Smart-Weigh
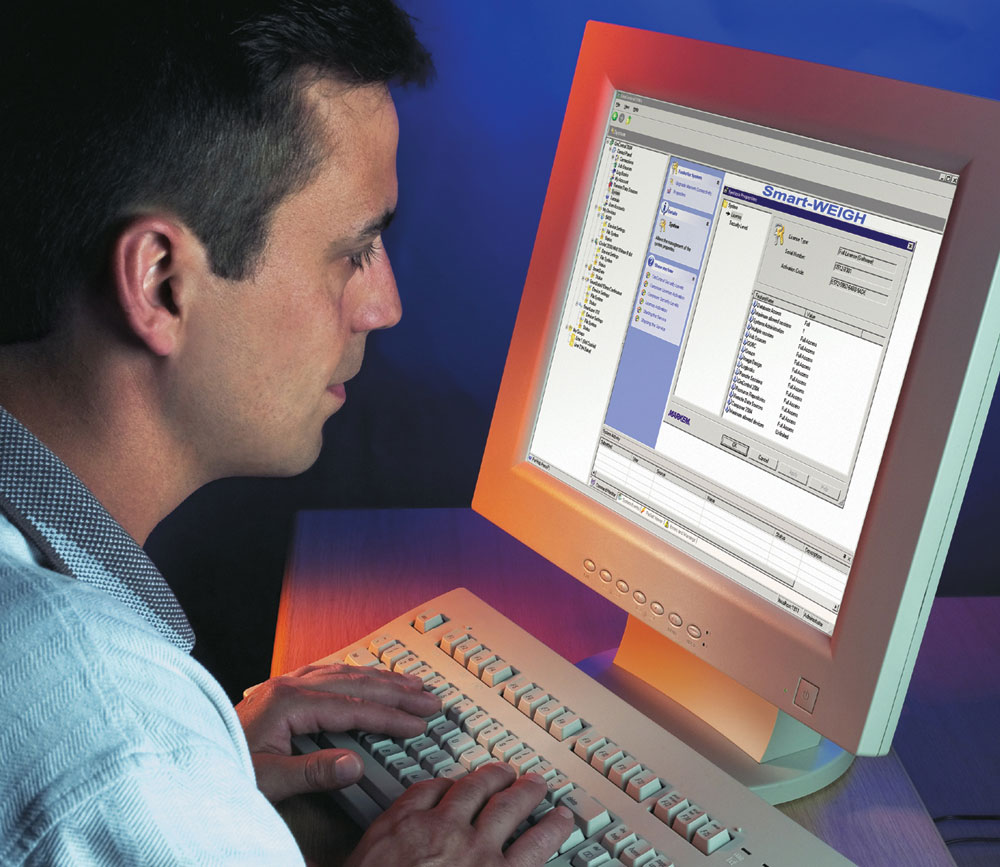
New technology ensures vital weighing data is used to its best advantage
Weighing is at the heart of most quarrying and recycling operations, with equipment as diverse as weighbridges, axle weighers, hopper scales, fork-lift truck weighers and silo weighing systems. In many operations, weighing systems such as weighbridges act as critical control points, providing valuable data and control functionality for vehicles entering and leaving sites. However, collecting and integrating the weight data into existing management systems has traditionally involved a significant amount of paperwork and manual data entry. As a result, most current installations do not make best use of this valuable asset, while in parallel, product diversification further complicates data reconciliation.
Industrial weighing specialists Weightron Bilanciai have recognized that weighing equipment, while vitally important, is really only a ‘means to an end’, and they have already pioneered the integration of complementary modern technologies with their products to provide better use/management of weighing data. Now the company say they are confident that their latest innovation, Smart-Weigh, will bring a new dimension to weighing and set new standards for system versatility and integration. Although this development can be used with virtually any weighing system, it is expected that one of its main applications will be for weighbridges.
Smart-Weigh – the chameleonic solution for modern weighing
Weightron’s sales director, Nick Catt, believes Smart-Weigh is the most significant development in weighing technology over the past decade, as he explains: ‘Today’s operators need fast, reliable information but do not want to have to concern themselves with how it is collected and distributed. Quarries and recycling plants often operate a range of weighbridges from different manufacturers, making site-wide integration difficult enough, let alone trying to co-ordinate nationwide operations.
‘We can now offer multiple weighbridge users a cost-effective, unified digital solution for their different analogue weighbridges. Historically, weighing-based software packages have tended to be application specific, leaving little scope for modification and further complicating harmonization. Smart-Weigh is a unique blend of software and hardware, providing a cost-effective and versatile solution for operators, irrespective of the weighbridge type or make.’
