Topping-up At Taff’s Well
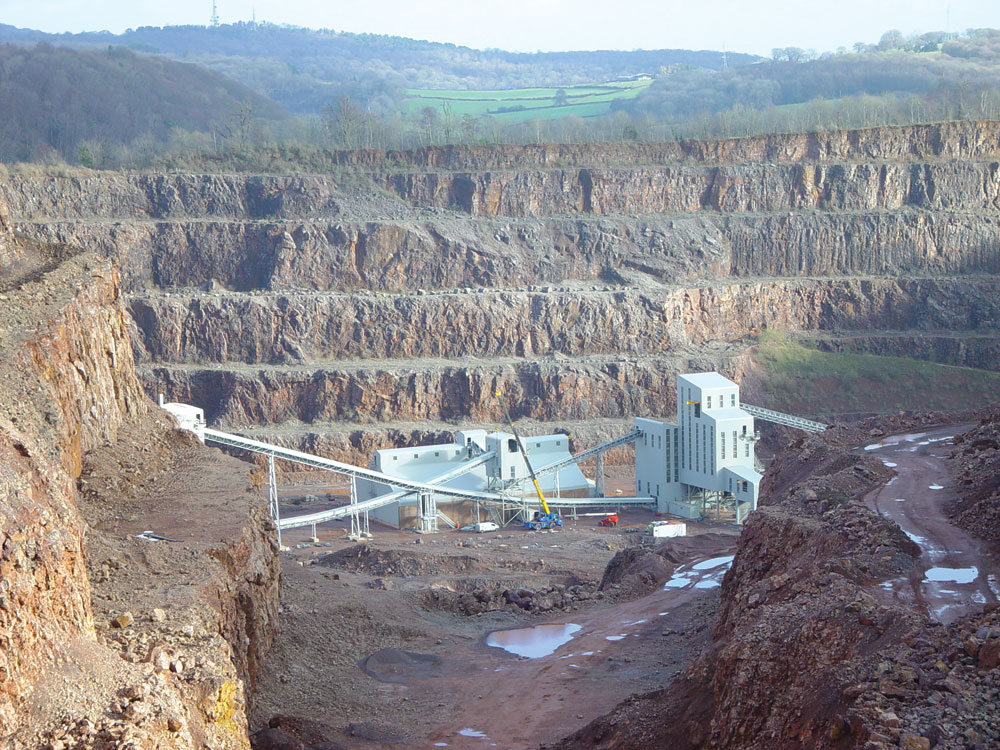
£15 million investment secures future of South Wales quarry for next 20 years
By May this year, Taff’s Well Quarry, near the village of Pentrych, just north of Cardiff, will have been given a new lease of life with the release of some 20 million tonnes of previously sterilized reserves, the commissioning of a brand new 1.4 million tonnes per annum processing plant set deep within the quarry basin, and a reduction in the impact of quarry transport movements on local roads, thanks to a newly created access tunnel. Overall, these developments will help secure the future of the site and its workforce for the next 20 years or more.
The 60ha limestone quarry, which has already been worked for more than 80 years, was owned by Steetley during the 1950s before being acquired by Redland Aggregates and then Lafarge. In March 1999, RMC bought the quarry from Lafarge to bolster their dwindling reserves at Wenvoe Quarry, some 11 miles south of Taff’s Well. Four years ago, the 1 million tonnes per annum quarry became part of CEMEX’s UK operations, following the Mexican firm’s acquisition of RMC in 2005.
Planning considerations
Discussions with the local planning authority and neighbouring communities of Pentrych, Morganstown and Radyr concerning the development and improvement of Taff’s Well Quarry first took place as far back as the 1980s, but it was not until 1998 that a Section 106 agreement was finally signed.
This included an obligation to improve access to the site, via a new road tunnel, as well as the removal of the existing processing plant and buildings from the skyline, to be replaced with a completely new plant on the quarry floor. Removal of the old plant, which currently stands 110m above the base of quarry and is visible from Cardiff, will not only improve the visual impact of the site, but will also provide access to a further 20 million tonnes of previously sterilized reserves.
The original Section 106 agreement included several key dates for the completion of various phases of the development work. However, to achieve greater project flexibility, this was subsequently modified to a single ‘guaranteed’ end date, whereby it was agreed that the new processing plant would be fully operational by May 2009 – a full year earlier than the original phased programme end date.
Also included under the Section 106 agreement is a commitment not to disturb the beech woodland which surrounds the quarry on three sides. This former SSSI, known as Garth Wood, is home to a rich variety of flora and fauna and was recently designated as a Special Area of Conservation (SAC) under the EC Habitats Directive.
