Integrated Technologies
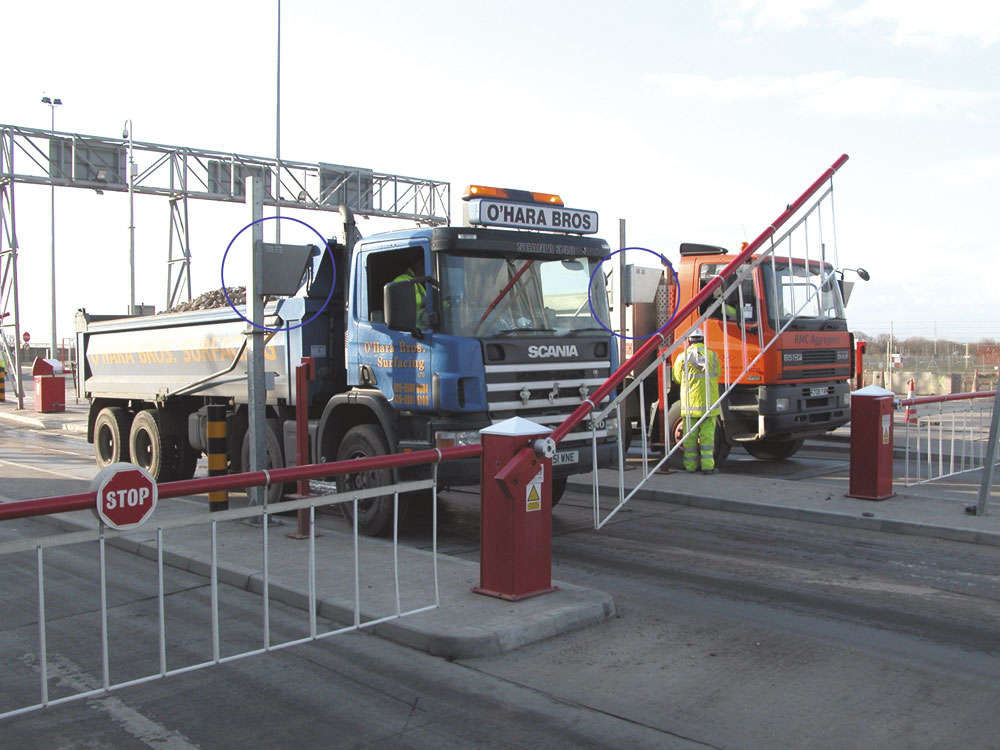
The integration of new and diverse technologies with traditional weighbridges is playing a growing part in system improvement across a broad spectrum of industries. Weightron Bilanciai’s sales director, Nick Catt, believes these advances are set to bring cost-effective improvements to the changing and challenging world of mining and quarrying
Weighbridges play a crucial role at quarries, mines and mineral-processing plants, providing critical data for a wide range of activities, including the weighing of incoming and outgoing raw materials and finished products. They also provide essential safety information ensuring vehicles do not cause unnecessary damage to roads through overloading.
Traditionally, the weighing process in many weighbridge applications has been relatively slow and data collection has been confined to local printouts of tickets and daily tally rolls. Now more emphasis is being placed on developing key peripheral areas. This is aimed at speeding up throughput of vehicles, improving security and extending weighbridge operational periods, together with improving and simplifying data collection and distribution. Technologies employed include Ethernet communication for remote access, automatic vehicle-recognition systems, smart card or key readers, wireless interfacing, the worldwide web and GSM (global system for mobile communications — the second generation of digital technology originally developed for Europe but which now has in excess of 70% of the world market. GSM originally stood for Groupe Speciale Mobile). Bespoke, yet configurable, software packages can now be tailored for specific applications and are designed for seamless integration with existing management systems.
In parallel with these developments, the advent of predictive-maintenance programs is minimizing breakdowns and reducing service call outs. However, although most of the recent innovations focus on peripheral equipment and system integration, companies such as Weightron Bilanciai have also invested considerable time and effort to improve the design and structure of the weighbridges themselves. At first sight there appears to be little scope for improvement, but the company has found innovative ways to reduce costs without compromising strength and reliability. Modular construction techniques have significantly reduced production lead times, while the use of robotic welding and new surface-finishing technology ensures improved longevity. In addition, improvements in load-cell technology and instrumentation offer further enhancements. Digital load-cells are now becoming well established in weighbridge applications and offer a number of advantages over analogue load-cells, especially during installation and ongoing servicing.
