The Way Forward
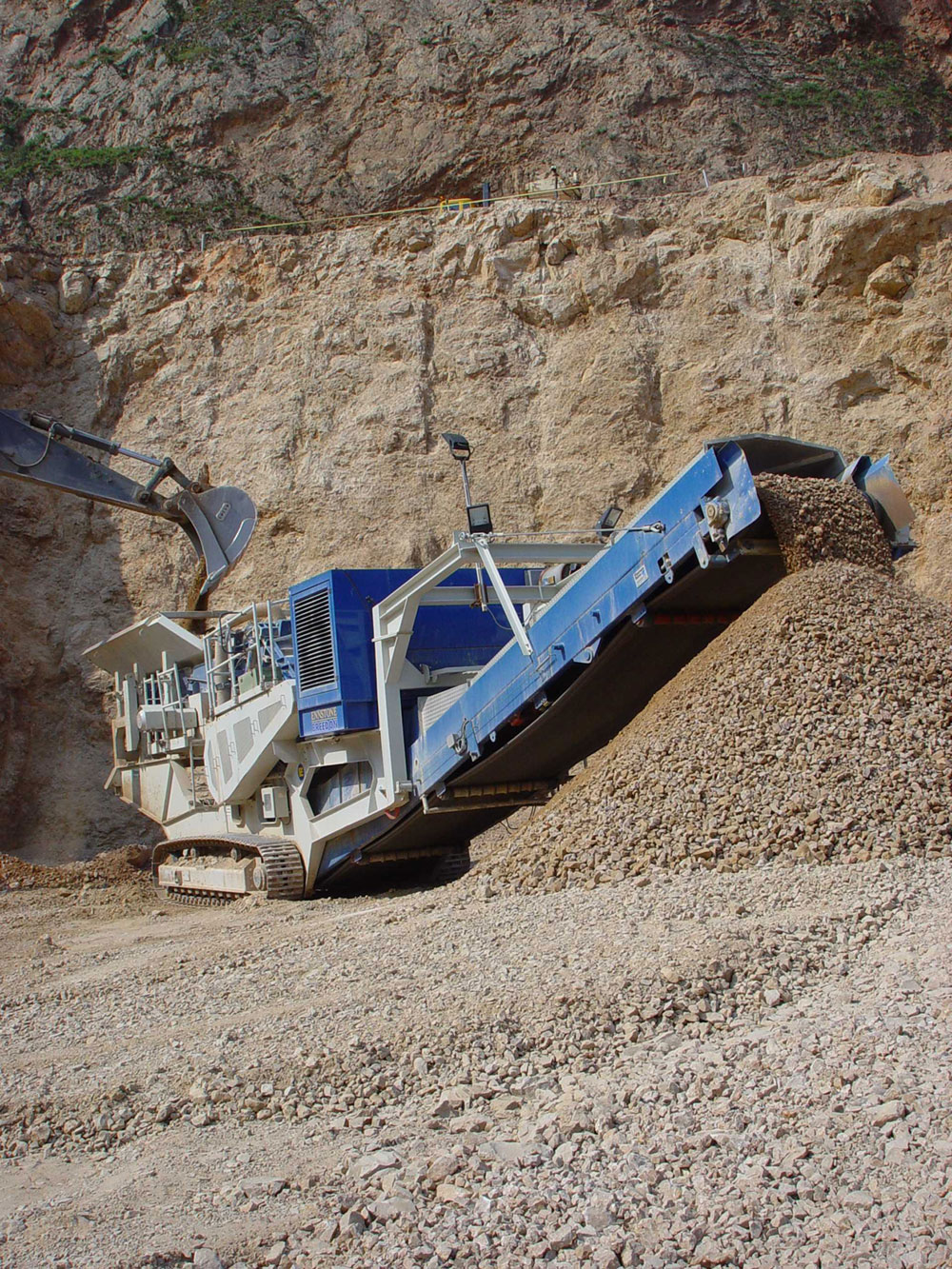
New tracked crushing and screening plant boosts productivity at Breedon on the Hill
Last year Ennstone Breedon Ltd, the English arm of Ennstone plc, invested in a new, fully mobile crushing and screening system for their flagship Carboniferous limestone quarry at Breedon on the Hill in Derbyshire. A decision was made to replace the site's existing 15-year-old O&K wheeled impactor with a Mobirex MRB 122Z tracked impactor from Kleemann + Reiner given the need for the operation to be able to deliver the lowest cost per tonne produced in an increasingly competitive market.
In recent years mobile crushing and screening technology has proved to be the ideal processing solution at Breedon on the Hill, owing to the considerable depth of the excavation and the somewhat narrow, restricted nature of the quarry. Nevertheless, the decision to invest in the new German-built machine required careful thought, as although Mobirex crushers are well established in their homeland and other parts of continental Europe, the range is still relatively new to the UK market.