In addition, CEMEX have made a commitment to the preserve the abandoned Garth Mine, which is located on the northern side of the quarry. Believed to date back to Roman times, these iron ore workings were mined intermittently until the mid-1900s, before finally being used as a secure location for the stockpiling of munitions during World War II.
New tunnel access
Representing an investment of around £4 million, construction of the new 200m long, two-lane access tunnel was undertaken by South Western Mining & Tunnelling Ltd. Work on the tunnel project began in late 2005 and took around 15 months to complete using drilling and blasting methods along its full length.
Wherever geological conditions allowed, the rock exposed in the tunnel was left in its natural state, however, the presence of numerous clay-filled bedding planes, faults and joints undermined the tunnel’s strength and stability in several areas, necessitating the use of various support measures, including rock bolts up to 5m in length, cable and grout bolts up to 7m in length and sprayed concrete with mesh.
Interestingly, the new tunnel portal on the quarry side intersects a disused railway tunnel, which was once used for the transportation of coal from the Welsh mines located further inland. On the non-quarry side of the tunnel, further excavation work was required beyond the entrance portal to link the new quarry access road into the existing road network. Work at this end also included the provision of a new roundabout at the quarry entrance, for the safety of quarry vehicles and other traffic.
Finally completed and commissioned for use in early 2007, the finished tunnel measures 10.2m in width and 7.5m in height, and has a 1 in 14.5 gradient. It has been specifically designed to allow any loads capable of travelling via the M4 motorway to pass through the tunnel, including machines the size of Cat 775 dumptrucks. In addition, the tunnel’s two carriageways are separated by a removable central barrier to facilitate the delivery or despatch of oversize loads.
Once the new plant is full commissioned in May 2009, all traffic entering and exiting Taff’s Well will use this route, making the site’s old access road redundant. This will eliminate all quarry traffic (up to 400 vehicle movements per day) from the adjacent minor road leading to the village of Pentrych, and will reduce the journey from the quarry to the A470 main road by around two miles.
Face operations
The geology at Taff’s Wells essentially comprises a series of northward dipping dolomitized limestones of Lower Carboniferous age, interbedded with clays and haematite near the top of the quarry. The stratigraphic sequence is complicated in several places by the presence of considerable folding and faulting, which has had, and will continue to have, some bearing on the excavation geometry.
However, the additional reserves that will be released by removing the existing processing plant from the top of the quarry will be more accessible than the current working area, and more amenable to future blasting operations. Once the new plant commences operations, the quarry’s 85-tonne Cat 385 face shovel will load a fleet of three Cat 775 rigid dumptrucks for the downhill haul to the site’s existing refurbished Lokotrack LT140 primary jaw crusher. Fed by a Cat 365 backacter, this skid-mounted, semi-mobile crushing unit will be located on one of the quarry’s southern benches and will feed material on to a field conveyor for delivery to a new scalping station.
New processing plant
Designed to produce a complete range of single-sized aggregates and blended products, and to meet or exceed all relevant UK/EU obligations and standards, the new plant infrastructure at Taff’s Well represents an investment of around £12 million. The main contracts for the project were awarded to a limited number of suppliers, with Whitwick Engineering (Coalville) Ltd appointed as main contractors for the mechanical engineering and materials handling aspects, and RMB Contractors Ltd, Dan Herrick Construction Ltd and SES responsible for the civils work, steel erection and electrics respectively.
Construction work commenced at the end of 2007, with the project being conducted in accordance with current CDM and health and safety regulations. One of the first tasks was the creation of concrete pad foundations to support the main plant structures. These were cast to a depth of 2m below ground level and tied into the limestone bedrock by means of 8m deep anchor holes. Concrete supplies for the support pad work, together with the subsequent steelwork and all other material requirements for the construction phase, were delivered to site via the newly created access tunnel.
The first element of the new 625 tonnes/h processing plant is located adjacent to the southern face of the quarry and comprises an Binder Bivitec double-deck, rigid scalping screen, together with its associated feed/discharge arrangements, all mounted on a steel support frame with access platforms and inclined stairways. Fed with primary crushed material from the feed conveyor located on the bench above, the scalping screen is designed to take out any –12mm material, while the coarser material passing over the screen is delivered to the secondary processing plant via an inclined, fully encapsulated conveyor – the first of 18 new link conveyors within the plant.
