What Is A Weighbridge?
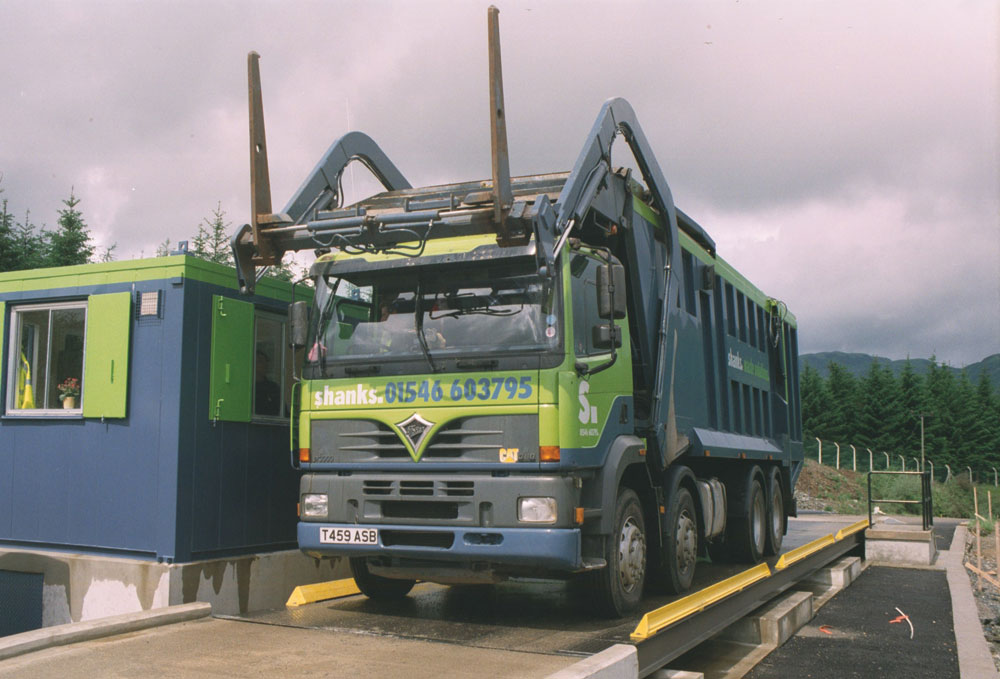
Shering Weighing take a look at weighbridge technology with a view to helping operators make the most of their investment
It seems almost patronising to ask the question: what is a weighbridge? However, an opinion often voiced is that a weighbridge is just a weighbridge, suggesting that they are seen as simple pieces of equipment that carry out a simple task. In a recent BBC Radio 2 news programme it was reported that customers were losing huge sums of money as a result of inaccurate petrol pumps and weighing scales, so it seems appropriate to look at weighbridge function and technology in more detail, as a little knowledge could go a long way in helping weighbridge owners and operators to make the right investment and ultimately save their companies money.
Made of steel or concrete (or a mixture of the two), a weighbridge is essentially a big set of ‘bathroom scales’ for trucks that connects to a readout (the digital weight indicator) which shows the weight. The system provides for the weighing of goods by vehicle load and allows companies to charge customers by weight of load supplied or delivered. The description is straightforward, but the technology to achieve the function is innovative and highly precise.
The accuracy and reliability of a weighbridge system is of paramount importance. Inaccurate weighings (ie too light or too heavy) could be causing profits to dwindle or may result in overcharging and risk ill will, lost customers and litigation problems. It is worth remembering that it is the weighbridge owner who is responsible for ensuring that the equipment is legal for trade use and maintained as such (Weights & Measures Act 1985). Failure to do so makes the weighbridge owner/operating company liable to prosecution, not the weighing company. As a minimum, an approved system (for trade use) found to be weighing out of tolerance will be shut down by a Trading Standards Officer until it is repaired, re-calibrated and re-verified. This not only costs money, but also effectively prevents a company or site from trading.
