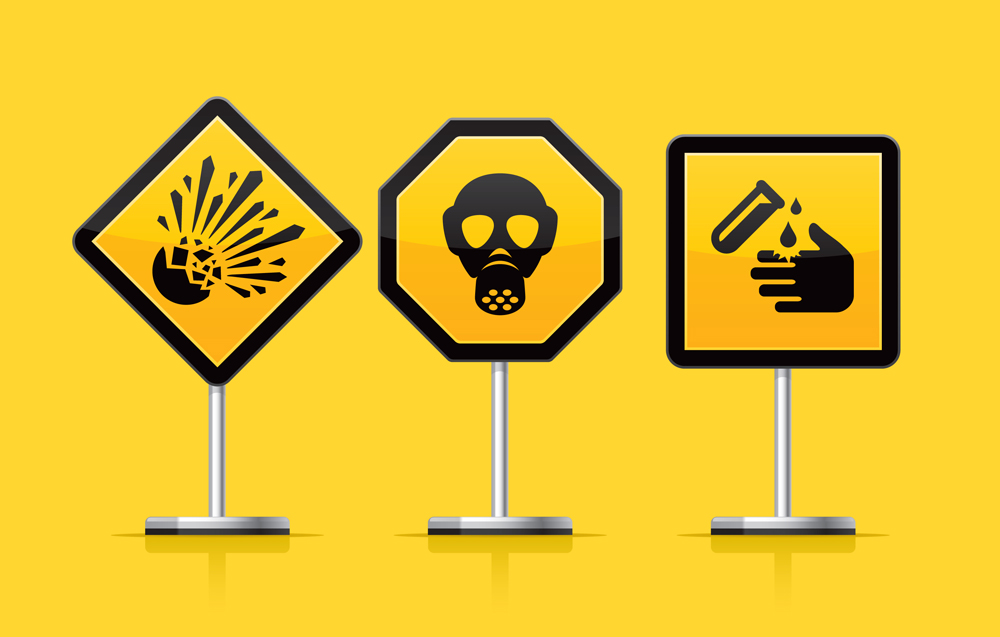
Every year exposure to hazardous substances at work affects the health of thousands of people. Frequently reported illnesses are lung disease (dusty conditions), skin irritation, dermatitis or skin cancer (frequent contact with oils, contact with corrosive liquids), occupational asthma (sensitisation to isocyanates in paints or adhesives), and occupational cancer.
Employers are obligated to protect workers and others who may be exposed to hazardous substances. The high costs of ill health arise from loss of earnings, loss of productivity, prosecution and civil action, among others.
There are many hazardous substances in use in industry today, therefore it is essential to ensure, first of all, that those being used are absolutely necessary, and that there are no safer alternatives.
Secondly, it is vital that employees and the environment are protected from the effects of these substances by the use of training and appropriate protective measures. Below you will find some simple steps that will enable you to meet the requirements of the COSHH Regulations.
-
Identify all the hazardous substances used in or created by your workplace activities and the likelihood of exposure. Consider all areas of the workplace including the production area, office and welfare facilities (cleaning fluids).
-
Obtain Material Safety Data Sheets (MSDS) as required by the Chemical Hazard (Information and Packaging) Regulations 2002 (CHIP). These come from the suppliers of the products. If you are manufacturing a product then you will have to prepare a MSDS for distribution to your employees and customers.
-
Using the Material Safety Data Sheets, identify how the substances can harm your workers.
-
If possible, remove the substances from the workplace or replace them with substances less hazardous.
-
Record the location and quantity of substances that you hold.
-
Identify what further control measures are needed to protect your workforce. These could include locked storage areas and authorized key-holders, and the provision of Personal Protective Equipment (PPE)
-
Ensure that control measures are used and maintained properly and that safety procedures are followed.
-
If necessary, monitor the exposure of employees to hazardous substances.
-
Carry out health surveillance where appropriate.
-
Prepare plans and procedures to deal with accidents, incidents and emergencies.
-
Provide your employees with suitable and sufficient information, instruction and training.
Attached is a COSHH register and a simple COSHH assessment sheet that will help you comply with the current regulations.
However, the COSHH Regulations are currently under review and in my role as chair of the Construction Dust Partnership we have been invited to make recommendations on changes to the regulations. Consideration is being given to combining COSHH, Lead at Work and DSEAR (Explosive risks) into one item of legislation.
A possible change is to call the regulations the Control of Tasks Hazardous to Health. How many people have wood on their COSHH register? Very few I suspect, but when wood is machined or cut it produces wood dust that can be very hazardous if inhaled.
A good approach is to consider substances as part of a task risk assessment process and include the effects on health and explosive risk. So, if you are doing a maintenance activity you would consider grease and dermatitis along with propane and explosions… I will keep you updated on the changes as they come along.