CEMEX reduce use of plastic and timber
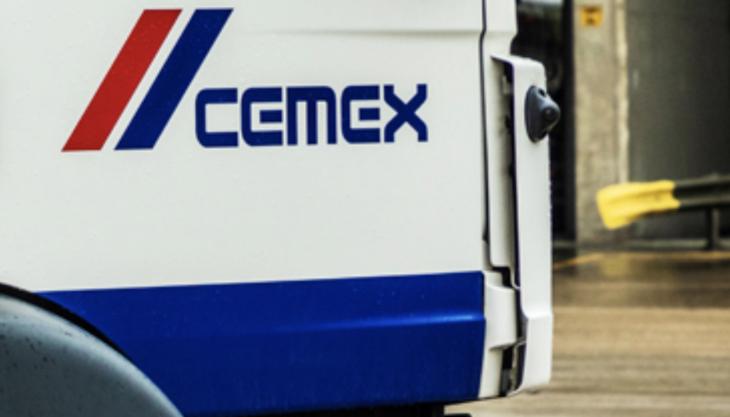
Building products business making significant reductions in line with Future in Action programme
CEMEX have committed to a robust programme of reducing the plastic packaging of their concrete products across a comprehensive range of sustainable urbanization solutions.
The company’s key building products plant at Northfleet, in Kent, has made significant inroads over the last 12 months. This follows on from the recent launch of ReadyBlock Zero, the UK’s first zero-carbon concrete block, as CEMEX’s urbanization solutions business continues to improve the sustainability of its operations in line with the company’s global Future in Action strategy, which is committed to Net Zero CO2 in concrete by 2050.
Production equipment at Northfleet has been upgraded through a £100,000 capex investment to facilitate increased supply and ongoing maintenance. The new high-strength banding process means that plastic hoods are no longer required on dense and lightweight bricks and concrete blocks. As a result, Northfleet has eradicated 6.1 tonnes of plastic (the equivalent of more than 65,000 plastic water bottles) per year from its traditional plastic packaging process.
In addition to plastic reduction, Northfleet is continuing to make environmental savings in timber by increasing the volume of void packs, which reduces the volume of timber-palleted products. More than 100 tonnes of timber were saved in 2021 and this figure is expected to increase in 2022. The programme is further supported by CEMEX’s pallet-recovery scheme, which works with merchants and distributors to recycle and reduce timber waste across the supply chain, to make greater environmental efficiencies.
Damien Allen, CEMEX’s business manager for building products UK, commented: ‘We have been pushing a more sustainable approach to our packaging in concrete products. At our Northfleet plant, our results so far are very encouraging. We expect our usage of plastic and timber to reduce further in 2022 due to the upgraded process.
‘Our equipment meets the highest quality requirements. It is extremely reliable, requires little maintenance, and is highly energy-efficient too. We are looking at lots of different options to continuously improve our packaging, without compromising product quality. This includes a constant watching eye on recycled materials and our approach to repair and re-use across the plant, in line with the circular economy mindset.’