New Plant For Cloddach Quarry
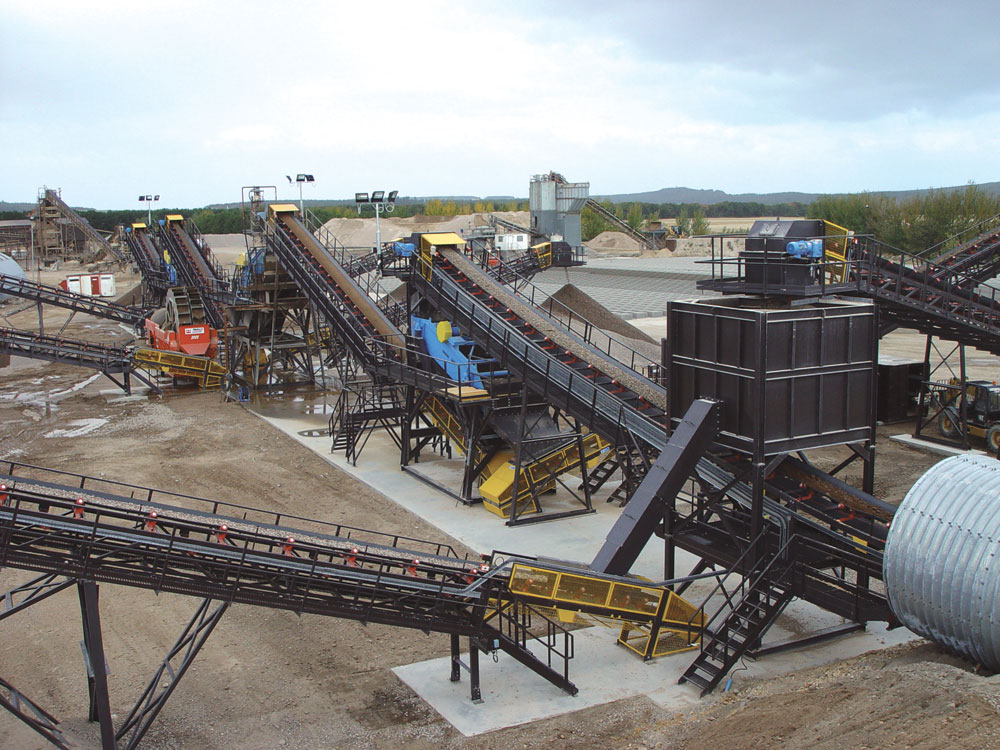
Quarry replant boosts output and improves health and safety
Straddling the river Lossie about two miles south of Elgin in Scotland lies Cloddach Quarry, one of Tarmac Northern’s northernmost outposts. The sand and gravel site operates under the banner of Tarmac’s wholly owned Scottish subsidiary, Tarmac Caledonian, a business which covers the Highland and Moray regions around Inverness and the Moray Firth.
Earlier this year over £1.1 million was invested in Cloddach to replace the site’s aging processing plant, which was already second-hand when first installed at the quarry in the 1970s, with a brand new crushing and screening plant. With around 10 years of proven reserves remaining at the site at current levels of production, replacement of the old plant was necessary for a number of reasons, not least of which was its inability to meet future production requirements. Another significant factor in the decision to replant was the extent of corrosion on the existing structures, which had reached a point where it was beginning to pose a potential threat to health and safety, a situation very much at variance with Tarmac’s commitment to eradicate all lost-time incidents from their business by 2005.
The contract to carry out the replant was awarded to Annan-based quarry design and installation specialists John Hope Engineering Ltd, with the civils and electrical work sub-contracted by them to local firms McDonald Formwork and Number One Building Services respectively.
Designed within the parameters of earlier permissions, no formal planning process was required to build the new plant, which was constructed on an area adjacent to the old plant and in line with the quarry’s existing raw feed arrangement. This allowed the old plant to maintain production levels throughout most of the build period, with just one week’s shutdown during changeover to the new plant.
Thanks to a concerted effort by the quarry manager, Tarmac Northern’s in-house project engineers and the various contractors involved, in particular John Hope’s lead team of engineers, all of whom hold the industry’s Safety Passport qualification, commissioning took place in mid-August 2003 just 10 weeks after the first concrete foundation slabs were laid. Most impressive of all, however, was the fact that, from the outset, the plant worked virtually faultlessly and to specification, requiring little more than minor tweaks and adjustments to bring it on stream at its maximum capacity of 250 tonnes/h.
With the new plant now fully operational Cloddach Quarry has the flexibility to step up annual output by around 30%. The plant itself is designed to produce six discrete finished products (Type 1, 20mm, 14mm, 10mm and 6mm and sharp sand) but can also be configured to produce a –14mm +5mm ‘bypass’ product for Cloddach’s on-site concrete block-making plant, which turns out around 4 million blocks a year for sale to markets in this part of Scotland and also as far afield as the Isle of Skye and Ullapool.
