Top Tower For Shap
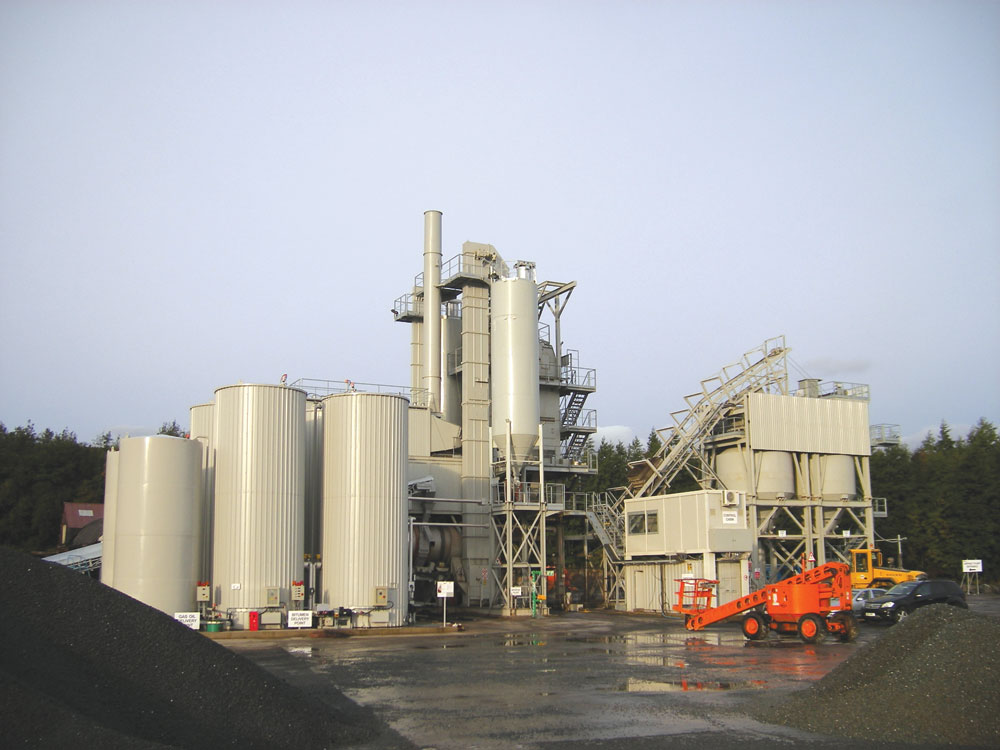
New asphalt plant offers energy and space-saving advantages for CEMEX
West Lothian-based Cormac Ltd have installed and commissioned a complete high-efficiency Marini Top Tower asphalt plant for CEMEX’s Shap Blue Quarry, in Cumbria. Cormac, who are well known for their high-efficiency bitumen storage tanks, took full responsibility for the CEMEX installation, having recently entered into an exclusive UK working relationship with leading Italian asphalt plant manufacturers Marini SpA.
The new plant has been purchased to produce up to 100,000 tonnes of coated stone per year, primarily using aggregates from the adjacent quarry. The coating plant is designed to operate up to 24h a day, seven days a week, allowing CEMEX to fulfil night-time contracts, when required, to avoid disruption to traffic during the day.
Planners placed strict environmental restraints on CEMEX to minimize carbon emissions and prevent dust or debris contaminating the local environment. In parallel, the company needed to minimize plant running costs without affecting performance and product quality.
According to Cormac, this new generation of energy-efficient asphalt plants has been developed to meet customers’ demands for versatility, quality and environmentally friendly solutions. By definition, asphalt production is an energy-hungry process, so, to minimize energy consumption at all stages of the process, the Top Tower uses a combination of innovative design and optimized insulation to achieve significant energy savings throughout.
Cormac claim that these design concepts can deliver energy savings in excess of 15%, while their own high-efficiency bitumen storage tanks provide savings of up to 50%, compared with traditional designs. Moreover, these savings also reduce the installed electrical capacity requirements.
The plant design is extremely compact and the main components are brought to site in a pre-assembled modular format, thus reducing on-site installation time. The Top Tower is technically compatible with all types of asphalt, including hot, half-warm and low-energy varieties.
Depending on the required layout of the storage unit for finished products, the plant can be configured in either under-mixer or offset format. There is an under-filter storage hopper for recovered fines and also a short fines recycling unit.
The patented screen design and direct double access ensures that the screen grilles can be changed easily and quickly, as required, while the multi-function metering-mixing unit features a large-section access door to facilitate the gravity emptying of aggregates, filler and bitumen. This also makes it simpler to introduce bagged additives, recycled materials and foamed bitumen.
The main burner, which is designed to minimize CO2 emissions and optimize energy consumption, can be adapted to run on light or heavy fuel oil, natural gas or coal, while the dryer drum itself features an efficient heat-recovery process, recycling waste heat back into the process to further reduce the burner’s fuel consumption.
By its nature, bitumen needs to be transported and stored at elevated temperatures. As a result, storage tanks can act as giant radiators, if not suitably insulated, devouring energy and adding, in a small way, to global warming. Cormac have been successful in significantly reducing the transfer of heat from the inner tank to the outer cladding, which, in turn, minimizes the amount of energy needed to maintain an optimum storage temperature for the bitumen.
The new tank design uses a combination of traditional insulation materials combined with a special reflective thermal coating. Together, these produce considerable energy savings compared with a conventionally clad tank design, reducing energy consumption by over 50%. To reduce energy consumption even further, the tanks are fitted with proprietary, progressive, multi-stage heating systems, which maintain the temperature of the bitumen within a preset bandwidth.
Cormac’s managing director, Steve Corbett, is very upbeat about his company’s new capabilities. He said: ‘The Marini designs represent the latest innovations in compact asphalt plant design. With our experience in asphalt plant implementation and bitumen tank design, we can now offer customers cost-effective, high-efficiency asphalt plants with production capacities from 60 to 300 tonnes/h.
‘Safety and environmental issues are also of paramount importance in our asphalt plant design. Our optimized burners reduce CO2 emissions, while special filters at strategic parts of the plant ensure dust or particles cannot be emitted to the atmosphere. The bitumen storage tanks are fitted with an RBA (Refined Bitumen Association)-compliant failsafe safety system to prevent overfilling and spillages. This system allows regular testing of critical components at ground level prior to each fill.’
Cormac Ltd, Unit 1, Burnhouse Industrial Estate, Whitburn, West Lothian EH47 0LQ; tel: (0141) 646 2066; fax: (0141) 646 2077; email: sales@cormac.co.uk