Replant At Scrooby Top
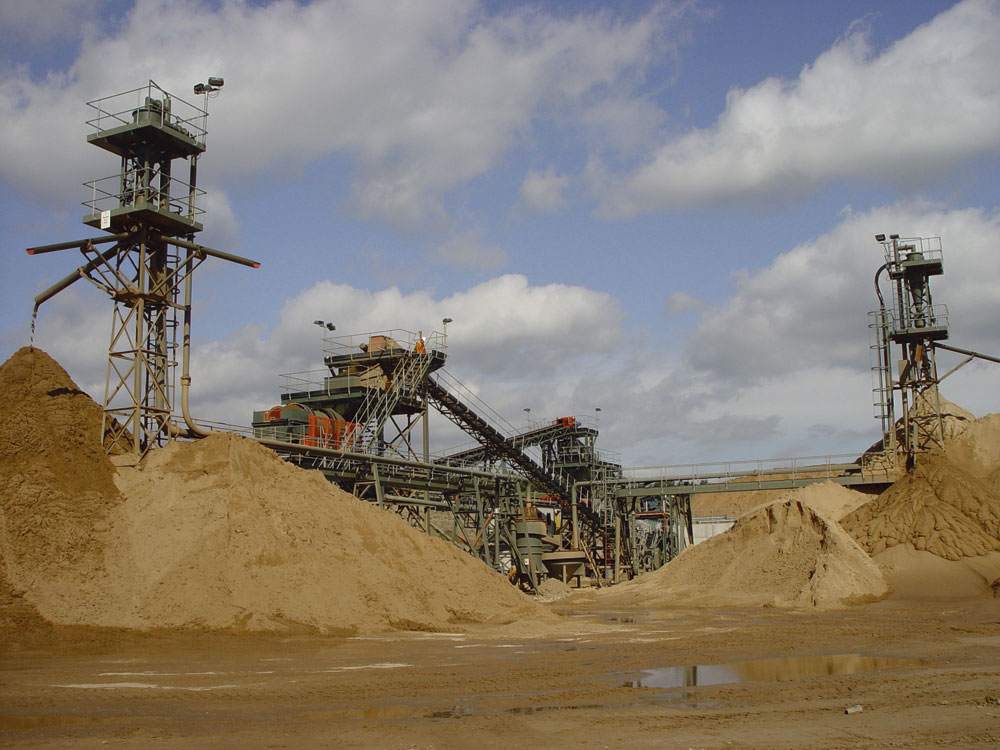
Rotherham Sand & Gravel invest £2.5 million in new plant for flagship site
Rotherham Sand & Gravel Co. Ltd, an independent, privately owned company, were founded in 1930 when farmer Samuel Scholey from North Nottinghamshire, together with an architect partner from Rotherham, formed a business to supply washed sand and gravel to the building and construction market. At this time the company’s offices were based at Devonshire House in Rotherham, South Yorkshire, hence the company name, although the quarry was actually located some 12 miles to the east at Scrooby Top, near Bawtry.
In the early days sand and gravel was loaded by hand into tubs on a narrow-gauge railway system and transported to the processing plant, which was one of the first washing plants to be built in the UK. The business expanded during the 1930s and by the onset of World War II large quantities of ballast were being produced to supply the military airfields being built in the area. At about this time W.G.S. Scholey took over the business from his father and led the company through the post-war redevelopment period of the 1950s and 1960s.
By the 1950s the overlying glacial sand and gravel deposit at Scrooby Top had been exhausted and extraction continued down into the underlying Sherwood sandstone, from which different grades, blends and colours of sand were developed. In the late 1970s RMC Mortars chose Scrooby Top as the site for one of their first ready-mixed mortar plants owing to the suitability of the Scrooby building sand, which was used to produce a wide range of coloured sand and lime mortars.
The present chairman and managing director, Paul Scholey, took over the reigns in 1981 and continued to expand the range of products and services available, including dry screened building sands, puddle clays and root-zone soil/sand mixes. Expansion into the ready-mixed concrete and floor screed market commenced in 1991 with the opening of Batchmix Ltd, followed more recently by the establishment of a bulk bag and pre-packed aggregates business, Batchpac, as well as facilities for the recycling of construction and demolition waste.