In short, a weighbridge must sustain accuracy over the long term. It must be designed to achieve reliability and be durable enough to cope with the harshest of site conditions and environments. It is therefore useful to look at how a weighbridge achieves this task through certain design criteria and the factors which contribute to weighing errors, downtime or unnecessary repairs.
The weight of the load on the weighbridge is measured by the load-cells — the highly accurate transducers that form the heart of any weighing system. Using strain gauges bonded on to a precisely machined element that deforms under load, they convert a small resistance change into a usable electrical signal. This signal is then filtered, calibrated and digitally displayed by the indicator. The wrong load-cell choice together with inferior assembly and weighbridge design can result in poor performance, regular failures and huge losses in revenue. Compression load-cells are the most popular choice for weighbridges, and multi-column products, such as those used by Shering, sustain their accuracy and offer a low-profile reliable solution.
Owing to the precision engineering element of load-cells, the environment surrounding them has to be suitably controlled as weighing errors or load-cell failures may occur. This is especially relevant as the load-cell itself is a particularly expensive component in a weighbridge system. In addition, replacement means additional costs associated with labour, re-calibration, hire of a weighbridge calibration unit and, in the case of trade-approved systems, re-verification. It is of paramount importance, therefore, that this element is protected to the utmost.
The most obvious weighing failure is often the result of a direct impact overload, ie when one or more load-cells have a load applied in excess of acceptable tolerances. The acceleration and momentum of vehicles often cause very large instantaneous loads to be applied to the weighbridge, far greater than the expected static load. In order to cope with this a weighbridge should be designed to withstand a considerable amount of overload. Generally, the higher the designed overload is, the more robust and accurate the weighing system will be. For example, the theoretical maximum load that can be applied to a Shering weighbridge before any damage is sustained is massively in excess of its rated capacity.
The weighbridge structure should also take into consideration the momentum created when a truck traverses and applies its brakes on the deck. As kinetic forces are transferred from the deck to the ground, it is important to avoid transmitting these forces through the ‰ load-cells. Typically, most weighbridge decks ‘float’. However, the key design criteria should allow freedom to ‘float’ but restrict movement to the absolute minimum, thereby preventing damage from these kinetic forces. An essential requirement on any high-tech, high-quality weighbridge is a restraining mechanism which can disperse these forces away from the load-cells and mountings. Inadequate or faulty restraint systems can result in excessive movement of the weighbridge deck, thereby magnifying these forces to a destructive level that can seriously affect the structural integrity of both the weighbridge and the foundations, not to mention the accuracy, as illustrated in figure 1.
In the case of the Shering weighbridge system, deck movement is restricted to 1mm in any direction using the company’s patented restraint post system. This system is mounted at the centre of the weighbridge for a very important reason — it compensates for the environmental temperature changes that radically alter the lengths of all weighbridge structures. Tackling this problem is a major factor in weighbridge design. For example, the restraint post system successfully overcomes all expansion and contraction issues by eliminating any need for end-restraint measures which create excessively large gaps and allow potential excessive movements as described above.
Lightning strikes also threaten a weighbridge system. Contrary to popular belief, it is not a direct strike (actually a very rare occurrence) that should concern weighbridge owners/operators, but a hit to a nearby object. When lightning strikes an object the power dissipates radially across the ground, similar to the effect seen when a stone is thrown into water. If a conductor is placed in the path of this power dissipation, extremely large eddy currents can be induced. It is these eddy currents that cause failures in weighbridge electronics and load-cells. Most weighbridge manufacturers include some kind of lightning protection in their designs, and the pros and cons of each type can be debated ad infinitum. When choosing a new weighbridge system, however, it is worth considering the manufacturer’s claims on lightning protection and the purchaser should not be worried about asking awkward questions. For example, if a manufacturer claims that load-cells are protected by bypassing them with earth straps, it is pertinent to ask how the earth strap bypasses the load-cell. This is only possible if the load-cell is isolated by an insulator of some kind. Similarly, if a manufacturer states that surge protection is fitted to absorb the energy of a lightning strike, the purchaser should ask how long it takes to react. In the instant before it reacts (and there will always be one) what happens to the equipment which is at that point, in effect, unprotected?
