Effective conveyor transfer point design
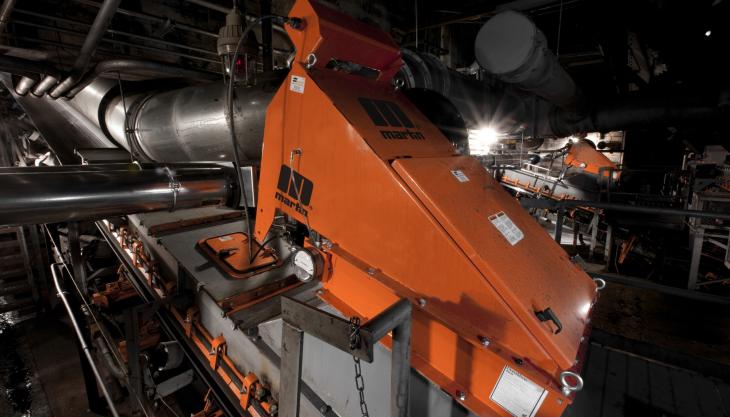
Material containment for safety and efficiency: key advice for cleaner, safer, more productive conveying
AS tonnes of material per hour are quickly dropped with great force through receiving chutes on to a receiving conveyor, fugitive cargo often piles up around the frame and dust migrates throughout the area, collecting on idlers, pulleys and floors, and affecting air quality.
Workers have to continuously clean up the material before it encapsulates the belt, potentially exposing them to a hazardous work area around a moving conveyor, where even incidental contact can result in serious injury in a split second. Considering that most conveyor injuries occur though routine maintenance or clean up, controlling fugitive material is becoming one of the primary elements in a well-organized effort to reduce hazards and prevent injuries.
‘Conveyor operators need only take a broad look at the expense that fugitive material has on a system to realize the full cost that accompanies inefficient transfer point designs,’ said Jerad Heitzler, product specialist at Martin Engineering.
‘Problems such as improper belt support, badly sealed chutes, damaged idlers and uneven cargo distribution can all result in spillage and belt mis-tracking. They also contribute to increased costs for lost material, premature equipment failure, maintenance and clean-up, as well as the potential for injury and compliance issues. These factors raise the cost of operation and reduce profit margins.’
In a properly engineered transfer point, each component, from the chute design to the cradles and dust seals, is employed to maximize its specific function and contain dust and fines, whilst at the same time offering workers easy access for maintenance.
Transfer points
Containment is the key to avoiding spillage and dust, and there are a number of components designed for this purpose. Although shaped transfer chutes and rock boxes direct the material flow to mitigate the concussion of material on the belt, most high-volume operations need one or more impact cradles to absorb the force of the cargo stream.
Heavy-duty impact cradles can be equipped with rubber or urethane impact bars with a top layer of slick UHMW plastic to minimize belt friction. Able to withstand impact forces as high as 53.4–75.6kN and drop heights of up to 15.2m (50ft), support beams in the centre of the cradle are set slightly below the receiving belt’s line of travel. In this way, the belt avoids sustained friction when running empty, yet can absorb hard impacts during loading, while still retaining a tight belt seal.
Within the settling zone – located after the impact cradle in the conveyor chute box – slider cradles can then create a troughed belt to center the cargo and reduce disruption quickly, aiding in dust settlement. Slider cradles, located down the length of the skirted area, have several functions. One is to create a trough angle that adequately centres the load. The trough angle also plays an important part in retaining a tight seal between the belt and the skirt. Lastly, utilizing track mount idlers in between each cradle, a smooth belt path is created through the settling area – one that can be easily maintained. A smooth belt path should have no gaps, minimizing disruption and promoting containment, allowing dust and fines to settle into the cargo stream prior to leaving the containment area.
Airflow
With a constant stream of material crashing on the impact point of the receiving belt, the transfer point can be extremely turbulent, and this turbulence must be contained. By slowing the airflow in the skirted area, suspended dust is allowed to settle on to the cargo path. To contain the mixture of air and disrupted material, a stable, correctly supported belt is needed for the sealing components to function properly. Without a stable beltline, the belt will sag between idlers, and sealing components will not prevent air and fine material from escaping out of the resulting gaps, causing spillage and dust emissions.
Chute sealing
By closing gaps and keeping a tight seal on the belt, apron seals can also be attached to the chute walls to prevent fugitive dust and fines from escaping. ‘A crucial requirement in any transfer point designed for reduced spillage and high efficiency is an effective skirting and wear liner sealing system at the edge of the belt,’ explained Mr Heitzler. ‘Modern designs feature external skirting, which establish the tight belt seal needed to eliminate fugitive dust and fines.’
The external design requires minimal tools and no confined space entry to inspect, adjust or replace wear liners or skirts, and in most cases can be performed by a single worker. The low profile of the skirting assembly needs only a few inches of clearance, allowing installation and maintenance in space-restricted areas. The design of these components significantly reduces scheduled downtime and the potential workplace hazards associated with replacement and adjustment.
Dust filtration
In operations with limited space for a settling zone or especially dusty materials, dust bags and curtains may be essential components. Providing passive relief via positive air pressure created at belt conveyor loading zones, dust bags prevent the escape of airborne particulates by venting the air and collecting dust at the same time.
Installed at the exit of the loading zone and mounted in the skirtboard cover, dust curtains can help create a plenum for dust suppression and dust collection. For additional dust control, an integrated air-cleaner system (pictured) can be installed at the point of emission, containing a suction blower, filtering elements and a filter-cleaning system.
Conclusion
Managers concerned with the overall safety and cost of operation need to review potential hazards, the impact of rising labour costs for clean-up and maintenance, combined with the expense of potential fines or forced downtime, to determine specifically how they can affect the bottom line.
Using the technologies described above, even poorly performing conveyors often do not need to be replaced or rebuilt, but merely modified and reconfigured through the installation of modern equipment by knowledgeable and experienced technicians.
‘These improvements will help operations improve efficiency, reduce risk and contribute to regulatory compliance,’ said Mr Heitzler.