Smart-Weigh is the result of extensive experience in weighbridge operation together with customer feedback from a broad spectrum of industries. Essentially it consists of two main elements. At the ‘ground level’, a high-performance Weights and Measures-approved digital ‘black box’ converts any analogue weighbridge into a fully digital system, where each load-cell output is individually monitored and measured. Digital weighing systems bring significant advantages for both users and suppliers in terms of operational and maintenance benefits. Connectivity from the weighbridge is via a bi-directional serial link to a weight indicator fitted with an Ethernet communications card. The weight indicator is not part of the ‘approved’ measurement chain and can therefore be changed or modified without the need to re-verify the system.
At ‘management level’ the Weightron Connect universal software package provides optimum flexibility, user-friendliness and security. Depending on the available network (LAN or WAN), the software can reside on a local or remote PC and each weighbridge can be allocated its own dedicated IP address. The software is configured so that operators communicate with the IP addresses of the particular weighbridges via a standard web browser and weighing operations from up to four different scales can be viewed on screen at any one time. Approved administrators can handle full file maintenance including, for instance, the validation of smart cards for driver-operated weighbridges. This is particularly useful when new cards need to be issued for delivery or collection vehicles and removes the need to visit sites to program in the details.
Transaction data is stored securely on the weight indicator and then uploaded to the designated PC at predetermined intervals via the network connection. The format of the data can be set for specific applications and comprehensive internal checks ensure that all the data strings are valid. These strings can be made available at designated locations on a network so that systems such as SAP or SAGE can access them. The effective collection of the weight data brings another bonus by keeping secure records of key operator actions to provide a permanent record of who did what, where and when. This can help identify problems that may have been inadvertently caused by ‘operator misadventure’.
When is a weighbridge not a weighbridge? When it’s a Smart-Weigh axle weigher
In addition to improved data management, the digital benefits introduced by Smart-Weigh can be effectively used to convert a standard analogue pit weighbridge into a dynamic axle weigher at the touch of a button.
Overloaded axles cause major damage to roads and resulting fines can be very onerous for operators. In many applications the high-accuracy weighing of all vehicles going over a particular weighbridge is not necessary; the operator may simply want to check if the vehicle is overloaded. Carrying out static weighing on every vehicle in this situation can lead to unwanted delays and bottlenecks. In addition, measuring the total weight of a vehicle does not always detect individual overloaded axles, while fitting supplementary dedicated axle weighers to check vehicles is a relatively expensive exercise.
Unlike competitive products which require vehicles to be positioned statically at two different places on the weighbridge, the Weightron solution can weigh vehicles at speeds up to 5km/h and has a number of built-in features to optimize the weighing procedure. If the approach–departure surfaces are sufficiently level, individual axle weights can be measured within to ±1%.
Depending on how the operator wants to weigh the vehicle, the system is set to either standard or dynamic weighing. In dynamic mode, as the vehicle drives on to the weighbridge the system measures and records the first axle weight. When the second axle comes on to the deck the system automatically subtracts the first axle weight from the new weight reading to give the second axle weight. This procedure continues until all the axles have been individually weighed and recorded.
As soon an overloaded axle is detected, a signal is generated which can be used to trigger an audio or visual alarm. If drivers try to cheat by driving a wheel over the edge of the weighbridge, the system automatically detects the corresponding weight change and initiates an alarm.
Sign of the times
In another technological breakthrough, Weightron Bilanciai claim to be the first UK weighbridge manufacturer to offer electronic signature-pad capabilities for their driver-operated weighbridge systems. The robust pads are fully compatible with Smart-Weigh and can either be integrated into the Weightron Self Box terminal or, for manned installations, located in the weighbridge office. The electronic signatures act as a permanent record for each weighing and the signatures can be printed on paper receipts and also displayed on the local or central PC.
The specific weighing procedure determines where the pads are located and drivers may be required to sign to gain entry to and/or exit from any particular weighbridge. The signing process gives added security and traceability to the weighing process, while triggering an output to control traffic lights or barriers.
Keeping the wheels of industry turning
In addition to important operational and managerial benefits, Smart-Weigh provides a powerful system diagnostic capability, which allows the supplier to remotely keep a constant check on the health of any weighbridge. This takes the burden of responsibility away from users, who can then concentrate on maintaining their businesses’ profitability. The system can record critical operational parameters, including instances when the weighbridge is overloaded. Problems with individual load-cells are automatically flagged up with email or text messages sent to designated recipients. Engineers can access the system to check on other critical parameters and, in many cases, resolve system malfunctions remotely. If there are more serious problems engineers can ensure that when they go on site they know what the problem is and have exactly the right spares, thereby ensuring a ‘one-time fix’ with minimum plant disruption.
For further information contact Weightron Bilanciai Ltd on tel: (01246) 260062; fax: (01246) 260844; email: sales@weightroncb.co.uk