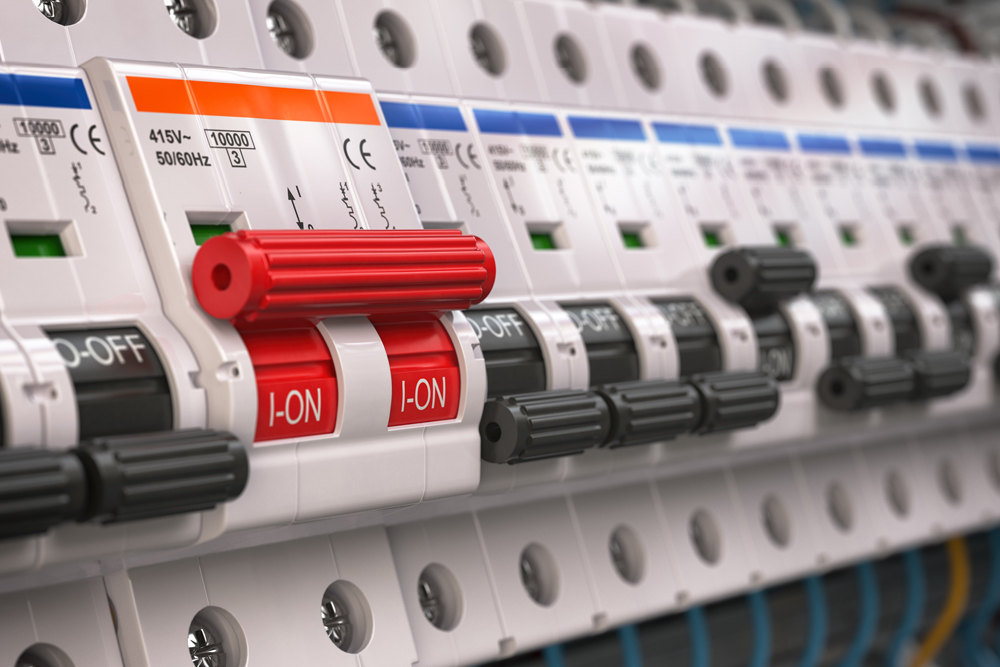
Get your act together on electrical safety. We have discussed this topic before but it is a ‘Hot Topic’ for the HSE in 2018.
QNJAC have recently published some guidance on electrical safety in quarries. It is an extremely comprehensive document and can be viewed here.
The document is split into a number of key sections and you must read the document in full, however some of the important points are as follows:
Management
Ensure you have access to and appoint a competent person with the necessary technical knowledge and experience to advise you on electrical safety matters.
It is advisable to have one or more individuals (employee or contractor) identified as the responsible electrical person for the site, to advise you on electrical matters and manage all work on the electrical system. The responsible electrical person should be authorized in writing as to their duties, clearly defining what they are, and are not, responsible for.
The responsible electrical person should authorize all other persons, including contractors, who carry out work on the electrical system at the site, ensuring that they are competent to carry out that work and have the equipment, including suitable test instruments, to enable them to carry out the work safely.
Risk assessments
It is your duty to ensure that electricians or electrical contractors are competent and have suitable risk assessments and safe systems of work for the tasks to be undertaken.
The responsible electrical person should therefore ensure that adequate risk assessments have been completed and are included in the health and safety document for all electrical work. A basic list of activities that require risk assessment are:
- Use of electricity
- Operation and use of high-voltage equipment including maintenance
- Periodic inspection and testing of all installations and equipment
- Operation and use of low-voltage equipment
- Working on or near to live electrical equipment for the purpose of fault finding, commissioning and testing
- Testing isolated equipment to prove it is dead
- Protection against contact with overhead lines and underground cables
- Installation of equipment including cables
- Access to equipment at high level
- Risks from overhead line contacts by drivers of owned vehicles and contracted vehicles.
