Waste Not, Want Not
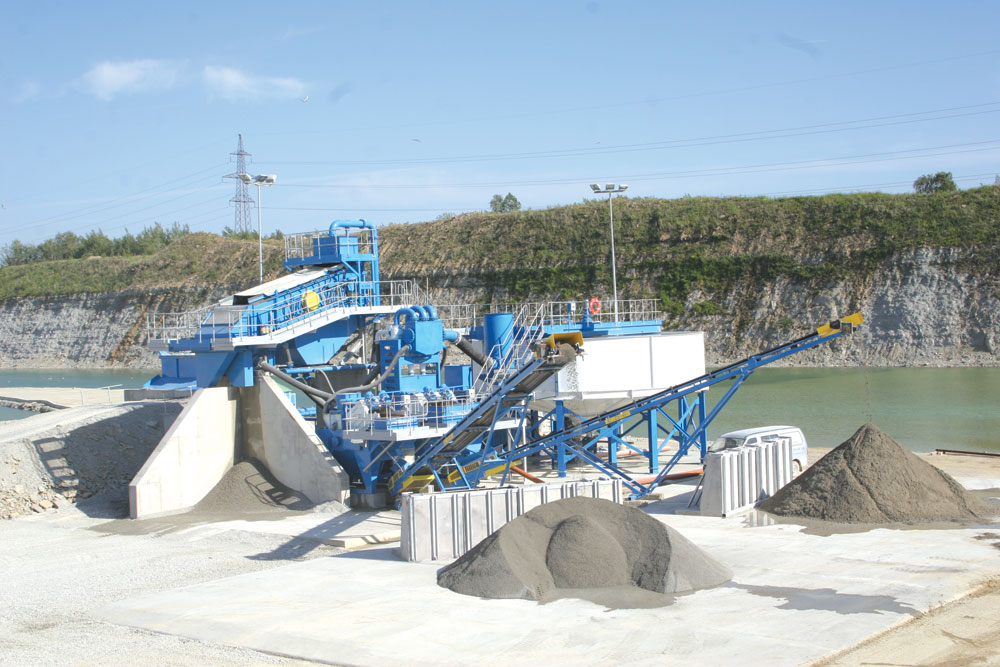
New CDE sand washing plant produces high-quality building materials from 50-year-old waste in Estonia’s capital, Talinn
Estonian company Paekivitoodete Tehase (Limestone Products) have recently purchased a CDE sand washing plant to process a material that had previously been stockpiled as waste because of its high clay content. As a result, this same material is now being sold to the Estonian building materials market as high-quality, fully certified sand and aggregate.
The urban location of the new plant, which is situated in Estonia’s capital, Talinn, required the plant supplier’s proposal to contain a detailed environmental impact statement dealing with issues such as noise pollution and other site conditions likely to have an impact on residents in close proximity to the site. CDE compiled a detailed report for the Estonian planners and, with all the information provided having received their approval, planning permission was duly granted.
Paekivitoodete Tehase are Estonia’s leading producers of crushed limestone products and operate several sites in the Talinn area. The new CDE plant is installed at their Vao Quarry, which has been in operation for around half a century. The materials produced by the company are used extensively in Estonia’s burgeoning construction market.
Since they were founded Paekivitoodete Tehase have developed a reputation for innovation. ‘We are seen as leaders in Estonia with regard to bringing new technologies and processes to the market,’ commented company chairman Vladimir Libman. ‘The introduction of this CDE washing plant is yet another example of how we approach business. These technologies have never been used before in Estonia and we are delighted to be the first company to use them.’
The project is the first contract that CDE have won in the region through their Estonian distributors Baltem, who also represent the Northern Ireland-based company in the neighbouring countries of Latvia and Lithuania.
‘We are delighted to be working with Baltem in this region,’ said CDE’s European sales manager, Eoin Heron, who was responsible for delivering the Talinn project. ‘Through their representation of Komatsu in Estonia, they have established a reputation as a company that delivers…and we are very pleased to be working with them, not only on this project, but also a number of other significant projects in the region.’
The new CDE washing plant has been acquired specifically to deal with material that has been stockpiled as waste since Vao Quarry began production some 50 years ago. The material is a by-product of the site’s crushing processes and, until now, Paekivitoodete Tehase had been unable to find a system capable of processing it to produce commercially viable products in a cost-effective manner.
However, rather than giving up on their search and simply dumping the waste material, the company continued to seek a solution and their persistence eventually paid off when they made contact with CDE at the UK’s biennial Hillhead quarry show in June 2007.
