Canning Conveyor lend a hand on Guernsey
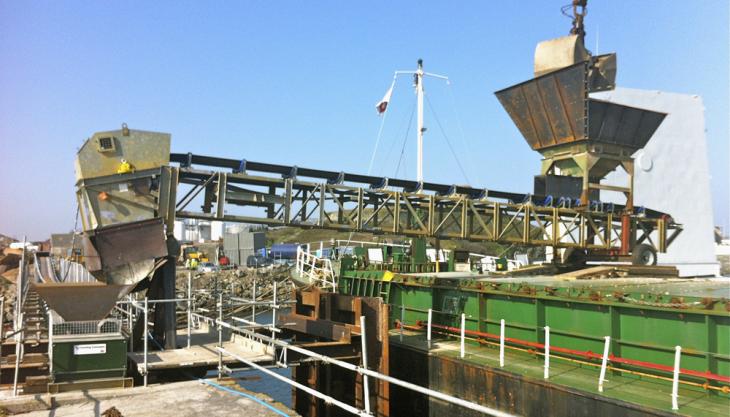
Bespoke conveying system playing a vital role in the redevelopment of Guernsey Airport
CANNING Conveyor have recently supplied an aggregate conveying system for construction work on the £80 million redevelopment of Guernsey Airport.
With planning approval for the Guernsey Airport Redevelopment Project granted in October 2011, work commenced in January 2012 and will take approximately two years to complete.
The project includes the rehabilitation and reconstruction of the existing airfield pavements, including the runway, apron and taxiways, and the installation of a new surface-water drainage system.
The bespoke conveying system, which has been supplied on hire, was designed and manufactured by Canning Conveyor for the sole purpose of conveying incoming aggregates from ships at Guernsey Docks.
Designed to accept 200 tonnes/h of –20mm aggregates, the system includes a conveyor-mounted receiving hopper that is fed by a barge-mounted 360° grab. Mounted centrally, the hopper feeds material on to a 16m long ship-to-shore conveyor which incorporates a number of unique features to cope with the rise and fall of the tide.
For example, the tail end of the conveyor is fitted with a pneumatic-tyred wheel bogie which runs on the hatch cover of the ship, while the head section is mounted on a support trestle that is para-bolted to a new concrete pad on the sea wall and fitted with a slewing and pivoting arrangement which allows the tail end of the conveyor to rise and fall.
An additional feature allows the tail end to be lifted by the ship-mounted grab and slewed around to a resting position on the sea wall during high winds or gales.
Aggregate is delivered from this conveyor on to a 50m long ground conveyor that runs horizontally on the quayside and feeds into the receiving hopper of a 12m long stockpile conveyor. The stockpile conveyor, which elevates the material to a height of 4m, discharges into waiting dumptrucks or, alternatively, stockpiles the material on the ground.
The ground conveyor is powered by a Canning SuperDrive motorized 22kW single drive drum, which has been specifically designed to operate in this type of application. Its motor, gearbox and bearings are all totally enclosed and hermetically sealed inside the steel-shell drum.
The Canning SuperDrive is said to offer many benefits including extremely low maintenance costs (ie none, other than a recommended synthetic oil change after 30,000 running hours) and 97% efficiency compared with approximately 85% efficiency on conventional drives.
The single drive drum, which delivers a belt speed of 1.6m/s, is fitted with ceramic lagging and includes a high-tension bend pulley, jib discharge drum, loop bend drum and a primary and secondary belt scraper.
Featuring a discharge chute with integral crash box and hinged inspection hatch, the entire ground conveyor unit is mounted on a substantial skid-mounted frame with cantilevered jib discharge. Complete with a loop take-up unit and heavy-duty tail-end loading section, the conveyor structure comprises Canning intermediate bays and Cannoflex belting throughout.
Designed and manufactured in the Canning workshops, the entire system is providing an effective and reliable system for the handling of incoming aggregate for Guernsey’s huge airport redevelopment project.