Weighing errors can also be due to cable damage caused by abrasion, water ingress or rodents. A good-quality weighbridge system should include comprehensive cable protection, such as Shering’s waterproof flexible conduit system. This helps prevent cable exposure, limits damage and adds an extra level of protection against water penetration in the load-cell junction boxes.
A quality weighbridge will successfully achieve the task of weighing goods, which is essential for many businesses. Today, however, weighbridge owners and operators can also reap the benefits of unmanned systems, state-of-the-art weighbridge software designed for individual needs, remote operation and integration into existing in-house systems. However, to protect any weighing system investment, it is vital that the technology behind the design of the weighbridge is understood. Armed with this knowledge, companies will be better equipped to purchase the right weighbridge for their needs and better able to maintain it appropriately.
This article was written by Kimberley Anderson, with technical contributions from Bob Matthews, Shering’s general manager (systems & electronics) and Chris Watt, general manager (engineering & design).
Shering Weighing Ltd, Pitreavie Business Park, Dunfermline, Fife KY11 8UL; tel: (01383) 621505; fax: (01383) 620262; email: sales@shering.com; website: www.shering.com
It seems almost patronising to ask the question: what is a weighbridge? However, an opinion often voiced is that a weighbridge is just a weighbridge, suggesting that they are seen as simple pieces of equipment that carry out a simple task. In a recent BBC Radio 2 news programme it was reported that customers were losing huge sums of money as a result of inaccurate petrol pumps and weighing scales, so it seems appropriate to look at weighbridge function and technology in more detail, as a little knowledge could go a long way in helping weighbridge owners and operators to make the right investment and ultimately save their companies money.
Made of steel or concrete (or a mixture of the two), a weighbridge is essentially a big set of ‘bathroom scales’ for trucks that connects to a readout (the digital weight indicator) which shows the weight. The system provides for the weighing of goods by vehicle load and allows companies to charge customers by weight of load supplied or delivered. The description is straightforward, but the technology to achieve the function is innovative and highly precise.
The accuracy and reliability of a weighbridge system is of paramount importance. Inaccurate weighings (ie too light or too heavy) could be causing profits to dwindle or may result in overcharging and risk ill will, lost customers and litigation problems. It is worth remembering that it is the weighbridge owner who is responsible for ensuring that the equipment is legal for trade use and maintained as such (Weights & Measures Act 1985). Failure to do so makes the weighbridge owner/operating company liable to prosecution, not the weighing company. As a minimum, an approved system (for trade use) found to be weighing out of tolerance will be shut down by a Trading Standards Officer until it is repaired, re-calibrated and re-verified. This not only costs money, but also effectively prevents a company or site from trading.
In short, a weighbridge must sustain accuracy over the long term. It must be designed to achieve reliability and be durable enough to cope with the harshest of site conditions and environments. It is therefore useful to look at how a weighbridge achieves this task through certain design criteria and the factors which contribute to weighing errors, downtime or unnecessary repairs.
The weight of the load on the weighbridge is measured by the load-cells — the highly accurate transducers that form the heart of any weighing system. Using strain gauges bonded on to a precisely machined element that deforms under load, they convert a small resistance change into a usable electrical signal. This signal is then filtered, calibrated and digitally displayed by the indicator. The wrong load-cell choice together with inferior assembly and weighbridge design can result in poor performance, regular failures and huge losses in revenue. Compression load-cells are the most popular choice for weighbridges, and multi-column products, such as those used by Shering, sustain their accuracy and offer a low-profile reliable solution.
Owing to the precision engineering element of load-cells, the environment surrounding them has to be suitably controlled as weighing errors or load-cell failures may occur. This is especially relevant as the load-cell itself is a particularly expensive component in a weighbridge system. In addition, replacement means additional costs associated with labour, re-calibration, hire of a weighbridge calibration unit and, in the case of trade-approved systems, re-verification. It is of paramount importance, therefore, that this element is protected to the utmost.