‘The problem that Paekivitoodete Tehase had was that the material they were stockpiling was very dirty with a high clay content,’ explained Eoin Heron. ‘We were able to show them that we have a considerable amount of experience in working with difficult materials, such as the one they were having a problem with.’
After several site visits in the UK and Ireland, where similar problems had been encountered, and following much deliberation between the customer and CDE’s technical design team, a deal was eventually concluded for a 150 tonnes/h CDE washing plant capable of handling –40mm material.
New plant
The washing plant commences with a 20-tonne feed hopper, which discharges into the latest addition to the CDE product line-up, the AtroFeed. This unit utilizes a very-high-pressure jet of water, which, at the point of impact with the clay-bound feed material, provides enough attrition to remove the clay. Following this stage, the material is fed directly to a ProGrade R2M108 (1.8m x 6.0m) double-deck rinsing screen, where the material is washed and sized into +16mm, –16 +5mm and –5mm materials, with the two coarser fractions being discharged into concrete stockpile bays beneath the screen.
The project marks the first commercial use of CDE’s AtroFeed system, as Mr Heron explained. ‘Given the clay-bound nature of the feed material and the individual characteristics of this project, the AtroFeed was the ideal product,’ he said. ‘The material is delivered to the AtroFeed directly from the feed hopper and from here it is transferred directly to the screening station. One of the many advantages the system provides is that it eliminates the need for a transfer conveyor from the hopper to the screening station. The feed material, mixed with the water from the high-pressure jet, is piped to the screen, thus reducing the space required for an installation such as this.’
Meanwhile, the –5mm material from the ProGrade screen is sent to a heavily customized dual-sands plant from CDE’s EvoWash range. Here, the –5mm +2mm grit is rinsed again and dewatered before being stockpiled, while the –2mm material is fed through CDE hydrocyclones, which remove the unwanted –63 micron material, and on to another dewatering screen. The clean –2mm +63 micron sand is stockpiled, while the waste water and –63 micron material are sent to a CDE AquaCycle T08 thickener.
The washing of the –5mm material on this project required a substantial amount of customization of the CDE equipment due to the high percentage of clay in the feed material, as Mr Heron explained. ‘With the amount of clay that we had in the feed, it was clear that, at the sand washing stage, further washing would be required. The result of this is a second washing screen for all the –5mm material. This ensured that we were able to get the material clean enough to be commercially viable.’
According to CDE, it is the high level of customization in the plant that has allowed Paekivitoodete Tehase to process this waste material into commercially viable products. ‘The fact that this material has been here for 50 years is evidence that it could not be processed by an off-the-shelf product,’ commented CDE’s sales director, Enda Ivanoff. ‘Only through a system built specifically to deal with the individual characteristics of this project, were we able to solve the problem for Paekivitoodete Tehase.’
Also key to the project from its very earliest stages were the environmental considerations demanded by the planners. These required a degree of water treatment and recycling to minimize the environmental impact of the operation – an area where CDE have gained significant experience in recent years having supplied many international projects with systems that incorporate complete closed-circuit water treatment, such as their AquaCycle thickeners and filter presses.
Following the sand washing phase, the waste water and –63 micron material are sent to the AquaCycle T08 thickener. On entering the thickener, the waste sludge is automatically dosed with a small amount of polyelectrolyte flocculant, which forces the silts and clays to settle to the bottom of the tank. Rotating rakes fitted at the bottom of the tank move the thickened sludge towards the centre of the tank, whereupon it is discharged and pumped to the on-site settling ponds. The rotating rakes send signals back to the PLC control panel regarding the amount of resistance being encountered, causing the sludge pump to start and stop automatically, as required.
Meanwhile, the clean water that overflows the top of the thickener tank is recycled back to the washing plant. This significantly reduces the amount of water used in the washing process, which, in turn, reduces not only the environmental impact of the plant, but also its running costs.
‘This project, more than any other, provides support to our often stated belief that providing off-the-shelf products is simply not an efficient way to deliver systems to this industry,’ said Mr Ivanoff. ‘Each project has its own individual characteristics in relation to feed material and output requirements that necessitate an individual approach.’
At the official opening of the plant in June 2008, Paekivitoodete Tehase’s chairman, Vladimir Libman, commented: ‘Our company has developed a reputation for innovation which has been the foundation of our success in recent years. The introduction of CDE’s technologies to Estonia is the latest example of our commitment to the development of our business through the adoption of the best systems available to us.’
For further information on this or other CDE projects, contact the company via email: info@cdeglobal.com or tel: (028) 8676 7900.