Wire-free Weighing
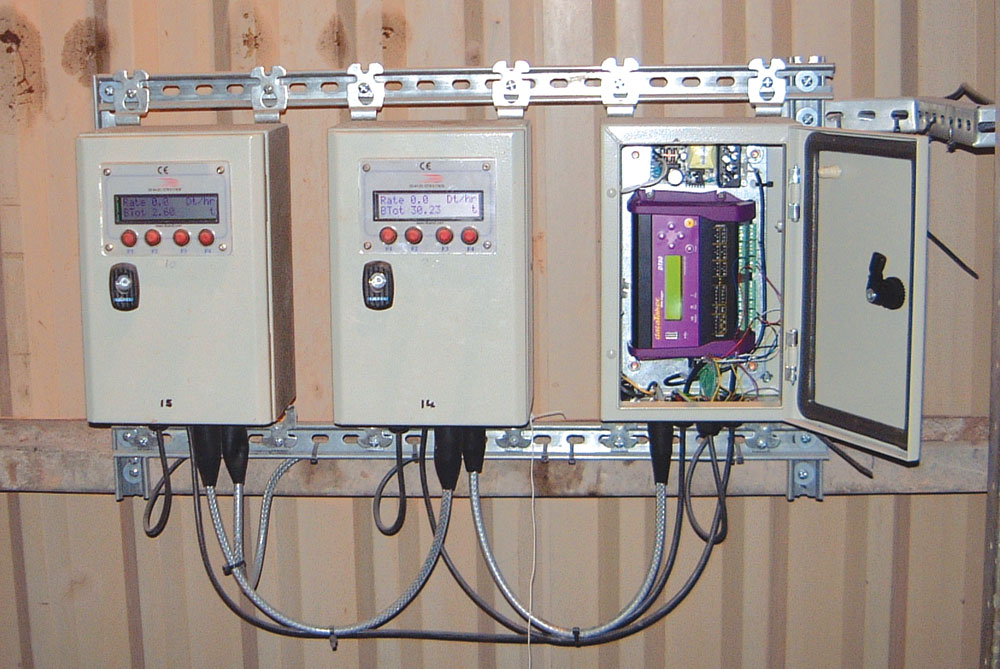
Interfacing weighing systems using radio modems
When weighing equipment is installed in an industrial facility, such as a quarry, mine, or waste-disposal site, it is often located in the noisiest, dirtiest, dustiest, smelliest and generally most difficult to access part of the plant. As a result, nobody wants to go there, least of all with a pen and paper to read the weigher data.
In the past, one solution to this problem was to site the electronics somewhere more salubrious, but this in itself can cause a problem, particularly when attempting to calibrate the instruments. For example, when calibrating a belt weigher, the top of the belt carrying the material to be weighed should be visible so that if any material passes over the belt weigher during the zero calibration routine, the test can be aborted and restarted. If the belt is out of sight of the operator it will require two people to perform this function to ensure it is done correctly. This is rarely done and sometimes leads to weighing errors.
Siting the weigher electronics
A major problem with siting the electronics in other areas of the plant is the cabling required. Cabling is expensive, time-consuming to install and can be subject to electrical noise, particularly if the load-cell signals have to travel a long way. Generally, the load-cells used on a great number of installations have a 2 millivolts per volt (2mV/V) sensitivity, so with a nominal 10V excitation voltage the maximum return voltage into the electronics will be 20mV. In practice, however, the return voltage value will be much lower than this. This signal is then amplified up to 200 times, and in some cases even more, so any electrical noise generated by devices such as inverter drives can seriously affect the accuracy of the system. In addition, long cables can cause seasonal drift as the temperature changes and the resistance of the cable core changes. This can be overcome by using a six-wire system, but again this has cost implications.
Remote instruments
One way of overcoming the problem of signal degradation is to leave the measuring instruments close to the weigher and use remote instrumentation, such as counters and rate indicators, to allow the operator to see what is happening to the plant. However, this still leaves the problem of getting a cable across the site to a suitable point for the instrumentation.
Radio modems
There are a number of radio systems that can be used to transfer information from one point in the plant to another. In order not to have to pay a radio licence fee, there are ‘free’ radio channels available. The most commonly used are in the 406–470MHz frequency range. When connecting to this type of radio modem it appears transparent to the weighing equipment, as if plugging in a cable between the items of equipment. This makes things very easy for the system builder, but with one exception. If there is a high degree of RF noise in the surrounding area, this can effect the radio transmission and, in some cases, swamp the signal so it becomes useless. Most radio modems have a series of channels that can be selected so that the system can be switched to the channel with the lowest noise.
