Phoenix Transworld Selected For Budore Quarry
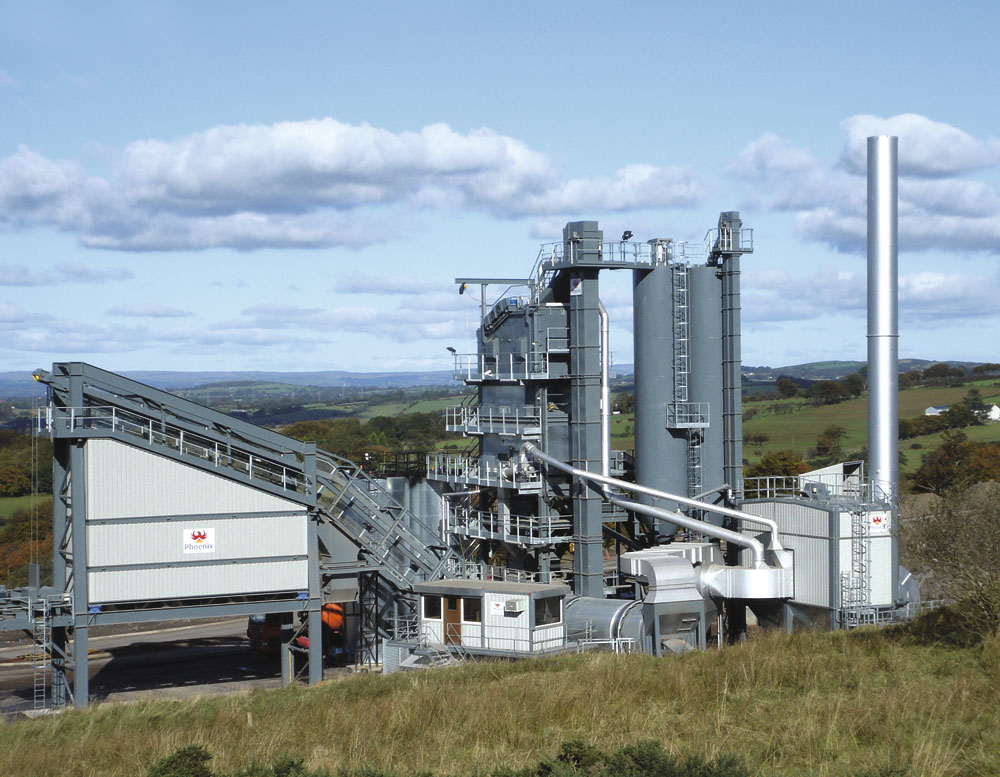
New 240 tonnes/h StarMix asphalt plant for Edentrillick Quarries
Nestling on the side of a hill close to Dundrod and with a clear view of Belfast International Airport just a few miles away is the latest 240 tonnes/h StarMix 3000 asphalt mixing plant designed, manufactured and installed by Phoenix Transworld. Its owners, Edentrillick Quarries, made this significant investment at Budore Quarry in order to service new road-surfacing contracts awarded by the local authority and highways department, as well as to supply other independent operators in the area.
To fulfil these needs, an asphalt plant was required that would be able to consistently and reliably supply a wide range of high-quality asphalt mixes on demand. Edentrillick Quarries approached Phoenix Transworld for a plant that would not only be capable of producing high volumes of hot-rolled asphalt with 5% moisture in the feed, including the facility to handle recycled asphalt planings (RAP), but would also, because of its location, satisfy strict environmental controls.
The Phoenix StarMix 3000 was selected for this project and the plant was installed and commissioned in September/October 2005.
The plant’s feed system comprises eight cold-feed hoppers, each having a capacity of 20m3 and a width of 4m, thereby permitting high loading rates of virgin feed to ensure that plant throughput is maintained. Feed control from each hopper is achieved using belt feeders with AC, inverter-controlled, variable-speed motors with 20:1 turndown capability. Two hoppers for sand are fitted with motor vibrators to ensure material flows freely. By enclosing all the hoppers on three sides and with a roof, dust from the feed stocks is contained and effective weather protection provided.