Before purchasing the machine, however, Ennstone Breedon carried out six months of head-to-head evaluation trials with other leading makes of mobile crushers, as operations director Owen Batham explained: 'We were looking for the best value for money so we compared the performance of several different machines from a number of well known manufacturers. The MRB 122Z is a well engineered machine and proved to be best overall in terms of productivity and price.'
The new unit went into operation at Breedon on the Hill in October 2001. It is fed by a well matched, standard-specification, 47-tonne Volvo EC460 hydraulic excavator equipped with a 1.8m3 bucket, while at the discharge end an Extec 16 x 5 double-deck, three-way-split tracked screening unit receives the crushed material from the Mobirex and grades it into three saleable products (Type 1, –75mm +40mm and 5in). Both of these ancillary machines were purchased new to work in tandem with the crusher.
The direct-drive diesel-electro-hydraulic MRB 122Z is a rugged 67-tonne machine which accepts a maximum feed size of 1,200mm x 900mm and delivers a nominal throughput capacity of 350 tonnes/h. The unit incorporates a 6m3 feed hopper with a 3,500mm long feeder and a heavy-duty 1,200mm x 2,250mm independent double-deck vibrating scalping screen. At Breedon on the Hill this pre-screen has an upper-deck setting of 75mm while the bottom deck is blanked off — all fines pass forward and rejoin the crushed material flow by means of a by-pass chute. If required, however, fines passing the lower screen deck (when fitted) can be discharged to stockpile via a removable side conveyor.
The +75mm oversize from the pre-screen is fed into a 1,270mm wide x 1,250mm deep crushing chamber with a hydraulically adjustable inlet case that can be opened up to allow larger rocks to pass through. According to Mr Batham, this is a particularly useful feature of the machine, as to date the crusher has suffered no serious blockages whatsoever. The crusher itself comprises a 1,300mm diameter SHB 12-100 impactor driven by a 200kW electric motor. All adjustments to the operation of the crusher are carried out by means of hydraulic cylinders which are operated a the touch of a lever. This permits rapid adjustment of the two impact toggles, allowing fast product size changes ranging from 3in down to 9in down, as well as simplifying maintenance work. In addition, an integral hoist bar facilitates the changing of blow bars during routine maintenance.
Mounted directly below the crusher is a 1,300mm x 2,600mm independently vibrating tray feeder which provides an accessible 800mm of clearance. This heavy-duty, Hardox-lined unit is designed to receive and withstand the force of the crushed material output from the impactor and greatly assists in the free flow of material on to the fully enclosed 1,400mm wide x 10m long main discharge conveyor. This feeder unit also seals in the area where most spillage and dust problems tend to occur, thereby eliminating these potential nuisances at source. In addition, a by-pass hose system which utilizes air flow generated by the crusher rotor is used to recirculate dust from the crushing chamber back into the product flow.
The MRB 122Z is powered by a 312kW Scania power pack and Leroy Somer generator. This set-up provides adequate power reserves to drive ancillary equipment such as a lighting system and/or screening unit.
Designed to comply with health and safety requirements, the crusher features a range of mechanical and electrical safety features and cut-off devices including belt stop lanyards, limit switches, electrical interlocking systems, rotor locking pins and a safe start-up system with comprehensive diagnostic checks.
Processing the limestone deposit at Breedon on the Hill, the crusher achieves an average production rate of 280–300 tonnes/h. However, working with material from one particularly well fragmented rock pile, the unit has exceeded 400 tonnes/h to reach a peak production level of 5,000 tonnes in a single 12h shift, although as Owen Batham admitted, a considerable amount of material in this particular case was able to by-pass the impactor via the pre-screen. Nevertheless, he still regards the machine's productivity, versatility and manoeuvrability as highly impressive.
Accompanied by the EC460 excavator and the Extec screening plant, the crusher is moved to different faces in the quarry about three times a week, covering distances ranging from 50m to 400m. 'The machine is so productive that we are continually having to chase faces,' commented Mr Batham. 'We bring down about 5,000-6,000 tonnes of limestone per blast, which provides about two days' work for the Mobirex.
'Unlike our old wheeled crusher which was very slow and took too long to move around the site, the Mobirex makes light work of tracking round the quarry from one face to another and moving out of harm's way during blasting. During tracking the unit can be controlled from on board or by means of a remote control unit, however for safety reasons we prefer to have our man on board while we move the machine around,' said Mr Batham.
He added that the Extec three-way screener is equally manoeuvrable and more than capable of keeping pace with the output from the Mobirex, producing good-quality end products at rates of up to 400 tonnes/h.
With versatile and productive equipment such as this, Owen Batham believes mobile crushing and screening operations will be the way forward for many quarries in the years ahead. Indeed, he is now looking at larger mobile crushers including the MRB 122Z's big brother — a Mobirex unit capable of producing up to 600 tonnes/h — with a view to further expansion of Ennstone Breedon's mobile crushing and screening operations in the future.
Acknowledgement
The editor wishes to thank Ennstone Breedon for permission to visit the site and, in particular, operations director Owen Batham for help in preparing this article.