Dust control for free-flowing materials
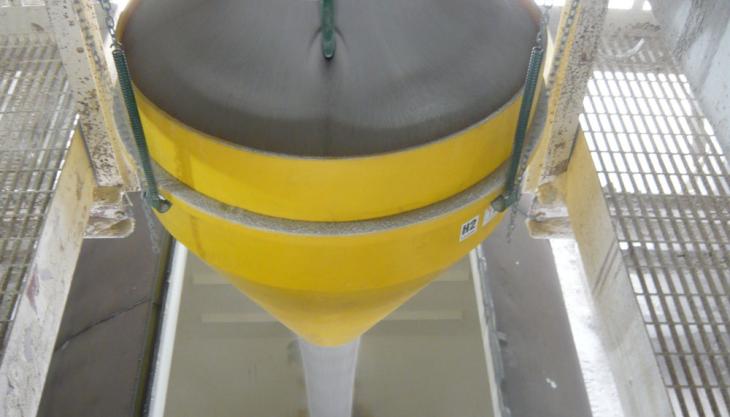
Patented dust-suppression hopper virtually eliminates dust emissions during transfer processes
DUST control has always been a major challenge in the commercial handling of powdery, granular or other free-flowing materials. Depending on the material being handled, dust may not just be unpleasant and unsightly – it can cause health issues, environmental hazards and even the risk of explosion.
Many processing, storage and handling plants may think they have little choice other than to try and cope with a dust-polluted atmosphere, but the patented dust-suppression hopper solution distributed throughout England and Wales by T H WHITE Projects virtually eliminates dust during transfer processes.
Manufactured in New Zealand by DSH Systems Ltd, the dust-suppression hopper is an easily installed loading spout that is mounted immediately beneath an existing feed point. It is particularly suitable for use where free-flowing products need to be packed, bagged, or loaded into ships, railway wagons, trucks, silos or storage bins.
Simple in design, yet highly effective, the dust-suppression hopper funnels material through a restricted orifice and cone, causing it to adopt a swirl. As the material exits the nozzle a combination of surface tension, compression and the induced vortex holds it together in a tight, highly controlled stream that contains any dust within the column.
The standard version has no internal moving parts and requires no power – it is simply configured before use according to the type of material being dealt with. Where several different types of material may need to be out-loaded from the same conveying system there is an advanced model featuring a computerized positional feed control.
Both models are available in a range of 10 sizes and can be made from standard polyethylene or tougher materials, including steel (mild steel, electro-galvanized, Corten, Hardox etc) where aggressive or abrasive materials are being handled. 304-grade stainless steel can also be specified for the handling of warm or abrasive materials, and 316-grade stainless steel for corrosive materials.
Inspired by the need for safer handling of fertilizers, the design of the dust-suppression hopper has proved to be equally effective when handling most other free-flowing granular materials, such as sand, gravel, limes, minerals, pellets and chemical powders.
Mineral and chemical plants including mines, quarries and glass works can benefit from far tighter control of potentially hazardous materials, whilst at ports – where it is important to control dust drift while loading ships or transferring goods between ships and rail, road or storage facilities – the benefits are equally rewarding.
Containment of dust is a considerable benefit in providing a safer, healthier environment for the workforce, but it also minimizes wastage and increases the yield of saleable product, which can lead to savings in cleaning and maintenance, resulting in rapid pay-back for an initial small investment.