D&E Roberts Ltd return to Thompsons bodies
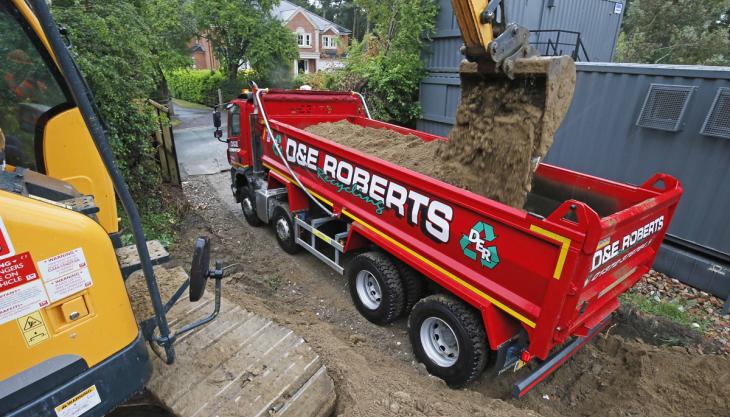
Recycling firm takes delivery of four new DAF trucks equipped with Loadmaster bodies
HAVING invested £4 million in upgrading their factories, Thompsons are starting to realize the significant benefits of utilizing high technology automated production systems. Particularly notable is that these advances are quickly being recognized by long-standing customers, such as D&E Roberts Ltd of Leatherhead, in Surrey.
Company director Dave Roberts said: ‘We’ve long preferred Thompsons bodies, but in the past, such was the demand for them that we found their delivery times just getting longer and longer, so regrettably we had to look elsewhere.
‘However, we’ve been impressed by the way Thompsons has really tackled the issue head on by committing to such a large investment programme to boost production capacity in their factories.’
He continued: ‘As a result, we’ve just taken four new Loadmasters into our fleet: three being standard front-end tippers; and the fourth a tipper grab. And we can see that the new factory systems are bringing other benefits too, because our new vehicles show that Thompsons product quality is actually better than ever.’
Key areas of Thompsons’ factory enhancements include a new TRUMPF 3030 laser-cutter installed at the OEM’s Croydon factory, while at their northern operation in Blackburn, the site now boasts a new automated robot welding system that can reduce the welding time required for bodysides and tailgates by over 80%.
Scott Burton, joint managing director of Thompsons, commented: ‘D&E Roberts has been buying our tipper bodies since the early 1990s, so we are delighted that customers are now recognizing the ongoing efforts that we are making to boost production capacity and extend even further our product quality.’
D&E Roberts’ four new 460hp DAF CF trucks are currently hard at work to meet the increasing demand for the contractor’s tipper services. Three of the standard tippers are fitted with a single-skinned steel Loadmaster Lite body, complete with a front-end cylinder to provide a competitive unladen weight of 12,400kg.
In contrast, the contractor’s DAF grab truck is equipped with a full-spec, double-skinned, all-steel Thompsons Loadmaster body working in conjunction with a Palfinger Epsilon crane. Each vehicle also features a Thompsons air-operated tailgate.
Mr Roberts said: ‘Loadmasters have always been the best tipper bodies available and now they’re better than ever. In particular, it’s the final fit and finish that really impresses, not least the outstanding quality of the paint. I’m delighted that Thompsons is, once again, at the forefront of our fleet.’