time,’ said Mark Cooper, managing director of UPS.
UPS engineers are now being trained on Groeneveld’s construction greasing systems, including the diagnostic software that provides rapid detail of what needs rectifying and how long the machine has been without lubrication. The contractor will also carry strategic stock for primary service needs at its Burton-upon-Trent and Bonnybridge depots.