Multiple-instrument interfaces
What if a number of instruments need to be connected into a single transmission? A multi-drop system at the instrument end is one solution, with each instrument having its own unique address when sending data on to a single cable. This type of data transfer has to be synchronized so that only one instrument at a time can send its information; alternatively, the remote device can demand data from each instrument as and when required by sending an address to each instrument. Each instrument responds when it gets its acknowledgement. A number of perfectly satisfactory transmission protocols are available for this purpose, as long as the instrument sending the data is suitable for this type of data interface.
Using a data logger
In the author’s opinion, the system that works the best involves marshalling all the remote weighers and other signals into a single data logger using the local analogue and digital interfaces. All of these signals can then be turned into a single data stream and transmitted at regular intervals. Another great advantage of using this method is that historical data can be recorded by the logging system, either in a PC or in the data logger, for use in management strategies when required. This data is easily transmitted over the Internet to other interested parties.
System costs
Using a 406–470MHz modem can prove expensive. To transmit data over a line-of-sight distance of around 20km can cost in the region of £1,200 to £1,500 for a pair of modems. Usually, however, the distances involved are not so great, often under 1km, so extra is being paid for the technology. With Bluetooth and WiFi these costs plummet.
Bluetooth interfacing
Bluetooth uses a much higher frequency (in the region of 2.7GHz) to transmit data. At these frequencies the signal tends to be more penetrative than the lower 406MHz range. This means that signals will pass through buildings and other obstructions and do not always have to be line of site. The downside is that the range is very much reduced, but the cost is significantly lower, generally under £40 per unit. These units are compact and easy to interface with existing equipment, or they can be designed into new equipment. They can be networked into a wide range of systems at a very low cost.
Range and cost considerations
Although Bluetooth devices have a much smaller range, because they are relatively cheap they can be used as repeaters, so that if the distance involved is, for example, 1km, typically three repeaters could be used to get the information to its destination. The data being transmitted can easily be encoded if privacy is a consideration and pass codes can be introduced so that only authorized personnel can access the data.
Man Machine Interfacing (MMI)
Once the data has been sent, how is it stored and displayed? If using a proprietary data-logging system, the supplier will normally provide a PC front end to extract the data and display it in graphical and spreadsheet formats. The data loggers used by Lodestone also have the facility to log the data locally on to a data stick, which can then be downloaded into a spreadsheet. Also available are relatively inexpensive serial interface systems that can display incoming data and log it on to disc, which again can be transferred to a spreadsheet.
Lodestone are also currently exploring the possibility of sending data to a mobile phone or PDA that has Bluetooth capability. This is a little way off yet but, as the boundaries between phones and computers become increasingly vague, this will become a very strong possibility in the future. The Microsoft Hyper Terminal can also be used for data collection; the data in this case can be read but not stored automatically, however, the data can be copied from the screen into a file for later use.
Putting weighers on the web
Another interesting aspect when using Bluetooth, Wireless LAN etc, is the ability to make the weighing instrument appear to be a web server. If either a landline or a mobile phone is available, or if the site where the weighers are installed has WiFi/Wireless LAN available, the LodeMaster belt weigher can be configured as a website and can be read from anywhere in the world. The Wireless LAN module contains an HTML web server that is integrated with the scripting language, allowing control of dynamic web page content from within a script and also the modification of script behaviour by data posted from a web browser. This web page can be personalized with a company logo and any other information that is required, and will contain dynamic real-time information, such as tonnes per hour, accumulated tonnes, batch tonnes, belt speed with time and date stamping. This becomes a powerful management information tool, which not only indicates site performance, but also other information such as conveyor running time and plant starting and stopping times. From these data it is possible to work out plant running efficiency and other vital plant information.
Flexibility
Another important aspect of the Wireless LAN module is its flexibility. It can be programmed at a high level. All the compilers, syntax checker and everything else required is on board. It is also relatively simple, which means the time from concept to market is very quick. Technology is galloping ahead and becoming very cheap to implement. Systems and techniques that previously could only be considered by larger companies are now available to all. The future is very bright for those who take advantage of it.
The author, Jon Scarrott, is managing director of Lodestone Electronics Ltd