On arrival at the top of the secondary plant, the material is discharged into a twin-deck Don Valley selector screen, which is used to split the material into +75mm, –75mm +40mm and –40mm fractions. The two coarser sizes are discharged into two 230-tonne capacity selector bins equipped with 450 tonnes/h Skako vibratory tray feeders, which, in turn, feed a 180-tonne surge bin mounted above the secondary crusher. The –40mm fraction is discharged into a third selector bin from where it can be fed directly on to the main screen house feed conveyor or, alternatively, to a lorry load-out conveyor rated at 850 tonnes/h or to a 2,000-tonne ground stockpile.
The 450 tonnes/h Kleemann+Reiner SNH20 secondary impactor discharges its –40mm product on to the main screen house conveyor. Final screening is carried out by three dust-encapsulated Don Valley screens – a 3.4m x 7.0m triple-deck unit, a 3.0m x 7.0m double-deck unit, and a 2.4m x 5.0mm single-deck unit – all equipped with
Tema Isenmann modular panels. A highly effective dust-extraction system, supplied by Enviroflo Engineering Ltd, ensures that the main screen house remains virtually dust-free at all times.
In addition, Enviroflo Engineering have supplied equally beneficial dry foam dust-suppression systems for all crusher feed and discharge points within the plant, as well as water spray dust suppression for transfer points and discharge chutes on the lorry load-out and stocking conveyors, resulting in a significant reduction in the site’s overall level of emissions.
The three main screens deliver eight final product sizes: +40mm; –40mm +28mm; –28mm +20mm; –20mm +14mm; –14mm +10mm; –10mm +6mm; –6mm +4mm; and –4mm to dust. These are discharged into a series of eight storage bins with capacities ranging from 250 tonnes up to 700 tonnes. The method of bin discharge varies depending on the product characteristics, with the finest fraction being discharged by belt feeders and the coarsest fraction by vibro-feeders. The other six bins are discharged via high-accuracy Rowecon sliding-gate feeders.
Any of the sizes from the storage bins can be sent to a Kleemann+Reiner SNH12 tertiary impactor for re-crushing in a closed-circuit arrangement, with the –20mm tertiary crushed product rejoining the secondary crushed material and –40mm fraction on the main screen house feed conveyor.
The new plant is equipped with two product blending/lorry loading conveyor lines, both rated at 1,000 tonnes/h. These are automatically controlled by a Rowecon software system, which utilizes smart cards to allow drivers to collect their loads direct from the load-out bays without having to leave their cabs. The accuracy of the bin discharge/load-out system is such that drivers rarely have to top-up or tip off material, making turnaround times much quicker. An additional stock-out conveyor line is available to feed three 3,500-tonne capacity partly covered storage bays with any product size or blend direct from the final storage bins at a rate of up to 500 tonnes/h.
With the exception of the mobile primary crusher, all processing operations and load-out functions are fully automated by means of Scada control system, with various monitoring devices, including level-detection probes from Pulsar Process Measurement Ltd, used to measure and detect hopper and bin levels, conveyor loads, belt slippage, blocked chutes etc. The main control system architecture was developed in house and designed to fully integrate with the various third party software systems utilized throughout the plant.
Redevelopment of the quarry infrastructure also includes provision for a new road layout and traffic-management system, together with a new weighbridge office, administration offices, a meeting room and workstations for 10 personnel, as well as car parking facilities and staff welfare amenities.
Conclusion
Until the recent sharp decline in demand for construction materials, Taff’s Well Quarry’s existing processing plant was routinely producing up to 1 million tonnes of limestone per annum, the bulk of which was supplied to construction markets within a 10-mile radius of the site. Although the new plant has been designed and engineered with the potential capacity to produce up to 1.4 million tonnes per annum, CEMEX intend to maintain output at current reduced levels for the time being, albeit with the capability to deliver greater peak tonnages than before, when necessary.
Operating at less than peak capacity will allow for an effective and timely maintenance regime, which will be crucial to future operations, as the plant has been set up to operate on a ‘just-in-time’ basis, with some 2,000 tonnes of material storage being maintained ‘in the air’ at any one time and company policy specifying a maximum of 10 days stock on the ground.
By constructing a brand new plant within the quarry basin and demolishing the old plant, CEMEX are set to gain access to a further 20 million tonnes of reserves, thereby securing the future of the quarry and its staff until around 2030. At the same, the company will be reducing the impact of quarry transport on the surrounding villages and safeguarding the future of a number of significant historical and environmental features for future generations.
Acknowledgements
The editor wishes to thank CEMEX for permission to visit the site and, in particular, Dave Goodman, area operations manager, and Harry Paterson, project engineer, for their help in preparing this article.