Avoiding The VIPER
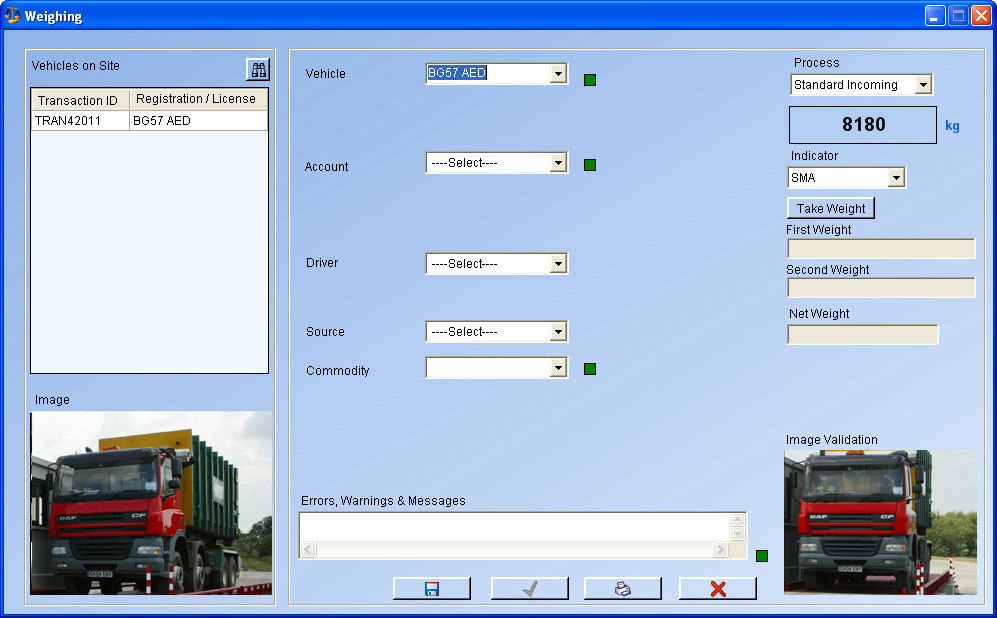
The use of new technology called VIPER means that VOSA is cracking down on overloaded and unevenly loaded vehicles. To take action, the quarrying industry needs accurate and reliable weighing solutions, argues Chris McAllister, market manager for Avery Weigh-Tronix
VOSA (Vehicle & Operator Services Agency) states that both overloading and uneven weight distribution continue to be two of the most frequent offences for HGVs, ranking alongside tachograph and drivers’ hours offences. It is a serious health and safety issue because it increases braking distances in an emergency and makes the vehicle more difficult to control.
Virtually all quarries will have at least one weighbridge, so gross overloading should not be an issue. There have, however, been several prosecutions for overloaded axles due to poor weight distribution.
With the rising cost of transportation, most vehicles will be loaded as close as possible to their maximum weight. This means that if product is unevenly loaded there is little or no margin for error for even weight distribution, and the chances are that individual axles will be overloaded, especially when taking into consideration the fact that some products do not flow well.
According to the Road Traffic Act, overloading a vehicle in any way is an absolute offence. This means that an offence is committed even when the driver or operator had no knowledge of the overloading. It is important to ensure that the driver has the cargo weight confirmed in writing and that information is printed on the weight bill, as this can be used as evidence in mitigation.
If a vehicle is stopped and directed to a weighing site and is then found to be overweight, the driver and any other person who permits the use of the vehicle may be liable for prosecution.
In addition, the authorized officer will issue a prohibition notice making it illegal for the vehicle to travel on the road. This notice must be cleared in writing before the vehicle can proceed, and it is up to the operator to meet the costs of offloading the excess weight safely.
The penalties for overloading can be severe. There is a maximum fine of £5,000 per offence, ie per axle, per gross and per train overload, and the driver can also have his or her licence disqualified. Convictions can also affect the decision of the Traffic Commissioner to suspend, revoke or renew an HGV driver’s licence.
