Precia-Molen Help Improve Traffic Flow And Loading At Tunstead
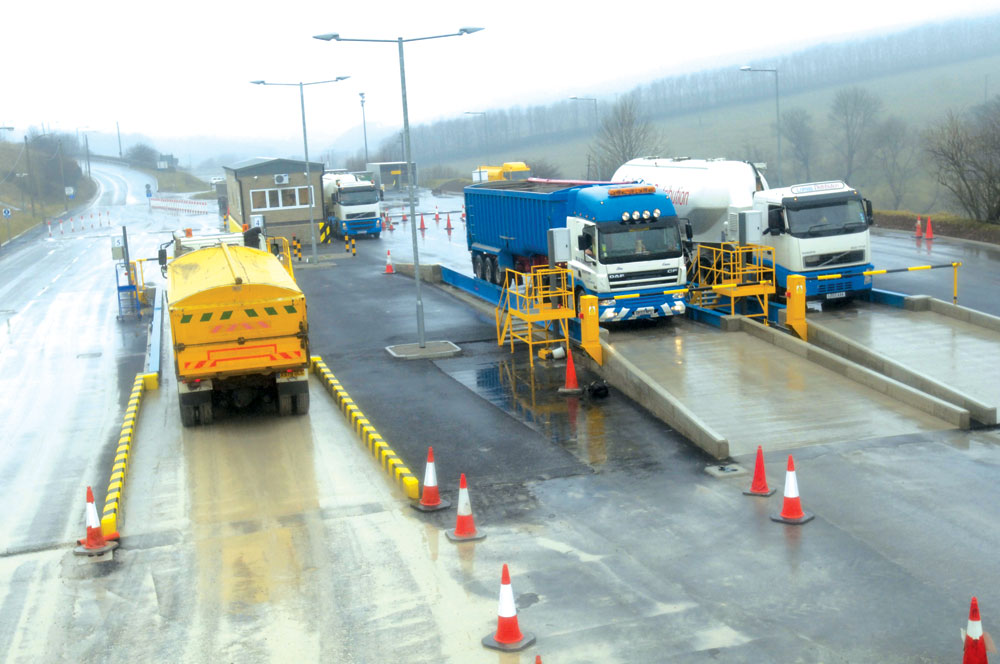
A weighing and loading management system at Tarmac’s Tunstead Quarry, in Derbyshire, is helping to move 6 million tonnes of aggregate products a year. Every day more than 650 vehicles, including rail wagons, transport products such as cement, lime, chemical stone and concrete, in and out of the site.
As one of the busiest quarries in the UK, Tarmac needed an integrated weighing, automated cement loading and traffic-management system in place that would interface with their SAP system to meet the diverse operational needs of the quarry.
Following a vendor assessment, Precia-Molen were approached by the quarry operators to design and build a system based on the widely regarded GeneSYS and GSM software.
The on-site weighing and load-management solution had to seamlessly integrate with the driver self-loading remote cement dispatch depots, which handle more than 250,000 dispatches a year. Replacing two existing dispatch units, the system also needed to provide fast and accurate management reporting to monitor the site’s performance and efficiency.
Precia-Molen came up with a flexible solution by developing a bespoke weighbridge-management system that encompasses the entire traffic operations at Tunstead. Utilizing the benefits of GeneSYS, the system has helped Tarmac combine the operation of eight weighbridges, two batch weighers for rail wagon loading and a total of 18 driver consoles, which provide fully automated dispatch activities across the site.
As part of the installation project, Precia-Molen have added a new weighbridge entrance comprising three weighbridges, each equipped with a driver console, traffic barriers and traffic lights.
To achieve seamless operation from ordering to invoicing, the GeneSYS software is fully integrated with Tarmac’s own sales order management system. When an order is placed, it is entered into the sales system and matched against quotes set up in SAP. The order is then imported by the GeneSYS system for collection or dispatch.
Lorries visiting the site are pre-issued with RFID cards for identification. On arrival, the vehicle is driven on to the weighbridge and the driver presents the RFID card to the cab-height driver console and enters an order number.
GeneSYS weighs the vehicles and, if the tare weight is within expected tolerance, a loading slip is issued. Data for each truck is also permanently kept by the system, offering faster verification and entry to the site.
If the vehicle is new to the site, the driver reports to the weighbridge operator, who inputs the registration details and order number. The lorry is then weighed, issued with a loading slip and single-use RFID card, and proceeds to the loading areas.
For bulk loading, the driver enters one of the numerous driver-operated loading points, which feature automated loading. GeneSYS then verifies the vehicle is at the correct location and signals the start of the loading operation, via the integrated PLC.
For vehicles being directed to the aggregates stockpile area, the order details are sent to the loading shovel through a telemetric link, where the operator verifies that the vehicle is to be loaded with the correct product and tonnage. Once loading is complete, the lorry proceeds to the check weighbridge where the order weight is checked against the loaded weight and, if it is within tolerance, the vehicle is directed to the exit weighbridge.
For bagged cement or lime products, drivers simply present their loading slips to an operator. When loading is done, confirmation is entered into the GeneSYS system and the driver proceeds to the exit weighbridge. All vehicles transporting aggregate products have to return to the exit weighbridge to receive dispatch documentation.
Meanwhile, cement and aggregate rail loading is managed by two Precia-Molen batch weighers, with loading details entered into the GeneSYS for integration into the site’s other operations. This configuration provides operation of rail-fed remote driver self-loading dispatch depots, reducing road vehicle movements, say Precia-Molen, by up to 70 a day.
The company has also built in system resilience and data replications, allowing remote dispatch depots to continue operation should communication failure occur.
Overall, Precia-Molen have provided a powerful and flexible on-site weighing and load-management system that has met the needs of this busy and diverse quarry operation. It is one of the most advanced automated loading systems in Europe, and with the integration of new remote dispatch depots in the West Midlands, Yorkshire and London, Tarmac have been able to expand into these market areas.
Nick Thomas, distribution manager for Tarmac Buxton Lime and Cement, said: ‘Tunstead now has a single system that encompasses the cement, lime, concrete, aggregate and chemical stone operations, ensuring fast and efficient throughput for high volumes of road and rail traffic.
‘We have a sophisticated management system that is fully integrated with Tarmac’s own SAP sales order and site systems. The GeneSYS-based solution, in particular, has created a stable and expandable platform for the management of the entire site, doubling weighbridge operator capacity and providing important performance and traffic information.’