Truly Captivating
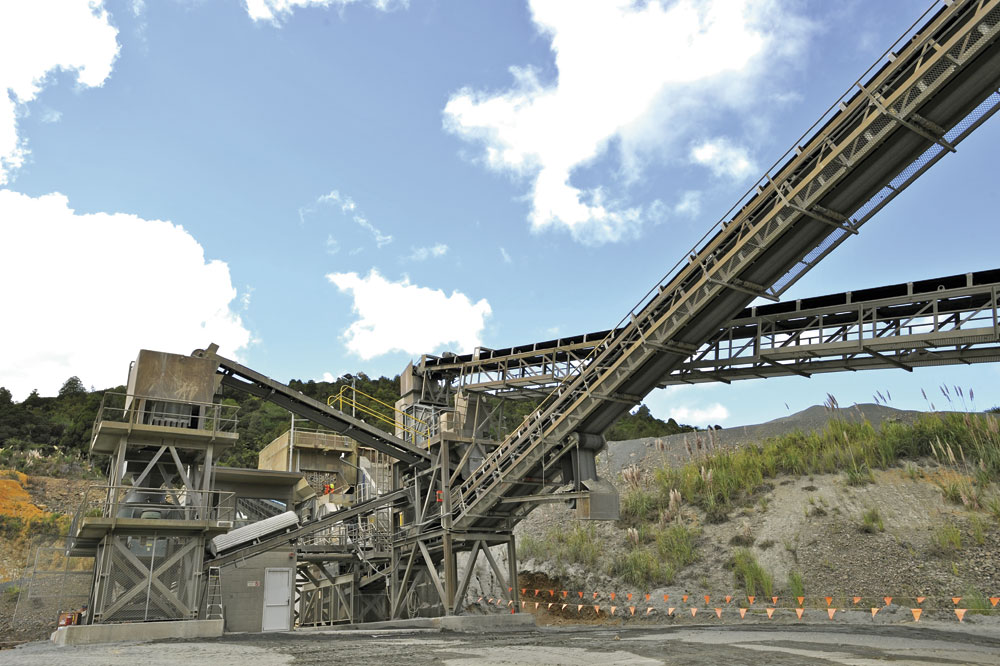
Having looked at the benefits for pit operations in the previous issue, Julian Athawes concludes his two-part review of Loadrite’s ‘Whole Site Solution’ for inventory tracking and process management by explaining how the technology links in with aggregate processing and load-out to help maximize cross-site efficiency and profitability
The Whole Site Solution provides a detailed and ‘joined-up’ view of inventory flow and volumes as material moves from the pit, through production, to load-out.
This new resource for the UK quarrying industry revolves around powerful software, the Material Management System (MMS). The program collates and analyses weighing, cycle time and associated data from high-accuracy scales on quarry equipment – excavators, conveyors, wheel loaders etc. Then, via a range of reporting options, it allows the quarry manager to assess actual on-site activity at every point, signalling where specific improvements can be made to reduce both short- and long-term operating costs.
Part 1 of this article looked at the benefits of Loadrite’s high-accuracy weighing and data reporting in the pit. By implementing similar inventory measuring systems in the conveying/production and load-out zones, data from all three zones can be integrated via the Whole Site Solution to extract maximum value in assessing site performance.
Crushing and conveying are the most expensive elements of a quarry operation. Capital and running costs relative to other quarry activities are high, taking into account the substantial plant infrastructure, depreciation and energy consumption involved, plus the replacement of crusher liners, belt scrapers and conveyor belting.
Processes need to run as efficiently as possible to protect profit margins. But efficiency can only be monitored and assessed by having accurate, comprehensive data on inventory and performance.
Intelligence
If data on inventory and output in the production zone is piecemeal and not particularly accurate, the quarry manager will be missing out on important intelligence.
Do you know what rating your crusher is running at, and whether it is hitting capacity? Is the haul sequence running efficiently? Can you identify bottlenecks before they happen? Are stoppages occurring that could be solved with more preventative maintenance? How much black belt time are you incurring?
These questions can only be answered through precise measurement and tracking of process volumes, together with versatile reporting to analyse parameters and performance.
Loadrite’s C-Weigh 1830 conveyor belt scale measures total production and machine utilization (crusher, screen etc), and provides stockpile tonnage by product. Data can be integrated with the MMS software to give live stockpile levels when linked with information from load-out operations.