Vehicle recognition
Vehicle-recognition systems are effective in increasing vehicle throughput at weighbridges while introducing an effective security system. They are particularly effective at remote sites and at sites where ‘out-of-hours’ weighing is required, and are increasingly being used in conjunction with driver-operated systems using smart cards or keys. These can be programmed to contain additional relevant information about the vehicle and its particular load. Recognition technologies employed include automatic number plate recognition systems using cameras and those that rely on the vehicles being fitted with transponders containing key vehicle details.
In a typical system where automatic or remote weighing is carried out, the weighbridges usually have entry and exit barriers. Vehicles approaching the entrance are picked up by the camera and the number plate is checked against the database. If the vehicle is registered it is allowed through the first barrier on to the bridge to be weighed. At this point the driver inserts his card or key at the control terminal positioned outside the vehicle window and this initiates the weighing. The database can be programmed to contain complete details of the vehicle, including tare weight, and this information can be used for printing weight tickets and invoices. Simple command prompts guide the driver through the weighing process and as soon as the weighing has been successfully carried out, the vehicle is allowed off the weighbridge. If the vehicle is blacklisted, it is not allowed beyond the first barrier and a variety of alarms can be initiated. The whole process is carried out in reverse when the vehicle leaves.
Such systems can also maintain a current and historical record of vehicles on site, allowing a comprehensive vehicle movement log to be maintained at both single and multiple sites. Overhead security cameras can even be used to take images of the contents of the vehicles as they are entering or leaving the weighbridge. Integrated message boards linked to the system can further help avoid congestion on busy sites by giving instructions to drivers.
Driver-operated systems
The use of driver-operated weighbridges offers significant benefits for operators both from a cost and efficiency standpoint. Such weighbridges typically have two main modes of operation, single weighing and double weighing.
For vehicles not registered in the database for a particular site, the driver stops the vehicle on the weighbridge, swipes the card, and the terminal issues a ticket with the inbound weight data. After loading or unloading has taken place, the driver returns to the weighbridge and, having swiped the card again, receives a ticket automatically calculating the weight of material delivered or collected.
In the single weighing mode, when a card for a known vehicle is swiped, the terminal retrieves previously stored data relating to that vehicle’s registration number and tare weight. Using this information, the terminal then issues a ticket showing the calculated net weight of material being delivered or collected, thereby removing the need for a second weighing.
Effective weight data collection
Weighbridge instrumentation has advanced in leaps and bounds over the past five years. Improvements in flexibility and ease of operator use have been matched with improvements in data collection and distribution.
One criticism levelled at suppliers in the past has been the ‘closed’ nature of their software architecture. Even basic changes required relatively costly upgrades to firmware or even hardware. Today more user-friendly systems are emerging where a wide range of set-up and operational configurations can be implemented remotely, either by the user or by the supplier via standard web browsers. The ability to configure weighing screens, databases and other key operational processes is invaluable and allows systems to be expanded and modified as and when required.
Remote access to weighing systems offers a number of clear benefits for both the supplier and the user. This can be achieved via Ethernet connections using standard telephone lines or, where applicable, GSM. Integration is now allowing the gap to be bridged between the weighing system and users’ management systems. Weighbridge applications at single and multiple sites can be linked to a centralized location, which may even be in another country.
Predictive maintenance
Weighbridges are essential to many processing operations and unwanted breakdowns can be costly and very inconvenient. Although regular servicing and maintenance can help to minimize problems, predicting what and when things will go wrong is very difficult with weighbridges fitted with traditional instrumentation and analogue load-cells. The advent of digital load-cells has brought a number of advantages, especially during installation and ongoing servicing, allowing the status of individual cells to be checked remotely. The combination of this technology with the new generation of instrumentation provides the platform for remote maintenance service systems, which can save considerable time and effort, especially for equipment operating in harsh, remote areas.
With such a system installed, any problems or unusual trends within the weighing equipment are automatically flagged up at the weighbridge supplier. Details can then be immediately forwarded to the local engineer who can dial into the weighing system remotely and make a risk assessment of the situation. In many cases the engineer can carry out a range of checks and rectify the problem without having to visit the site. Where appropriate, a temporary repair may be instigated, allowing plans to be made to carry out full remedial work at a time convenient for the operator.
Conclusion
Weighbridges are an essential part of a diverse range of mining and quarrying processes and they can offer far more than just weight information. A blend of sound mechanical practice and modern technologies is offering companies a range of benefits and it is expected that further system integration will continue to bring increased benefits to both users and suppliers.