Feed material is transported by two fully covered, weather-proofed conveyors to a 2.5m diameter x 9m long dryer, which is externally lagged with 100mm thick energy-saving mineral wool insulation. The dryer is driven by four 22kW friction-drive motors through nylon support rollers for longer life and lower maintenance.
The use of an inverter to control and vary the speed of the main 110kW exhaust fan greatly reduces power consumption and increases dryer efficiency when linked to the continuous monitoring of differential pressures across the dryer and filter. This controls and extracts from the dryer only that amount of air necessary for optimum combustion.
The hot aggregates pass to a twin-chain vertical elevator equipped with a backstop facility and are discharged on to a totally enclosed six-deck vibrating screen. With over 48m2 of screening area separating six sizes plus rejects, the screen is more than adequate to handle the full plant capacity. The unit is fully insulated with 75mm high-density mineral wool to retain heat and is activated by two externally mounted, oil-lubricated shafts to allow very-high-temperature mixes to be produced.
Material from the screen discharges into an insulated seven-compartment hot-aggregate storage facility with a total capacity of 75 tonnes. Five compartments are for sized aggregates and two have a remotely operated selector door for sand and fines, thus permitting on-demand production of either hot-rolled asphalt or basecourse without the need to empty the sand bin.
All weighing and mixing is computer controlled from the operator’s control cabin with weigh hoppers mounted on load-cells.
The plant’s high-efficiency twin-shaft paddle mixer is driven through two shaft-mounted, direct-synchronized geared motors and has a single-batch capacity of 3,250kg.
Two 60m3 capacity silos for reclaimed and imported fillers are mounted adjacent to the mixing tower. Dust collected by the plant’s bag-filter is transferred, via a screw conveyor and vertical elevator, directly into the reclaimed filler silo. Filler from either silo is delivered to the filler weigh hopper via screw conveyors.
Up to 25 tonnes/h of excess reclaimed filler can be processed in the plant’s twin-shaft dust conditioner, which discharges to a holding bay for eventual disposal.
An important aspect of the plant is the ability to introduce RAP into the mix. Fully enclosed on three sides and covered with a roof, a steep-sided, 8m3 capacity feed hopper delivers the RAP, via a variable-speed belt feeder, on to a feed conveyor. This passes the RAP on to the mixer weigh feeder mounted at mixer level. An inverter controls the speed of the weigh feeder, which is mounted on four load-cells with full dust covers and weather-proofing.
The feed conveyor and hopper feeder load the weigh feeder, stopping only when the exact predetermined percentage weight of RAP corresponding to the weight of material in the mixer is reached. At the appropriate time in the mix cycle, the weigh feeder discharges the RAP into the mixer. Simultaneously, using electronic timers and pneumatics, a door within the mixer housing opens to allow steam created by the addition of the RAP to be exhausted from the mixer into a duct equipped with a fan, which discharges the extracted steam into the bag-filter.
The bag-filter is designed to filter 93,500m3/h, all of which passes to the exhaust stack, which is continuously monitored for the presence of particulates. The results are transmitted to the control cabin where average readings, in milligrams per cubic metre, are displayed and logged. Although the imposed emission limit is 20mg/m3, the filtration efficiency of the plant is such that recorded levels are in low single figures.
Mixed material is transferred by inclined skip to a three-compartment, 210-tonne capacity storage facility. The three silos are mounted on a single base frame on four load-cells, which are linked to an automatic load-out system in the operator’s cabin.
To maintain high thermal efficiency throughout the plant, the dryer, screen, hot-aggregate storage bins and mixed-material storage silos are all fully lagged with up to 150mm thick high-density mineral wool.
Phoenix Transworld assumed the role of main contractor during installation and took on full responsibility for compliance with UK health and safety directives and CDM regulations. Particular attention was paid to safety considerations throughout the plant, with all moving components, such as feeders, feed conveyors and the dryer, being completely fenced off with access only permitted through electrically interlocked entry points. In addition, all elevated sections of the plant are fitted with safety handrails and are easily accessible for maintenance, and lighting is fitted at all levels of the plant.