Australian success for Pilot Crushtec
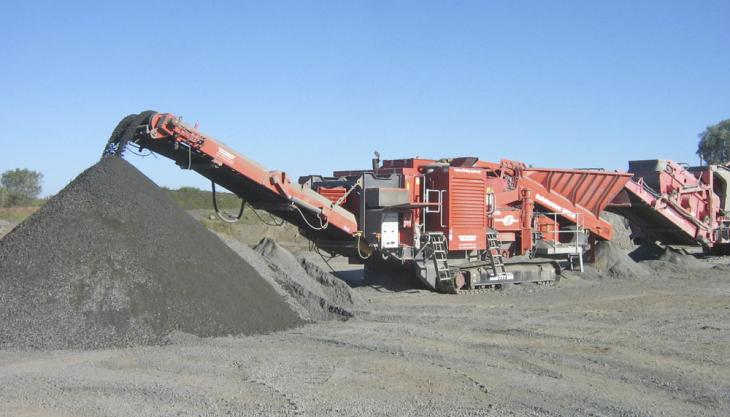
Company sees strong demand for its TwisterTrac VS350 VSI crusher in markets Down Under
SOUTH African crushing and screening specialists Pilot Crushtec International say they have found a ready market in Australia for their TwisterTrac VS350 vertical-shaft impact (VSI) crusher.
With four units already in operation Down Under and a further two crushers on order, the VS350 model will have earned the company export earnings of around R25 million (€1.85 million) in the space of six months.
The TwisterTrac VS350 is the latest and largest addition to the TwisterTrac range of track-mounted self-driven VSI crushers. Designed for tertiary and quaternary crushing applications, its primary applications are the production of sand, fines and the quality enhancement of aggregates. Powered by a CAT C15 diesel engine that produces 403kW at 2,100 rev/min, the TwisterTrac VS350 offers a choice of rotors depending on the end-use application.
Paul Chappel, export sales engineer for Pilot Crushtec, said the he TwisterTrac VS350s that have been supplied to the company’s Australian dealers are refined versions of the prototype TwisterTrac VS300, which was launched 18 months ago.
‘We firmly believed that there was a need for a high-volume tracked VSI crusher and this is certainly the case in Australia, which has become a large-tonnage market for roadbase material,’ he explained. ‘Mobile jaw and cone crushers have been developed to handle higher throughputs, but we identified the need for a tertiary tracked product to keep up with this higher pace of output.’
The primary use of these units has been in the production of aggregate and fines for roadbase material to repair the massive flood damage recently inflicted on Queensland’s roads. Special emphasis has also been placed on ease of service and access to key components, as plant hire is an important segment of the Australian market.
‘Pilot Crushtec International took on board all our suggestions and have given us a product that increases tonnages while shaping aggregate and producing fines material,’ said Ronnie Bustard, sales manager of Finlay Screening and Crushing. ‘Its simplicity means that any minor problem can be easily identified over the phone to get the machine back up and running.’
Mr Chappel added that increased throughput had been achieved with the installation of the CAT C15 engine and uprated hydraulics, with the inclusion of a bypass or ‘cascade’ system which regulates the rate of material feed into the crusher rotor.
‘If substantial extra fines are needed, more material is fed into the rotor,’ he explained. ‘Should only a minimal amount be required, a higher proportion of feed is directed to bypass the rotor, having the double effect of increasing throughput and yielding savings in fuel consumption and mechanical wear on the rotor.’