Energy-efficiency improvements at Quinn Lite
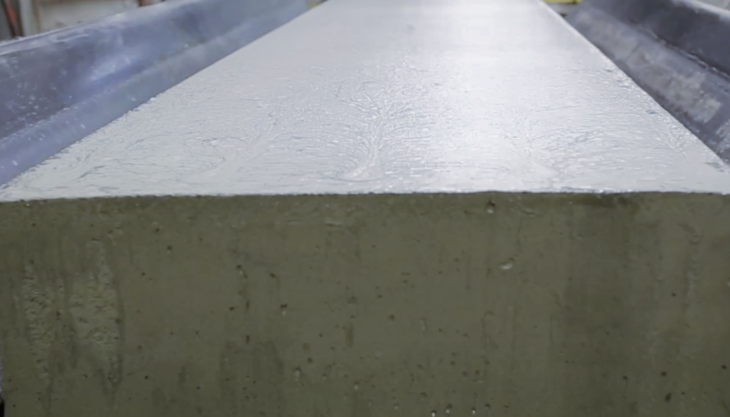
Aircrete block producer introduces number of measures to reduce energy usage in manufacturing process
QUINN Lite have introduced a number of measures to reduce energy usage and waste in the manufacturing of their aircrete blocks.
Having reviewed their manufacturing process in a bid to determine where improvements could be made to ensure minimal environmental impact and to maximize efficiencies, a series of improvement measures have been implemented in the last four months which have already seen a return.
A new heat-exchanger system has been installed in the plant to capture the excess heated water produced for re-use in the manufacturing process. The energy is no longer wasted, but instead is now pumped back into the system to heat the pre-curing chamber and help maintain the optimum temperature.
Achieving a temperature of 36–40 degrees in the pre-curing chamber is an important part of the manufacturing process to ensure the liquid ‘cake mixture’ achieves the right consistency.
It is during this stage of the process that a chemical reaction occurs between the raw ingredients which forms gases and fills the mixture with tiny pockets of air and gives Quinn Lite blocks their lightweight and thermal properties.
However, achieving and maintaining the correct ambient temperature in the chamber requires energy usage. In order to further reduce this energy requirement, Quinn Lite also insulated the entire chamber with Quinn Therm insulation, significantly reducing heat loss and energy requirements without increasing production time.
In addition, the new system allows greater control over the temperature of the pre-curing tunnel, which is regulated to prevent excess heat and energy.
Quinn Lite say the changes introduced help to ensure a constant temperature for this crucial stage of manufacturing and also help to more evenly dispersed the heat throughout the cake mixture, further improving the block quality.
The newly enhanced facilities also have a knock-on benefit of allowing for a reduction in lime content in the Quinn Lite mix. The lime ingredient, which is used as a heating agent, is supplied by a third party, so reducing the quantity saves on both production costs and transport requirements, thereby further reducing the carbon footprint.
Commenting on the recent changes, Quinn Lite’s production manager, Kieran McGorman, said: ‘The changes we’ve made form part of a larger, company-wide drive to minimize the impact of our operations on the environment and to maximize efficiencies wherever possible.
‘Given the nature of the Quinn Lite blocks, these improvements in energy efficiency, reduced waste and greater thermal efficiency are very fitting and will give customers even greater confidence that they are using a more sustainable product.
‘We’ve already seen very promising results from the changes, both in financial return and in energy savings, and we expect this to improve further in the coming months as the changes bed in and efficiencies are maximized.’