The post-glacial sand and gravel deposit at Cloddach is extracted by a new Caterpillar 972G wheel loader, part of a £650,000 investment in new loading shovels at this and other Tarmac sites in the area. At present, only the top 3m of the 6m thick deposit is worked, the remaining 3m lying beneath the level of the water table which currently defines the base of the pit. Future extraction of reserves to the north of the site will involve wet working.
The quarry’s existing primary section, extending from the feed station adjacent to the working face to the primary stockpile conveyor, was not part of the recent replant. The shovel-fed Allis feed hopper with its remote-controlled tipping grizzly screen feeds on to a 400m long field conveyor which delivers the sand and gravel to a Goodwin Barsby 36 x 24 mobile primary jaw crusher.
From here –100mm material is delivered to a primary stockpile via a 150m long field conveyor (part of the original feed arrangement to the old plant) and a new 900mm wide stockpile conveyor equipped with a Siemens belt weigher, this being the first of eight new material-transfer conveyors and four stocking-out conveyors, all fitted with stairway access, double walkways and emergency trip wires from Craig & Derricott. Designed and built by John Hope Engineering, all the conveyors are driven by energy-saving, high-efficiency, shaft-mounted gearbox units from Flender.
Material is drawn from the 1,000-tonne live capacity primary stockpile by two Skako vibratory feeders mounted within a gently inclined Armco reclaim tunnel which is open at both ends for ease of access and maintenance. Each feeder is generally set up to discharge material on to the 900mm wide reclaim belt at around 100 tonnes/h, although either unit is fully capable of feeding the 250 tonnes/h plant in isolation if necessary.
The reclaimed material is belt weighed as it is fed to a single-deck scalping screen with a top-mounted drive unit, this being the first of three 6m x 1.8m Roxon screen units supplied by Sandvik Rock Processing. Fitted with modular screen panels from Tema Isenmann, the scalping screen splits the reclaimed material at 20mm, with all +20mm material rejected by the screen being conveyed to a Sandvik H3800 cone crusher via a 750mm wide inclined belt equipped with an Eriez Magnetics metal detection system. Fed from a feed hopper mounted on the crusher support structure, the H3800 operates at a close-side setting of 22mm.
The crushed product is fed to a holding hopper mounted directly above the reclaim conveyor, from where it is discharged back on to the main material flow to the scalping screen or, alternatively, sent directly to a Type 1 stockpile via a 650mm wide inclined conveyor.
The –20mm material underflow from the scalping screen is carried forward to a double-deck washing screen equipped with spray bars and configured to split the material at 14mm and 5mm. The –20mm +14mm rejected by the top deck is sent directly to stockpile by a 650mm wide stocking-out conveyor, while the –5mm underflow from the bottom deck is discharged into an adjacent Finlay 200E Hydrasander unit which separates and dewaters the sand fraction to produce a clean sharp sand product (Cloddach only produces concrete sand as the raw material has a very low fine sand content). The concrete sand is discharged directly to stockpile by a 750mm wide sand conveyor.
Meanwhile, the –14mm +5mm fraction is delivered to a final double-deck grading screen for separation into 14mm, 10mm and 6mm final products. When necessary, however, the –14mm +5mm fraction can be diverted around the final screen to be stockpiled ready for use by the adjacent block-making plant. This is achieved by means of a bypass chute which delivers the material on to the 750mm wide stockpile conveyor which would otherwise carry the 6mm finished product. As an energy-saving measure, the bypass chute features and electrically operated changeover gate which, when activated, results in the automatic shutdown of the 650mm wide 14mm and 10mm finished product stockpile conveyors.
The entire plant is operated by one person on a sequential start/stop basis via a SCADA-based control system housed in a containerized control room that sits alongside the plant. Load out and rehandling duties, and the transfer of material to the block-making plant, are carried out by two Cat wheel loaders, a 966G and a smaller 962G.
On completion of extraction operations at Cloddach Quarry, the site will be fully restored to its pre-existing mix of arable farmland and native scrubland together with new areas of wetland. However, the operational life of the new plant will not come to an end at the this time, as the entire facility has been designed and built with future relocation in mind. Mounted on skids to facilitate easy dismantling, the plant is expected to have a second phase of life at another of Tarmac Caledonians’ sand and gravel operations in the region.
Acknowledgement
The editor wishes to thank Tarmac Northern for permission to visit the site and, in particular, Eddie Walker, quarry manager, David Chalmers, area engineer, and John McGill, project engineer, for their help in preparing this report.