Examination, inspection and test
Since the guidance on electrical safety in quarries was revoked there has been some confusion on the frequency of inspection and test. The following give clear guidance on the frequency of examination, inspection and test
Low voltage
- Emergency stops and safety interlock devices – Monthly
- Manual testing of RCDs – 3 monthly
- Visual inspections (quarries) – 6 monthly
- Thermographic surveys (all sites) – 12 monthly
- Visual inspection, R2 tests and earth loop impedance results using historical R1 values (quarries) – 12 monthly
- Earth electrode testing (quarries) – 12 monthly (in dry period)
- Visual inspections (non quarries) – 12 monthly
- Visual inspection, R2 tests and earth loop impedance results (non quarries) – 3 yearly
- Earth electrode testing (non quarries) – 3 yearly (in dry period)
- Verify circuit conductors (R1) (all sites) – 3 yearly
- Insulation resistance tests (all sites) – 3 yearly
Non conformities should be categorized C1, C2 and C3 and rectified accordingly.
High voltage
- Routine visual inspection – 12 monthly
- Thorough inspection and maintenance – 5 yearly (3 yearly for oil-filled switchgear)
- Post fault maintenance of oil-filled switches and circuit breakers – Immediately after operation under fault conditions
Portable appliance
For portable appliances there are no set frequencies of inspection and test, but guidance can be found in HSE publication HSG107 - Maintaining portable electrical equipment.
Hand tools
Where possible all electrically powered hand tools should be either:
- Rechargeable battery type or,
- 110V fed from centre tapped earth supply.
Where 230V hand tools and test equipment have to be used then the equipment should be protected by a suitably rated 30mA RCD.
Electrical panels
To ensure equipment is safe when commissioning or fault finding is being carried out, the risk of contact with dangerous live parts should be prevented. The internal conducting parts of the electrical panels should be covered so that accidental or inadvertent contact cannot occur. The minimum standard of protection is IP2X (ie finger proof).
Earthing of electrical equipment
All plant including mobile crushing and screening equipment must be properly earthed. For mobile plant, slightly different rules can apply for generator-fed to free-standing equipment, so get your competent electrical person to check it out.
High-voltage systems
All high-voltage systems should be placed under the control of a competent person (employee or contractor) who has the necessary competence to properly design, use and manage the HV system on behalf of the operator.
High-voltage switchgear should be installed in locked enclosures with access restricted to competent and authorized persons only.
Check who owns the equipment, if it is you then you need to establish a system for managing the installation safely.
Isolation and lock off
Establish a robust process for the safe isolation, lock-off and testing of equipment and ensure personnel and contractors on site are fully trained, understand and follow the procedure.
Live working
Work on or near live low-voltage equipment should not occur other than in exceptional circumstances. The live working procedures should be drawn up to detail when work on or near live equipment is allowed and what precautions should be in place to ensure that work is done without the risk of injury. The work should not be carried out unless agreed by the responsible electrical person and a risk assessment and safe system of work has been agreed prior to the work commencing.
As a minimum the following must apply:
- The equipment being worked upon is safe to work on, all conductors are covered or screened to a minimum standard of IP2X so that they cannot be touched or tools dropped on them
- If using the control circuit test switch method for diagnostic testing, the control circuit conductors, if greater than 50V AC, must be screened to a level of at least IP2X
- Test leads and probes are fitted with fuses in accordance with HSE guidance note GS 38 (Electrical test equipment for use on low-voltage electrical systems) and tools are insulated
- Persons are competent to undertake the work and recognize the precautions necessary to avoid danger.
Incidents
It is your responsibility to ensure that all electrical incidents and near misses are properly and thoroughly investigated so that a root cause can be established and action taken to prevent likely occurrences.
Record keeping
The following records should be readily available:
- Underground and overhead site service plans
- Installation test certificates high- and low-voltage
- High-voltage inspection and maintenance records
- Low-voltage inspection and test records
- Portable appliance test records
- RCD test records
- Emergency stop / safety interlock test records
- Defect rectification records for all inspections and tests
- Distribution line diagrams low- and high-voltage
- Motor control circuit diagrams
- Operating and instruction manuals for equipment.
Annual audit
The Electrical Safety Management System for installations should be audited and reviewed by the responsible electrical person to ensure compliance and, where required, actions put in place to rectify any deficiencies. The audit frequency should be no longer than 12 monthly.
If you are unsure on whether you have the correct control in place then speak to your electrical engineer or contractor. Alternatively give me a call and we can arrange for our competent electrical engineers to review your installations.
Contact: Colin Nottage: colin.nottage@influentialmg.com; tel: 07799 656303.