New Block-making Operation At Carew Quarries
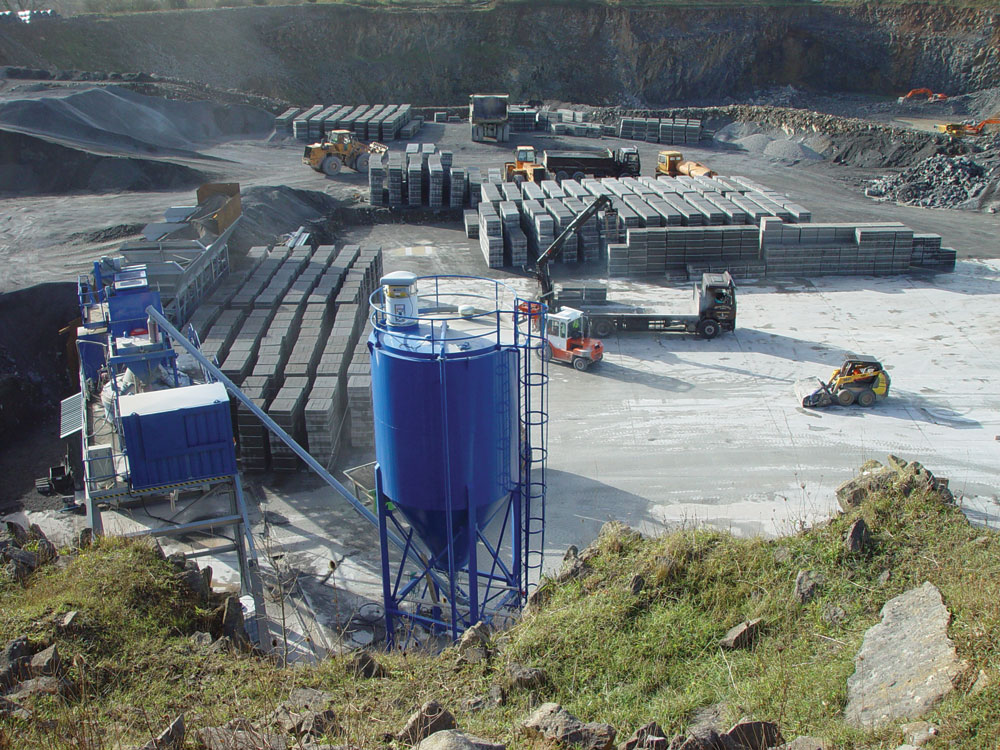
Thomas Scourfield & Sons. expand their product range
In this their 80th year in business, privately owned quarrying company Thomas Scourfield & Sons have expanded their product range with the installation of a brand new concrete block-making plant at Carew Quarries in south Pembrokeshire. Designed to add value to the company’s Carboniferous limestone aggregate products and help provide a secure future for the company’s 24 staff, the operation has been an instant success and is said to have captured a considerable proportion of the local concrete block market in the six months since production began.
Planning permission for the new operation was granted in February 2002 and initial preparations got under way with the laying of a flat, 4,500m2 area of reinforced concrete to accommodate the new operation. Located on what was once an aggregate stockpile area adjacent to the main quarry plant, this slab was constructed to a depth of 200mm using 40N concrete with added fibre mesh, supplied by both Hanson and RMC.
The order for the new concrete plant and block-making equipment was placed with Ross-on-Wye-based ConMac, agents for Finlay BME, at the end of March. The plant selected comprises a fully automatic, continuous-mix batching plant, together with an automatic mobile block-making machine and an automatic mobile block-strapping machine, all of which were on site and fully operational by the end of May.
A range of block types and sizes, including lightweight versions and concrete bricks, are now produced at the site, although production is largely centred around manufacture of 440mm x 200mm x 98mm solid blocks. At present production is weather-dependent, but planned developments at the site include the construction of an enclosed structure over part of the concrete slab to allow all-weather manufacturing to take place.
The batching plant
The new continuous-mix batching plant utilizes –10mm, –6mm +3mm and –3mm aggregates which are delivered by wheel loader to three 25-tonne in-line aggregate bins, each equipped with pneumatic doors and mounted above a 3.0m3 weigh hopper and 900mm wide drag-out conveyor. This feeds on to a 13m long inclined chevron conveyor which delivers the stone to a 2.5m3 capacity dry-batch hopper where the weighed, dry aggregates are held ready for discharge into the mixer while the previous batch is being mixed.
The dry batch is gravity fed into a 2,250-litre Kabag Wiggert planetary counter-current unit for mixing. Water drawn from the quarry’s existing silt lagoon is added to the mix via a 4,500-litre header tank. This tank also provides mixer wash-down water via a high-pressure pump.