The most obvious weighing failure is often the result of a direct impact overload, ie when one or more load-cells have a load applied in excess of acceptable tolerances. The acceleration and momentum of vehicles often cause very large instantaneous loads to be applied to the weighbridge, far greater than the expected static load. In order to cope with this a weighbridge should be designed to withstand a considerable amount of overload. Generally, the higher the designed overload is, the more robust and accurate the weighing system will be. For example, the theoretical maximum load that can be applied to a Shering weighbridge before any damage is sustained is massively in excess of its rated capacity.
The weighbridge structure should also take into consideration the momentum created when a truck traverses and applies its brakes on the deck. As kinetic forces are transferred from the deck to the ground, it is important to avoid transmitting these forces through the ‰ load-cells. Typically, most weighbridge decks ‘float’. However, the key design criteria should allow freedom to ‘float’ but restrict movement to the absolute minimum, thereby preventing damage from these kinetic forces. An essential requirement on any high-tech, high-quality weighbridge is a restraining mechanism which can disperse these forces away from the load-cells and mountings. Inadequate or faulty restraint systems can result in excessive movement of the weighbridge deck, thereby magnifying these forces to a destructive level that can seriously affect the structural integrity of both the weighbridge and the foundations, not to mention the accuracy, as illustrated in figure 1.
In the case of the Shering weighbridge system, deck movement is restricted to 1mm in any direction using the company’s patented restraint post system. This system is mounted at the centre of the weighbridge for a very important reason — it compensates for the environmental temperature changes that radically alter the lengths of all weighbridge structures. Tackling this problem is a major factor in weighbridge design. For example, the restraint post system successfully overcomes all expansion and contraction issues by eliminating any need for end-restraint measures which create excessively large gaps and allow potential excessive movements as described above.
Lightning strikes also threaten a weighbridge system. Contrary to popular belief, it is not a direct strike (actually a very rare occurrence) that should concern weighbridge owners/operators, but a hit to a nearby object. When lightning strikes an object the power dissipates radially across the ground, similar to the effect seen when a stone is thrown into water. If a conductor is placed in the path of this power dissipation, extremely large eddy currents can be induced. It is these eddy currents that cause failures in weighbridge electronics and load-cells. Most weighbridge manufacturers include some kind of lightning protection in their designs, and the pros and cons of each type can be debated ad infinitum. When choosing a new weighbridge system, however, it is worth considering the manufacturer’s claims on lightning protection and the purchaser should not be worried about asking awkward questions. For example, if a manufacturer claims that load-cells are protected by bypassing them with earth straps, it is pertinent to ask how the earth strap bypasses the load-cell. This is only possible if the load-cell is isolated by an insulator of some kind. Similarly, if a manufacturer states that surge protection is fitted to absorb the energy of a lightning strike, the purchaser should ask how long it takes to react. In the instant before it reacts (and there will always be one) what happens to the equipment which is at that point, in effect, unprotected?
Weighing errors can also be due to cable damage caused by abrasion, water ingress or rodents. A good-quality weighbridge system should include comprehensive cable protection, such as Shering’s waterproof flexible conduit system. This helps prevent cable exposure, limits damage and adds an extra level of protection against water penetration in the load-cell junction boxes.
A quality weighbridge will successfully achieve the task of weighing goods, which is essential for many businesses. Today, however, weighbridge owners and operators can also reap the benefits of unmanned systems, state-of-the-art weighbridge software designed for individual needs, remote operation and integration into existing in-house systems. However, to protect any weighing system investment, it is vital that the technology behind the design of the weighbridge is understood. Armed with this knowledge, companies will be better equipped to purchase the right weighbridge for their needs and better able to maintain it appropriately.
This article was written by Kimberley Anderson, with technical contributions from Bob Matthews, Shering’s general manager (systems & electronics) and Chris Watt, general manager (engineering & design).
Shering Weighing Ltd, Pitreavie Business Park, Dunfermline, Fife KY11 8UL; tel: (01383) 621505; fax: (01383) 620262; email: sales@shering.com; website: www.shering.com