Some six years ago planning permission was sought to extend Scrooby Top Quarry. Approval for an extension containing around 15 years of new reserves was eventually granted by Nottinghamshire County Council, but with conditions attached that required a new access road to be constructed at the opposite side of the quarry. This would allow lorries direct access to the A638 without having to use the former access on to a ‘C’ class road. Planning conditions also stipulated that the processing plant should be relocated at a lower level to reduce its visual impact.
Rather than dismantling, moving and reassembling their existing ageing processing plant, Rotherham Sand & Gravel (RSG) decided to adopt a clean-sheet approach and invest in a new processing plant located within the quarry void close to the new access road. The contract for the design, manufacture and installation of the new washing and grading plant was awarded to Leicestershire-based Wileman Engineers Ltd, with Linatex providing the associated sand-processing facility. These new facilities, together with a new weighbridge installation, have had the added advantage of improving the flow of vehicles around the site, reducing the need for reversing to a minimum. In addition, as part of the overall redevelopment, a new ready-mixed concrete plant and pre-pack bagging facilities have been installed and a new office block has been constructed in a central location within the void to provide an overview of the entire site, resulting in a total investment of around £2.5 million over the past two years.
Including the sand-rich deposit at Scrooby Top Quarry itself, RSG’s total landholding amounts to some 400 acres, with the company operating a number of satellite extraction sites which supply sand and gravel to Scrooby Top for processing. The company produce a wide range of products including red and grey building sands, washed concrete, building and plastering sands, as well as clean 10mm and 20mm gravel, much of which is used for decorative purposes.
Washing plant
The sand and gravel extracted at RSG’s various sites extraction sites is stockpiled at Scrooby Top prior to processing. A Cat wheel loader is used to feed the as-raised material into a 20-tonne capacity dump hopper equipped with a vibrating scalping grid and Skako vibratory feeder trough, which is capable of handling up to 100 tonnes/h of –75mm material. The sand and gravel is fed on to a 43m long x 600mm wide inclined belt conveyor for delivery to the washing section. Powered by an 11kW motor, this delivery conveyor is capable of handling 100 tonnes/h of the as-raised sand and gravel plus approximately 20 tonnes/h of crushed oversize.
These materials are discharged into a 3.6m long x 1.5m wide Wileman double-deck vibrating screen inclined at 15° and equipped with spray bars. The screen is fitted with modular polyurethane screen media with 20mm apertures on the top deck and 5mm on the bottom deck. Washed –75mm +5mm material is discharged directly into a Wileman 15M27 scrubber barrel, a 1.5m diameter x 2.7m long contraflow unit that features perforated polyurethane elements to remove sand and dirty water at both the feed end and the discharge end of the barrel. The barrel is driven by a 30kW squirrel cage motor and directly coupled gearbox through standard pneumatic tyres.
The –5mm sand/water slurry from both the scrubber barrel and the preceding wet screen is flumed to a lined collection box and then piped to a Linatex sand classification and dewatering system, while the coarse fraction from the scrubber barrel is discharged into a Metso Aquamator AK 3.5/1200/160, which effectively separates any lower-density material (wood, roots etc) from the clean aggregate. These lightweights are floated off and discharged, via a sieve bend, into a debris collection bay, while the contaminant-free gravel is fed on to a 41m long x 600mm wide inclined conveyor, capable of handling around 55 tonnes/h of –75mm +5mm material, for delivery to the grading section. This belt discharges on to another 3.6m long x 1.5m wide Wileman double-deck sizing screen fitted with modular polyurethane screen media with 20mm apertures on the top deck and 10mm apertures on the bottom. This dry screen and the previous wet version are the first screens to be designed and built by Wileman. Both screens feature an all-bolted design for easy maintenance together with a galvanized surface finish for maximum protection.