High-strength ordinary Portland cement suitable for block-making is supplied to the site by Swansea-based Morrissey Cement and held in a single 60-tonne capacity storage silo. The cement is delivered to the mixer unit via a screw conveyor and 500kg capacity weigh hopper.
After mixing has been completed the concrete is discharged into a 4.0m3 wet-batch hopper mounted below the mixer unit. From here a Case W30 wheel loader fitted with a purpose-built 2.0m3 skip attachment collects the concrete and delivers it to the mobile block-making machine. The plant is also equipped with a ready-mixed concrete discharge chute, although this is not used at present and the company says it has no plans to enter this particular market.
Plant control
The fully automated plant is controlled by a 2010 control system supplied by Pneutrol Ireland Ltd (PIL) of Co. Antrim. This particular system, which has the capacity to store up to 100 mix recipes, is designed around the Allen-Bradley SLC500 range of PLC equipment with an Allen-Bradley Panelview user interface. The controls are housed in a small cabin situated adjacent to the mixer and comprise a starter panel, control panel and mimic display.
Control and monitoring of the entire plant is carried out by a single operator with inputting conducted via a standard keyboard. Detailed information is displayed on the colour monitor and the operator has the option of printing batch records, recipe details, material usage, alarm conditions etc. Significant features of the control system include: automatic weighing with two-stage feed control; automatic in-flight compensation; automatic zeroing; zero checking; and stock control.
During batch weighing, aggregates and cement are accurately weighed and should they fall outside set tolerance levels an alarm message is raised, allowing acceptance or rejection as required. Audible and/or visual alarms are also triggered by other system problems and faults, and printouts showing details of any fault, with the date and time, can be generated.
Water input is controlled by a Hydronix Hydro-Mix V microwave moisture probe in the mixer unit. This checks the moisture content of the dry aggregate during the dry mixing cycle and provides a 4–20mA output, via a Hydro-View display, to the PLC system which then calculates the amount of water required at the end of the dry-mixing time on a ‘one-shot’ basis.
In addition, an adjustment panel is positioned at ground level so that manual changes can be made to the moisture content. This allows the plant operator to quickly alter the water input in situations where the aggregate moisture content is particularly variable.
Block-making
The blocks themselves are produced by a Finlay F44 Super GA Universal mobile block-making machine, which is capable of forming and ‘laying’ around 4,000 units per hour. Powered by a six-cylinder air-cooled Deutz diesel engine which operates a 55kVA generator, the machine features a fully automated steering and production cycle which only requires manual intervention for turnarounds at the end of each row of newly laid blocks. With its ability to manufacture blocks on end, the F44 is able to produce two clusters of 44 solid, 98mm wide blocks in less than 1min. The machine can be fitted with a range of different moulds to provide block heights between 190mm and 450mm, while its ‘universal’ capability means it can also manufacture cavity blocks and concrete bricks.
Each group of 44 ‘green’ blocks is left to cure on the slab for a period of 48h before being clamped together by a fully automatic Finlay BSM412 mobile block-strapping machine. This unit is powered by a three-cylinder air-cooled Deutz diesel engine which operates a 16.5kVA generator and, like its block-making stablemate, has a fully automatic steering and production cycle. The strapping operation is performed by a Orgapack ORT 230 strapping head.
Once strapped, two packs of blocks at a time are lifted from the slab, moved to the storage area and stacked ready for sale using a Finlay CPC 4T46 block clamp mounted on a new Merlo 37KT telehandler supplied by Mason Bros. of Narberth. The same equipment combination is used to load the blocks on to delivery vehicles. To help foster their new business, Thomas Scourfield & Sons have acquired three new flat-bed delivery vehicles equipped with crane off-load. In addition, the company is currently involved in the design and development of a ‘removable’ crane attachment which will allow the quarry’s existing fleet of tipper trucks to be utilized for occasional block deliveries.
To ensure that quality requirements are met consistently, sample blocks are regularly tested for strength in the quarry’s on-site laboratory. These tests are conducted on a Controls Automax Series-5 automatic compression testing machine supplied by Controls Testing Equipment Ltd of Tring in Hertfordshire. Designed for the rapid testing of concrete blocks and cubes, this state-of-the-art system provides a real-time graphical display of load/time output data and provides storage for up to 150 test results. Stored data can also be downloaded to a PC and/or printer via two RS232 ports.
With their new facility Thomas Scourfield & Sons have the capacity to produce up to 40,000 concrete blocks a day. These are sold and used throughout Pembrokeshire, with some deliveries taking place up to 40 [road] miles away. Although only six months old, the plant has already supplied a number of significant contracts in this part of South Wales, including a large order for a close-textured grade of block, selected on the basis of quality and appearance, for use in the construction of a new extension to Pembrokeshire College in Haverfordwest.
Acknowledgement
The editor would like to thank Thomas Scourfield & Sons for permission to visit the site and, in particular, Ken, Mike and Roger Scourfield for their help in preparing this article.