Making Commercial Product from Waste
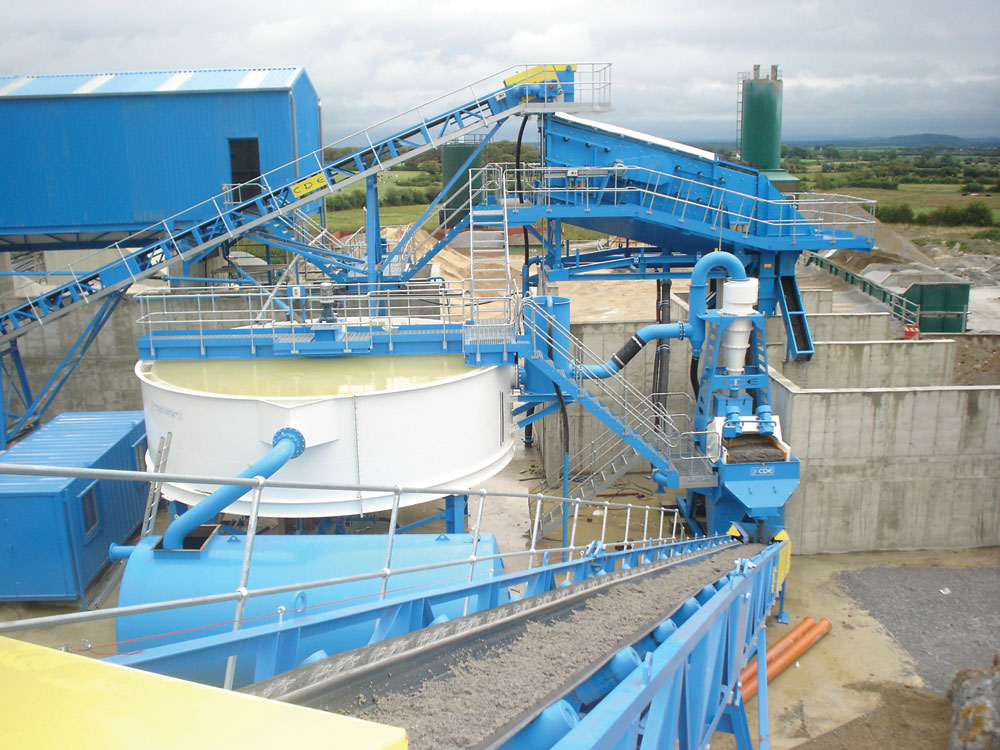
Liam Lynch (Quarries) Ltd install CDE dust-washing plant at Croom
County Tyrone-based CDE Ireland Ltd, specialists in the design and manufacture of tailor-made processing equipment for the sand and aggregates industries, have recently installed a complete new processing system for Liam Lynch (Quarries) Ltd’s limestone quarry in Croom, Co. Limerick. The system includes Ireland’s first overhead-beam GHT filter press, which recycles the maximum amount of water possible and reduces water requirements at the site to only a small amount of top-up.
The quarry itself produces 20mm, 14mm and 10mm single-size aggregates, an 804 (crushed –2in material), and a 6–0mm dust by-product, which, in common with many quarries in the UK and Ireland, was previously being stockpiled as waste, as traditional washing and dry screening systems were unable to make a commercial product from the material.
The new CDE system, however, washes the 6–0mm dust to produce a concrete sand by removing the –75 micron material. This sand is used by Liam Lynch in their own ready-mixed concrete batching plant. Before the new system was installed, it had been necessary to buy in all of the sand required for concrete production. Now only 20% of the concrete sand needed is bought, with the other 80% being produced from the quarry’s waste dust.
The CDE plant is also used to wash quantities of dirty overburden that the site’s traditional dry screening systems could not process. This is washed to produce clean 20mm, 10mm and sand grades for concrete mixes, while any washed oversize is recirculated through the site’s crushing plant.
The CDE process
Material is fed by loading shovel into an integrated CDE hopper-conveyor via an access ramp. The hopper and inclined feed conveyor arrangement was correctly aligned during manufacture to reduce on-site installation time and minimize any subsequent spillage. From here the material is fed directly into a CDE R3M108 (1.8m x 6m) triple-deck rinsing screen mounted on concrete walls. This washes and sizes the products for discharge into oversize, 20mm, 10mm and grit stockpiles, while the sand content is forwarded to a CDE C-62 compact sand plant where the –75 micron material is removed.