The dry screen separates the incoming feed into –20mm +10mm and –10mm +6mm gravel fractions, which are discharged to ground stockpiles via two 15m long x 600mm wide stockpile conveyors, each capable of handling 50 tonnes/h. At the same time, oversize rejected by the dry screen is fed into a 20-tonne capacity surge hopper equipped with low/high level indicators and a Skako vibratory feeder trough that delivers approximately 20 tonnes/h of the –75mm +20mm into a Kue-Ken Rockeater jaw crusher. The crusher discharges the crushed product back on to the primary feed conveyor for recirculation through the plant in a closed-circuit arrangement. Alternatively, the oversize can be discharged to a ground stockpile via an overflow chute on the surge hopper, thereby permitting continual plant operation without the crusher.
Sand plant
The sand slurry from the Wileman washing plant is piped directly to a Linatex sand classification and dewatering plant capable of processing up to 100 tonnes/h of –5mm solids in some 600 gal/min of water containing around 10% silt. The plant is configured to produce approximately 65% concrete sand, 30% building sand and 5% waste fines.
The –5mm slurry is piped into the centre of a 1.2m diameter S-Type classifier where the graded split on the sands takes place. A Linatex 150/125mm Mk III centrifugal pump powered by a 37kW motor draws the coarse concrete sand fraction from the base of the classifier and feeds it, via 150mm bore pipework, to a Linatex HK150 sand separator for washing and dewatering. Overflow from the separator is piped to a terminating point adjacent to the S-Type classifier, from where it can be discharged the quarry’s silt pond or partially recirculated via the classifier. The coarse sand fraction is discharged to ground stockpile via three sand chutes. The height of the separator tower provides a stockpile capacity of approximately 3,000 tonnes.
Meanwhile, the overflow from the S-Type classifier is flumed to the centre of a 2.4m diameter feed-regulating sump. A Linatex 150/125mm MK III centrifugal pump powered by a 30kW motor draws the fine sand slurry from the base of the sump and feeds it, via 125mm bore pipework, to a Linatex HK125 sand separator which washes and dewaters the fine sand fraction. This separator features an extended section to help retain more sub-micron fines, if required. Once again, the fine sand is discharged to a ground stockpile of approximately 3,000 tonnes capacity, while the overflow from the separator is discharged to the silt pond or partially recirculated via the feed-regulating sump.
Other developments
Operated by RSG subsidiary Batchmix Ltd, Scrooby Top’s newly commissioned ready-mix concrete plant replaces an earlier 60m3/h dry and wet mix plant. Supplied and installed by Basford Plant Ltd and capable of outputs of up to 100m3/h, the new facility features a 1.5m3 Teka paddle mixer with auto wash-out, six covered aggregate bins and three cement silos for full flexibility in mix design and production. A WAM Filcontrol dust-extraction system is utilized within the plant, with recovered dust being screw fed back into the mixer. Ready-mixed concretes, floor screeds and special mixes are supplied throughout Nottinghamshire, Lincolnshire and South Yorkshire using Batchmix’s fleet of 6m3 and 4m3 truckmixers.
Another recent development at Scrooby Top is the installation of a new pre-pack bagging plant, operated by RSG subsidiary Batchpac Ltd, for the supply of both indigenous sand and gravel as well as imported stone in 25kg and 40kg polythene bags. The plant is fed via a 10-tonne side-feed hopper with an adjustable flow-control gate and 7m long discharge conveyor. This unit, together with various weighing, bagging, sealing, handling and stacking equipment, including a Kawasaki ZD130 robot arm with pneumatic grab hand, as well as the associated guarding and plant control equipment, was supplied by Haith Industrial Ltd. With the exception of the hopper unit, which is situated externally and feeds into the building, the entire bagging plant is housed within a modern, purpose-built structure.
With their new state-of-the-art processing plant and equipment, together with an expanding range of products and services, and planning permission to extend their flagship operation at Scrooby Top, RSG are now well positioned to meet the challenges of the future. Yet despite employing some of latest technology available, RSG have still managed to maintain their reputation for providing customers with the ‘personal touch’, which has been the company’s hallmark for nearly 80 years.
Acknowledgement
The editor wishes to thank Rotherham Sand & Gravel Ltd for permission to visit the site and, in particular, Paul Scholey, chairman and managing director, for his help in preparing this article.