This level of intelligence allows the operator to monitor flow rates against processing quality to arrive at optimized running levels, as well as tracking trends in residual capacity. Reporting will help quantify suspected inefficiencies and may expose ‘hidden’ issues that have been eating away unseen at profits.
Load-out
Measurement and tracking of materials also poses challenges in the final zone – load-out. Again, Loadrite have developed high-accuracy weighing technology and data capture to track the journey of inventory from the conveyor to the weighbridge.
Loadrite L-series scales for wheel loaders achieve sub-1% accuracy deviation. The L-2180 offers ±0.5%, making it the most accurate system of its type on the market.
The technology uses two proprietary systems: Loadrite’s MDC (Multi-Dimensional Compensation) weighing and FACT (Friction & Ambient Compensation Technology). These combine to give fully dynamic, high-accuracy weighing that adjusts throughout the day to environmental and machine changes to give truly consistent performance at high output levels.
Maintaining the highest possible accuracy in load-out operations will prevent fails at the weighbridge, reduce cycle times and maximize shipment rates. Customers and in-house fleets gain from fast truck turn-around times, reduced queues and the virtual elimination of unloading, reloading and re-weighing.
Efficient loading also saves costs by avoiding overload fines, reducing wear and tear on trucks and wheel loaders, and preventing trucks leaving with void space on-board.
Onboard software captures a range of vital data on the machine’s activities, including the product type in each load linked to the truck that received it.
Multiple
For larger sites with multiple loaders, the Load-Out Management System (LMS) offers a traffic-control and loading solution to facilitate communication between loader operators and the quarry’s scale house ticketing system.
This offers real-time visibility of load-out operations to improve productivity. The plant operator uses in-cab information to optimize load-out, reducing the amount of time customers’ trucks spend on the yard. The system will track products sold, time on yard and loader efficiency.
It adds yet another valuable layer of management data to the Whole Site Solution. While helping to sharpen the stand-alone efficiency of load-out activities, data can also be cross-referred with outcomes from the processing zone to identify if production volumes can be better matched to load-out needs.
With high-accuracy measurement and data capture in all three zones, Loadrite’s MMS ‘Whole Site’ software can now merge information to give an unprecedented view of site ‘connectivity’ and efficiency.
Traditionally, quarries have tended to examine efficiency at isolated points of their operations. But key performance indicators (KPIs) in quarrying are now closing the ‘information gap’ between processes. The Whole Site Solution is a timely, tailor-made innovation that can assist the industry’s move to a more ‘joined-up’ approach.
Having accurate data on production volumes and cycle times can be a revelation. By analysing long-term data on production volumes and materials shipping, an operator might find, for example, that output should be lowered. Significant savings could be made by rationalizing pit output to suit an optimized production level based on intelligence from the Whole Site Solution.
By spotting bottlenecks and other issues, the technology may lead to dramatic improvements, such as a hike in productivity. It will also reveal opportunities to add value in many other areas, such as lowering operating costs by permitting better fuel efficiency.
Compatibility
Loadrite have designed their scales and software for compatibility with many types of new or existing plant. In most cases, the weighing systems integrate with equipment without the need for personnel to modify operating procedures.
The Whole Site Solution can be cost-effective for different sizes and types of extractive operation, whether turning out 30,000 or 30 million tonnes of product per year. Weighing and data-management systems can also be built bit by bit and refined as the business grows.
Through more accurate weighing of inventory, reduced cycle times and improved data capture, this technology offers a final important advantage in the current era of sustainable operation and carbon reduction. Quarry operators can reduce fuel consumption and quantify the savings.
University researchers carried out a study at a New Zealand quarry using Loadrite weighing systems to optimize road truck loading. It was estimated that 700,000MJ of non-renewable energy consumption and 52 tonnes of CO2-equivalent greenhouse gas emissions were avoided for each loader that had a weighing system installed.
Loadrite’s Whole Site Solution provides the seamless tracking of inventory that the quarrying industry has long needed, to enhance its efficiency, cost control and environmental performance.
The author, Julian Athawes, is managing director of Halomec Ltd, UK distributors of Loadrite weighing solutions. For further information on the technologies featured above visit: www.wholesitesolution.com. Alternatively, see them in action at the CETA demonstration days at Uttoxeter Racecourse from 15–16 June 2011. Visit www.cetauk.org for further details.