[img_assist|nid=12257|title=CDE R3M108|desc=|link=none|align=left|width=266|height=200]Equipped with an integrated hydrocyclone, the C-62 plant is able to accurately remove the –75 micron fraction while avoiding the loss of fines problem often associated with more traditional wheel- and screw-type washing plants. Also, thanks to the plant’s de-watering screen, the final sand is dried to approximately 12% moisture content, which is significantly drier than several other washing plants currently available.
The CDE compact plant range is fully customized to suit each application and, because of its modular design, tonnage capacities can be increased or the separation cut-point altered at a later date at minimal cost to the customer. This, combined with the machine’s impressive wear performance, has seen demand for the CDE compact plant grow throughout the world. Most recently, CDE have installed a compact plant in the Middle East that is operating 22h a day in 45°C heat, to produce 22,000 tonnes of sand a day, seven days a week.
Water treatment
Meanwhile, the –75 micron waste material and the water used for washing the 6–0mm material passes to a CDE T-08 high-rate thickener for treatment. Upon entry into the thickener, the material is mixed with a small amount of flocculant, which is prepared by an integrated polyelectrolyte dosing station. Once in the thickener tank the material quickly begins to form a thick sludge that settles towards the bottom of the tank, while clean water overflows the top of the tank and is sent to a separate storage tank for recirculation around the plant.
At the same time, a set of rakes rotate around the bottom of the thickener tank moving the sludge towards the centre and preventing it from setting. The rakes also send information about the amount of resistance back to the central PLC control panel, which automatically starts and stops the main sludge pump as required. The thickened sludge is sent to a buffer tank for further treatment by the filter press.
First filter press
The GHT overhead-beam filter press is a result of a partnership between CDE and their Italian partners Diemme, who have over 40 years’ experience in filtration technology. The overhead-beam filter press – a heavy-duty machine specifically designed for the quarrying industry – successfully eliminates the problems often associated with the more commonly used side-bar design. The GHT is capable of 24h unmanned operation and is noted for the dry, easily handled waste filter cake it produces, without the use of any additional chemicals or flocculant.
[img_assist|nid=12258|title=CDE GHT filter press|desc=|link=none|align=right|width=266|height=200]The unit installed by CDE for Liam Lynch – understood to be the first overhead beam filter press in Ireland – is a GHT.1200.P6 containing 64 plates and operating at approximately 16 tonnes/h. The press is fed by a pump that draws the thickened sludge from the buffer tank and pumps it in between the plates, which are then compressed under high pressure. The unit is mounted on two concrete walls and the dry filter cakes (comprising between 80–90% dry solids content) are discharged directly to the ground. The clean water is recycled and piped back into the system, reducing the site’s fresh-water requirements to an absolute minimum. The filter press also completely removes the need for settling ponds, saving valuable site space and eliminating the health and safety risks associated with such ponds.
‘There are numerous advantages to the filter-press technology that we can offer,’ said Terry Ashby, CDE’s general manager for the UK market, who added that the filter press on display on the company’s stand at the recent Hillhead show had proved to be one of their most popular exhibits, with people beginning to realize the financial, logistical and health and safety benefits to be gained from using this technology.
CDE say the Liam Lynch system has demonstrated, similar to previous CDE systems, that the traditional barriers to washing waste products, such as quarry dust, have been relegated to the past. They add that traditional systems, such as bucket wheels or screw classifiers, tend to fall short when dealing with this type of material, generating excessive and difficult to handle waste and producing a poorer-quality washed sand, often with an unacceptably high moisture content.
According to the company, innovative new washing systems mean that typical quarry dust can now be efficiently and consistently washed to provide concrete sand for use in ready-mixed concrete batching, reducing the requirement for bought-in natural sand. Likewise, any washed grit/aggregate which is also produced can be used in the manufacture of concrete blocks. And even if no on-site concrete sand requirement exists, the added-value washed sand output can be sold at a greater premium than the original raw dust.
‘We are delighted to have been awarded this contract by Liam Lynch and believe that we have delivered a truly innovative plant,’ commented CDE sales director Enda Ivanoff. ‘The approach we take in the design and manufacture of these systems is unique and the level of business we are winning on an international scale at the present time provides evidence for this,’ he said.
A detailed video of the Liam Lynch project is available from CDE. To obtain a copy, email your name, company name, postal address and email address, as well as a contact telephone number, to: pcraven@cdeireland.com.
For further information about any of the issues raised in this article, or any other enquiries, call CDE on tel: (028) 8676 7900; fax: (028) 8676 1414; email: info@cdeireland.com