Gravity Foundations
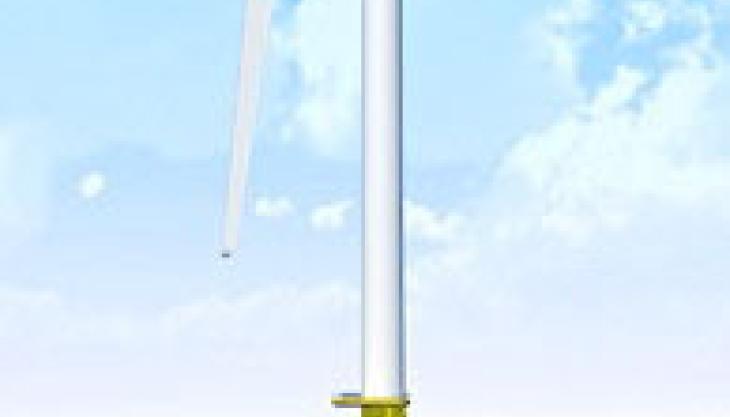
Concrete sector aims to ensure UK leads world in offshore wind power
Eyebrows are often raised on hearing the declaration that the UK is a world leader. With regards to offshore wind power generation, that declaration is true. A recent industry conference, hosted by MPA-The Concrete Centre, heard how the concrete sector has the solutions and capacity to ensure that UK offshore wind generation continues to power ahead.
The UK has built more offshore wind farms than any other country in the world, accounting for nearly all of the turbines erected in European waters during 2011. And there is more to come. The Government is committed to installing 3,000 additional wind turbines over the next nine years taking the current 1.3GW of energy generated by offshore wind power to 18GW.
At the conference, the support of the Government for offshore wind power was underlined by Chris Pook, head of the Green Economy team, Department for Business, Innovation and Skills, who opened the conference. Stating that offshore wind power is integral to the UK’s transition to a greener economy, Mr Pook highlighted the establishment of CORES, centres for offshore renewables engineering, which aim to provide local centres of excellence for development and manufacturing via partnership between central and local government and industry and so pull together both investment focus and offshore expertise.
Initial proposed locations for CORES include Tyneside, Teeside, the Humber, Great Yarmouth and Sheerness. Mr Pook believes that the time is right for investment in offshore wind power and stated that: ‘2012 will be a crucial year for offshore development and the Government is keen to work with industry to develop and deliver offshore solutions’.
As managers of the UK seabed out to a 12 nautical mile limit, The Crown Estate has a major role to play in the development of the offshore wind energy industry. Adrian Fox, supply chain manager for The Crown Estates, outlined what he described as being the world’s largest offshore wind farm programme. He warned, however, that the potential of offshore wind power would only be truly realized with the delivery of greater cost efficiencies for the manufacture, installation and operation of wind turbines.
The Crown Estate is currently undertaking a series of cost studies examining potential cost savings. Emerging themes include greater site optimization, early contractor involvement, increased data sharing and project collaboration, larger rotors and more efficient foundation installation. Ultimately, the challenge is to achieve a cost of £100 per megawatt of power generation.
With regards to foundations for offshore turbines, Mr Fox believes that the third and future rounds of The Crown Estate leasing could favour gravity foundation solutions due to the increased water depth and distance from shore demanding a more robust and maintenance-free solution. Indeed, from a depth of 25m to 30m and more, gravity foundations could be the economic solution of choice.
In addition to long-term robustness and performance, concrete foundations for offshore wind turbines also offer environmental benefits. These include minimum disruption to the seabed and reduced noise impact on sea life during installation. At the end of their operational life they can also be easily decommissioned and recycled. The issues of seabed disruption and the effect of noise on sea life was highlighted by James Bussell of Natural England. He believed that gravity foundations have an advantage in that their installation is less disruptive than mono piles. However, he warned that, as yet, the UK has little experience of these foundations and called for further modelling and trials to monitor their impact.
As a green alternative to carbon fuels, consideration of the environmental impact of wind turbines is essential. Members of The Interest Group for Gravity Foundations – Offshore Wind, run by MPA-The Concrete Centre, have carried out a study to determine the carbon footprint of a typical gravity foundation for offshore wind. Henrietta Ridgeon of Arup presented the interim results of this study, which demonstrated that in part due to the use of reinforcement manufactured from UK-sourced recycled scrap and locally, responsibly sourced cement, concrete gravity foundations provide a lower carbon footprint than alternative steel foundations.
Furthermore, additional carbon savings can be achieved by the use of cement alternatives which also provide extremely durable structures with the resultant reduced ongoing maintenance requirements. Due to the simple installation of gravity foundations, recycling of the concrete and reinforcement at end of life is relatively straightforward.
The construction industry has developed a wide range of concrete foundation solutions for offshore wind turbines. These solutions aim to capitalize upon the cost benefits of simplicity of design, repetition of construction, ease of installation and low maintenance. They include both in-situ and precast solutions with a range of installation approaches and techniques.
The conference heard from a number of companies and joint ventures including Gravitas (a consortia of Arup, Costain and Hochtief), GBF (a consortia of Vinci Construction UK and Freyssinet International), Deppwater Turbine Installation (DTI-50) and Strabag. In addition to these are concrete foundation solutions provided by BAM Nuttall, Wind at Base, Skanska, Grontmij, Hormifuste, Vici Ventus, Sir Robert McAlpine and Laing O’Rourke.
However, all these solutions mean little if the concrete sector does not have the capacity to deliver. ‘This it has,’ assured Andrew Minson, executive director of MPA-The Concrete Centre. He explained how all the constituent parts for concrete foundations can be locally sourced from the UK, there is no volume issue for aggregate requirements and the predicted maximum peak demand for cement for offshore foundations would only equate to about 4% of UK capacity.
The supply chain required to deliver gravity foundations would be further enhanced by the facility developments being undertaken by UK ports. Tim Davies of Royal Haskoning described what ports need to offer to facilitate offshore wind farm manufacturing. This includes easy land and sea access, local skills base, land for manufacturing facilities and deep water quays. He pointed out that small ports, in particular, are prepared to develop dedicated facilities, while some larger ports have the flexibility to provide mixed-use and change deep-berth locations for use by the offshore wind industry. Like the construction industry, the ports see offshore wind power as a growth market and are prepared to invest in the necessary infrastructure.
The last word, appropriately, went to James Staniland of Forewind. Forewind is a consortium comprising four leading international energy companies which joined forces to bid for the Dogger Bank Zone Development Agreement as part of The Crown Estate’s third licence round for offshore wind farms. Dogger Bank is the largest of the Round 3 zones with a potential of 13GW. This equates to almost 10% of the UK’s projected energy requirements.
Mr Staniland reported that a number of foundation options are currently being considered. As Forewind are now carrying out the necessary assessments and planning required for the consent process, he urged those companies and consortia with a solution to provide details sooner rather than later otherwise it may be too late for document submission to the regulatory authorities.
The conference demonstrated the significant investment that the construction industry is making in the development of innovative cost-effective solutions that can be delivered by an efficient supply chain. These efforts are being brought together by the Interest Group for Gravity Foundations - Offshore Wind whose members are working with engineers, contractors and suppliers to further increase the wind industry’s awareness of the tangible buildability, cost and environmental benefits that can be achieved using gravity foundations for offshore wind farms.