Goulding Fertilisers choose Smiley Monroe
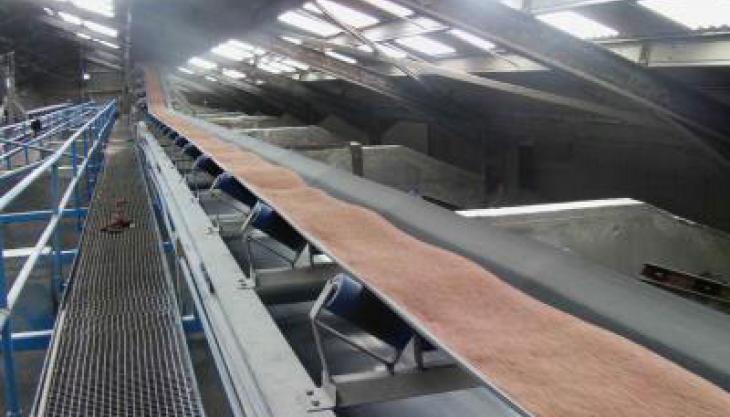
Specialized conveyor belts and conveyor components supplied to Irish fertilizer company
Smiley Monroe Ltd have recently supplied specialized conveyor belts and conveyor components for Goulding Fertilisers’ new intake conveyor system, in their Co. Limerick plant. Smiley Monroe won the business due to their previous experience in this sector and having demonstrated that they had the right mix of products.
A division of Goulding Chemicals Ltd, a wholly owned subsidiary of Origin Enterprises plc, Goulding Fertilisers manufacture and distribute a complete range of NPK fertilisers, trace-element fertilisers and granulated lime in Ireland. They supply mainline and customized blended products to suit local nutrient requirements and pride themselves in offering quality products and service backed up by their full time laboratory.
David Mullan, Smiley Monroe’s Ireland sales manager, explained: ‘When Goulding Fertilisers approached us to assist them with their new intake conveyor system, we drew on our previous experience working with Richardson Fertiliser, Irish Fertiliser and Kemira, to specify all of their oil- and chemical-resistant conveyor belts and conveyor components.’
Stephen Reidy, production manager with Goulding Fertilisers, commented: ‘We’re running two stainless steel elevators feeding conveyors with tripper cars, with an output of 400 tonnes/h, dropping product into bays below. Due to the highly corrosive nature of fertilizer, our new intake conveyor system is fitted with plastic catwalks, stainless steel handrails and Smiley Monroe’s anti-corrosive King Rollers. We also installed Smiley Monroe’s glide trackers on the return side of our conveyor belts, which we’ve found to be of benefit.’
Steel conveyor rollers have a severely limited life span in such a corrosive environment, whereas the self-cleaning King roller benefits from a strengthened high-density polyethylene (HDPE) frame construction, which is anti-corrosive, so it won’t rust and cause expensive belt damage. The low-friction surface greatly reduces carryback material build-up on the roller face - the main cause of belt tracking problems, material spillage, premature wear and failure of steel rollers. Another important advantage of the King roller is its triple labyrinth seal, which protects the sealed-for-life bearings from moisture and dust damage.
David Mullan continued: ‘The customer chose King Rollers with stainless steel shafts, which are ideal for use in fertilizer plants. They don’t just deliver longer service life, but also satisfy a growing demand for energy-saving products that keep running costs down. In today’s world of ever-rising energy costs, King Roller’s lightweight yet robust design can help reduce belt tensions and power requirements by up to 20%. To ensure a spillage free feedpoint and to protect the conveyor structure, we recommended four Smiley Monroe Glide tracker rollers be fitted to each conveyor. Glide Tracker is another of our low-maintenance products that keeps the conveyor belt central to the conveyor. In addition, conveyor belt cleaners were fitted to the return side of the belts to eliminate carryback material.’