In the past enforcement may have been an issue. The only solution was to have random checks at fixed sites with police officers stopping vehicles. Once word got out, many vehicles could easily avoid inspection sites. In 2003/04, for example, VOSA weighed 41,731 UK and foreign vehicles with a prohibition rate of 7.84%.
Beware the VIPER
Now, however, VOSA is using new technology and has new powers to make enforcement more effective.
In 2004 it gained the power to stop vehicles itself, following accreditation from chief officers, and the police have now trained a number of VOSA staff who can operate in specially marked cars. Since that time there have been significant increases in the number of vehicles stopped and prohibitions issued.
More recently the organization has started using VIPER, a system that combines weighing-in-motion sensors (WIMS) and automatic number plate recognition (ANPR).
As vehicles drive over the sensors, each individual axle is weighed, while the system classifies the vehicle type. The system then calculates the totals of the individual axles to a vehicle’s gross weight and compares this information to pre-programmed parameters of both axle and gross vehicle weights. The ANPR system records the number plates of any vehicles that are in any way overloaded.
A recent pilot study recorded a 700% increase in identifying and prohibiting overweight vehicles. In this study the system identified 434 vehicles as being overweight. These vehicles were stopped and 379 were found to be actually overweight. A total of 344 weight prohibition notices were issued. Since then, road checks between February and April were 100% effective and only non-compliant operators were stopped.
Such was its success that VIPER won the Intelligent Transport Society’s technology award for excellence. There are now four sites operating with another 10 to be added by April 2008. Negotiations are ongoing for further sites.
Weighing-up a solution
With tight margins and fuel prices increasing, most quarries and transport operators will load as close as they can to the legal limit. Most also understand the need to load their vehicles evenly, but in practice this can be hard to check.
While it is possible to check weight distribution on a weighbridge by weighing the total load and then driving partially off to check the weight distribution, in a busy quarry there is rarely the time or inclination to do so.
To check for even weight distribution the best option is to install on-board weighing. Not only does this weigh the gross load but it can also show how the weight is distributed.
Unfortunately, in the past some systems proved unreliable, which is not surprising considering where they are installed – both the load-cells and the cabling are underneath the vehicle and, therefore, subjected to mud, water and debris being kicked up by the wheels.
The good news is that the technology is getting better and there are now more reliable and accurate systems on the market.
So, if you are specifying on-board weighing, what should you ask the supplier?
Chris Hodge of Commercial Motor magazine has some recommendations. He suggests asking: ‘Can it be tailored to suit an individual vehicle or operation? Can it be transferred from one truck to another? Is it accurate to within 50kg? Is it simple to operate? Is it robust and reliable? Does the system come with a tailor-made warranty? Is it quick and easy to install? Does the system come with nationwide aftersales and service back-up?’
He finishes off the list by questioning whether the system allows drivers to load safely and if it helps ensure that they are not losing money by under-loading.
In addition to this list, it is suggested that you ask for references and proof points. For example, how many technicians are in my local area? How quickly can they get to me – time off the road is money lost. And can simple repairs be done at the roadside?
One recent advance that makes such systems inherently more reliable is the introduction of digital load-cell technology. This is not a new technology for weighbridges and other applications, but it is new for on-board weighing.
Using digital load-cells halves the number of wires in the chassis cable from four to two. It also reduces the amount of cable needed, eliminates any need for a junction box and minimizes the number of chassis cable contacts. Put simply, there is less to go wrong.
In addition, reliability is better because the temporary presence of moisture in the connectors will not affect digital data transmission. In an analogue system this would stop it working.
While weighbridges ensure that gross overloading of a vehicle is rare for quarry traffic, it is still important to make sure that the load is evenly spread. Weight distribution can be an issue, as many products do not flow evenly, if at all.
As operators push the maximum legal loading on the vehicles the margin for error on individual axle loadings becomes finer, and the chances are that VOSA will now catch those who transgress. Unfortunately, even genuine errors are not a defence in law. So beware the VIPER and make the most of current technology to stay legal.